Why invest in a friction stir welding machine?
Because of its wide range of applications, the friction stir welding machine offers many advantages for manufacturers. Designed to adapt to the most specific requirements, the FSW machine has now been adopted in all cutting-edge sectors…
Friction stir welding (FSW) is a solid-state welding process that combines heat generated by friction with mechanical pressure to join metals.
This heat softens the materials, which are then mixed together to form a solid, homogeneous bond when they cool. It is therefore an innovative welding method that has a number of advantages over other processes.
But what is exactly an FSW machine? How does it work? What types of machines exist today? And what are its advantages in the welding sector? TRA-C industrie takes a look at this revolutionary tool in this article…
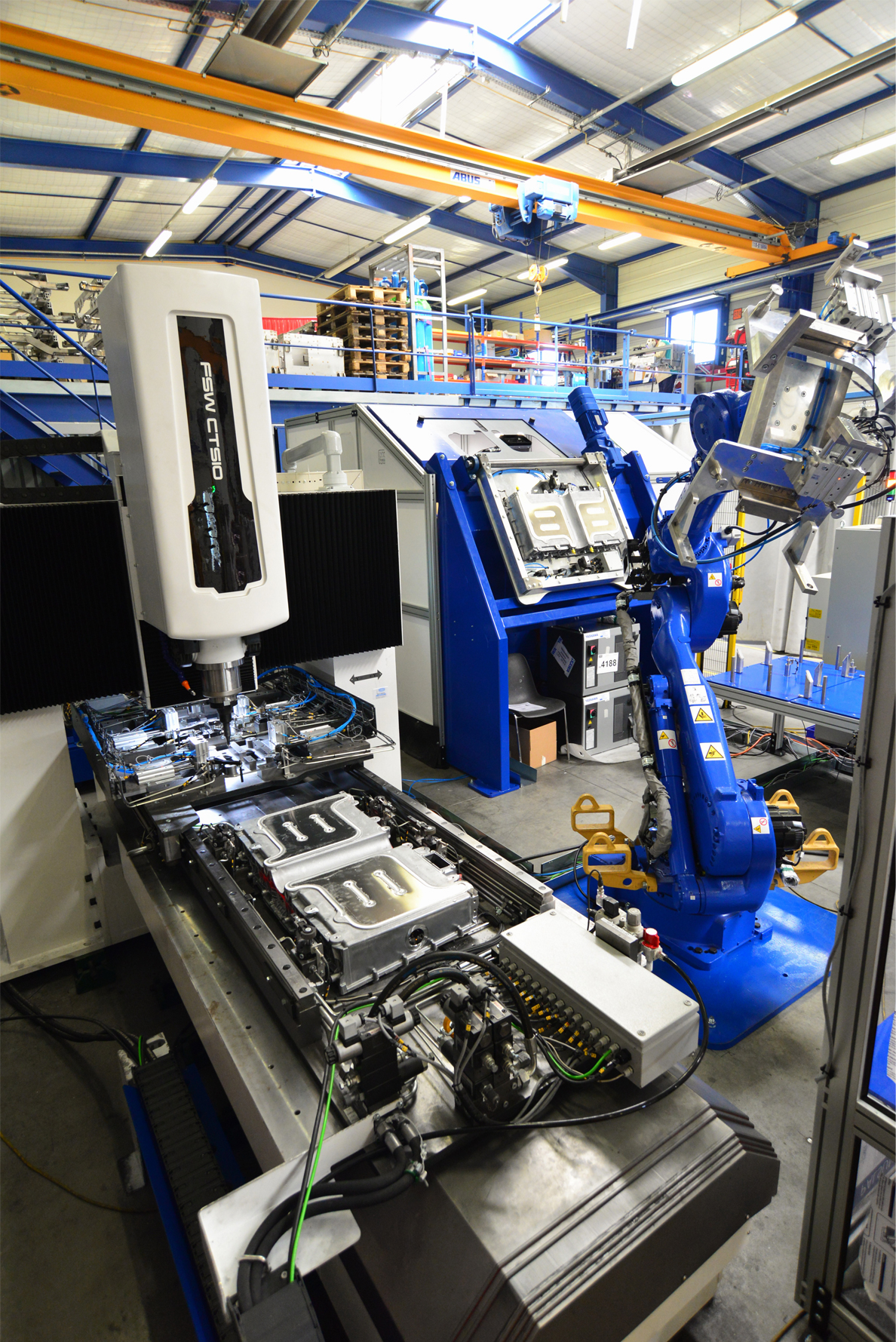
What components make up a friction stir welding machine?
A friction stir welding machine is designed to perform a mechanical welding process using a combination of friction, pressure and controlled movement. Here are the main components of a conventional FSW machine:
- The pin: this is the central element of the machine. It is a threaded tip that penetrates the parts to be welded. It rotates at high speeds during the welding process;
- The shoulder: cylindrical or conical in shape, this is the part precedes the pin. It exerts constant pressure on the materials to generate heat through friction;
- The anvil: this supports the parts to be welded during the welding operation. It can be adjusted to suit different workpiece shapes and sizes;
- The clamping system: it holds the parts to be welded firmly against the clamping plate during welding to ensure close contact between the surfaces to be welded;
- The movement system: this system moves the spindle and/or the parts to be welded according to specific parameters, such as speed and direction, in order to weld along the joint line;
- The in-situ control system: this is the ‘brain’ of the machine. It controls all aspects of the welding process, such as the speed of rotation and the force applied by the pin, as well as the movement of the workpieces. It therefore guarantees continuous quality.
How does a friction stir welding machine work?
A friction stir welding machine operates in 5 key stages:
- Positioning of the parts. The parts to be welded are first placed on the tool, then held firmly in place with the clamping system;
- Penetration. The tool is then rotating with the machine spindle and inserted into the components to be welded;
- Pre-heating. A waiting phase allows the material to heat locally and bring the tool up to temperature;
- Welding. The welding head is then moved along the interface to be welded, forming a mechanical bond. The combined effect of strain, rotation and movement generates friction which produces heat. The materials to be welded then enter a pasty state, allowing them to be mixed;
- Removing the tool. At the end of the welding process, the tool is finally removed, leaving an exit hole characteristic of the process.
The usual FSW parameters to be considered when welding are as follows:
- The speed of rotation expressed in revolutions per minute
- Feed speed expressed in millimetres per minute
- The normal force expressed in kN
- The tilt angle is expressed in degrees. It allows better forging of the material while improving the surface finish of the welded joint.
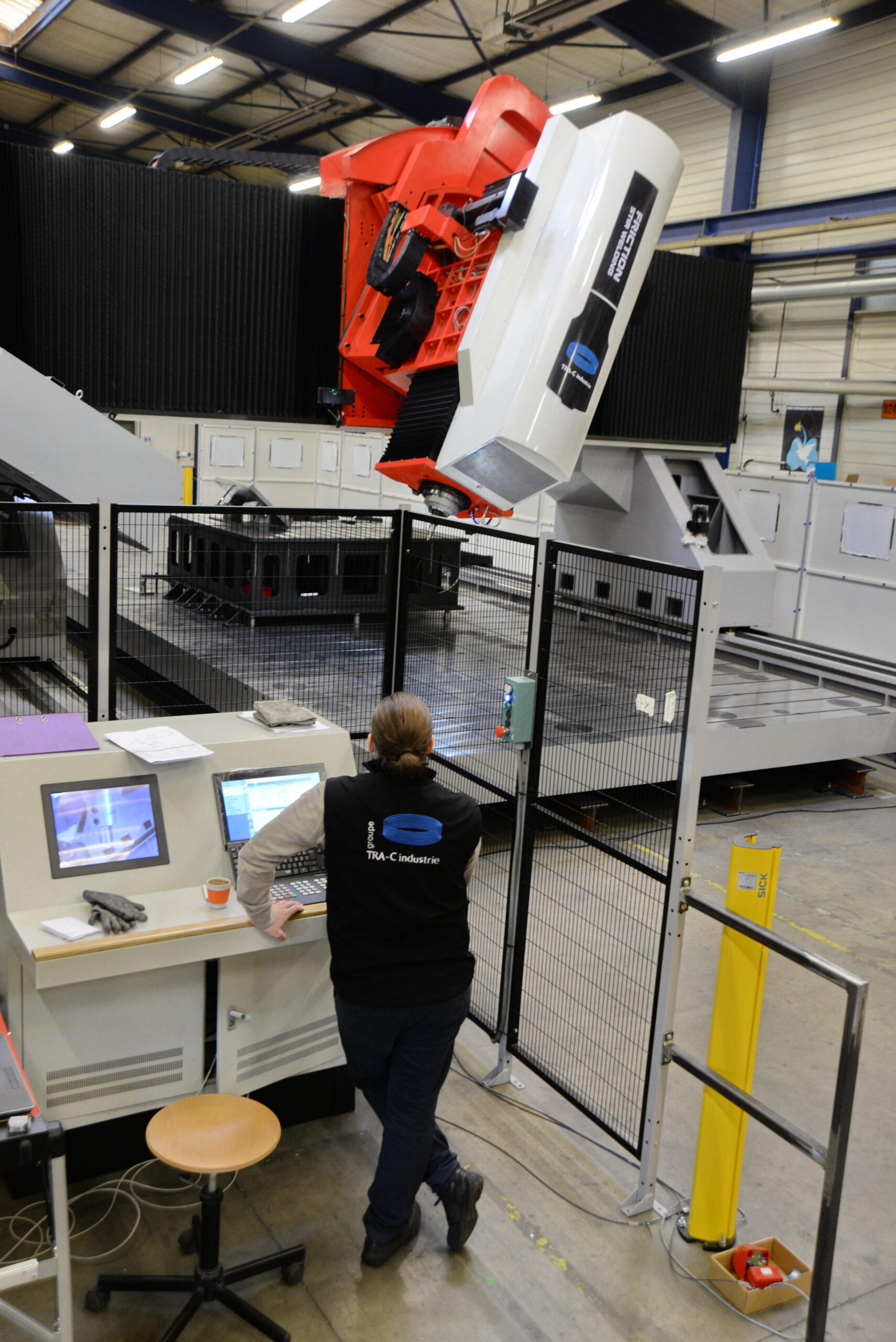
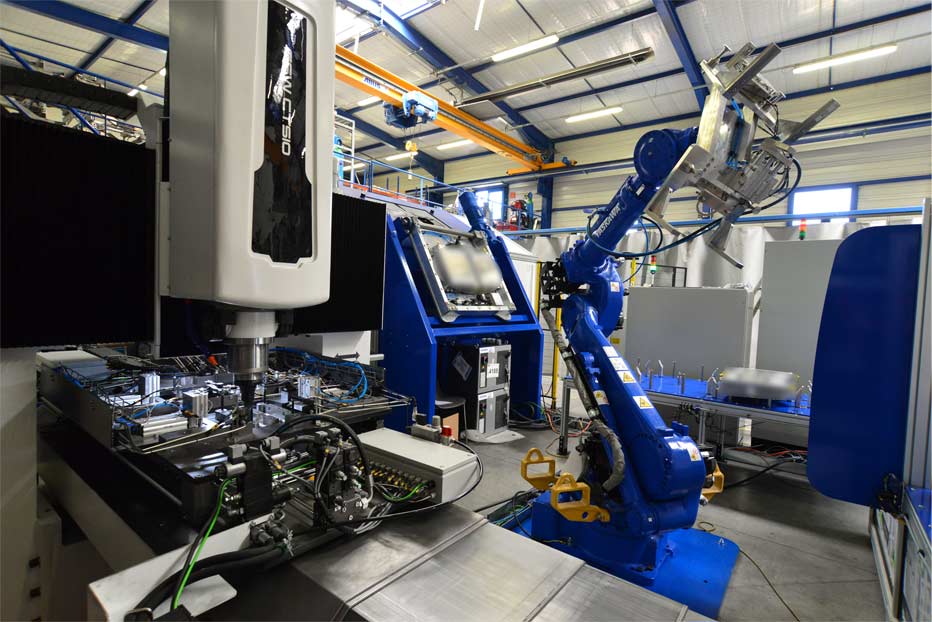
What friction stir welding machines are there?
There are several types of friction stir welding machine available today, each adapted to specific applications according to industrial needs. The most commonly used machines include:
- The table-top machine: used to assemble small parts in the X and Y axes. It is ideal for use in research laboratories and training centres;
- The gantry machine: it is composed of a table that moves along the X axis and a welding head that moves along the Y and Z axes. With its higher rotation speed, it is particularly suitable for mass production;
- The rail machine: mounted on rails, this machine is able to weld long components. It is therefore perfect for assembling structural panels in the rail and aerospace industries;
- The robotised FSW machine: the FSW head is installed on an industrial robot to weld various thin-walled shapes. It can also be programmed for automated operations on production lines;
- The twin-spindle FSW machine: finally, this machine is equipped with rotating spindles operating in tandem. It is ideal for welding applications requiring bidirectional access or for welding complex parts.
What are the advantages of investing in an FSW machine?
Economic benefits
First of all, investing in a friction stir welding machine saves on material costs compared with conventional welding machines. As the process takes place in a solid state, there is no material input. The absence of electrodes or shielding gas also makes the process easier to use!
The FSW machine also welds faster than other methods, resulting in shorter production cycle times. Companies can therefore increase their productivity and meet market demand more quickly.
Finally, FSW machines are designed to be durable. They require less maintenance than welding machines. Maintenance costs are therefore lower…
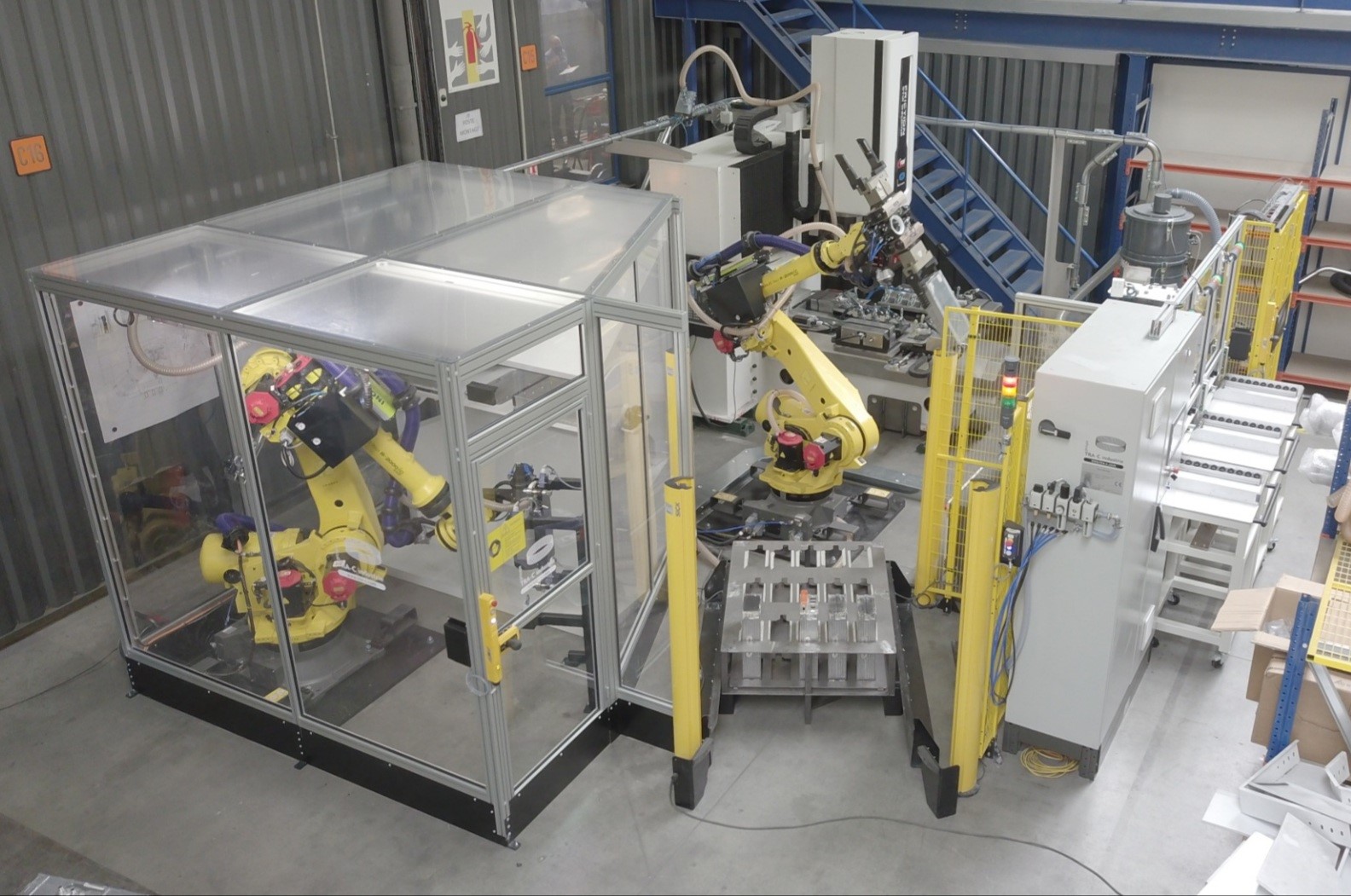
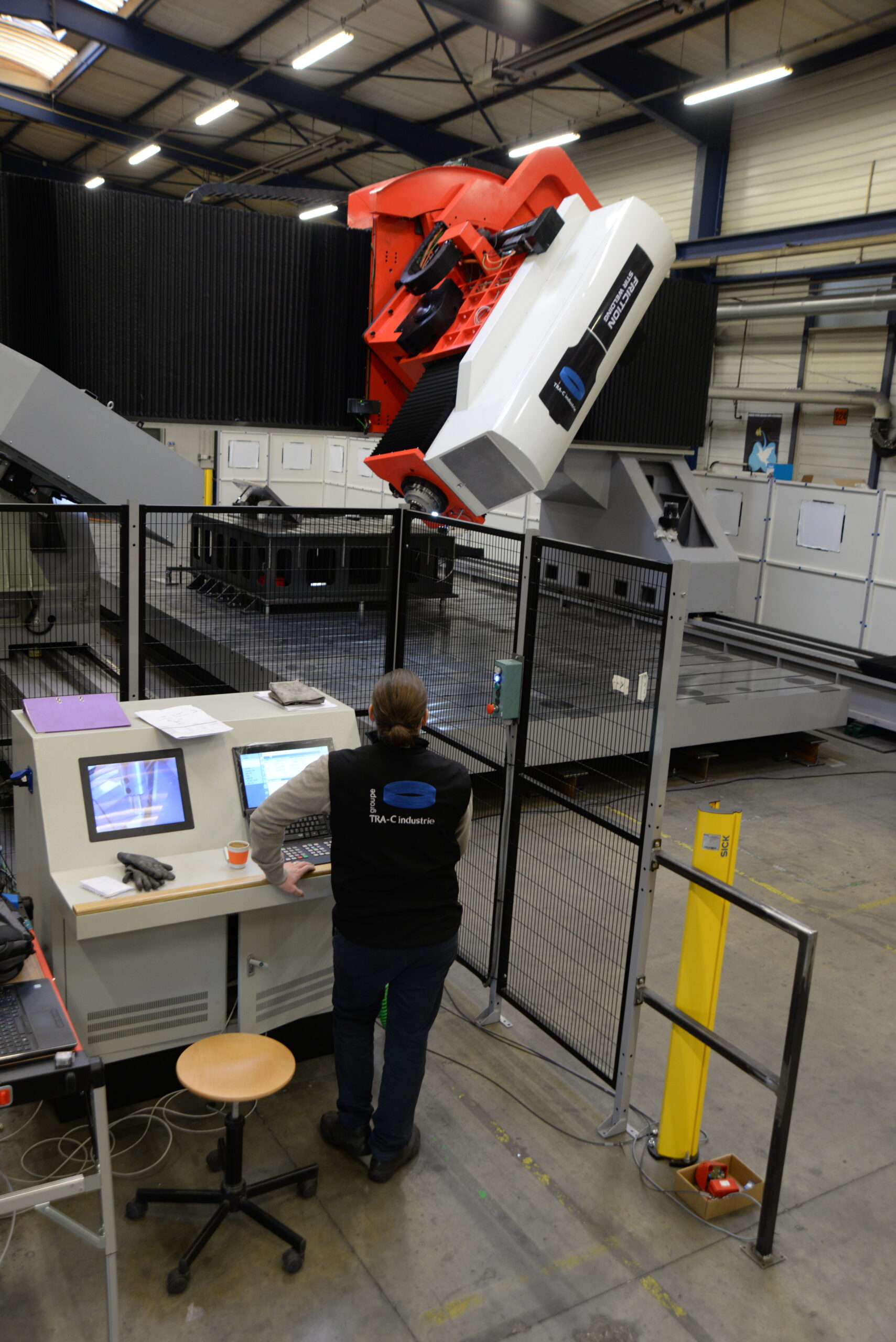
Welding quality
Welds produced with a friction stir welding machine are homogeneous and have a high level of structural integrity. By mixing the materials, the metal components are evenly distributed along the weld zone.
Solid state welding limits the problems of solidification or rapid cooling associated with fusion welding methods. Once qualified, the FSW process therefore produces welded joints without major defects such as porosities, cracks or inclusions. The parameters associated with each application can be used repeatedly.
In FSW, the parts are also welded at lower temperatures, which minimises thermal stresses. There is generally less deformation than with other welding methods, particularly those involving high heat.
Diversity of applications
The FSW machine can assemble a wide range of materials that are difficult to weld using conventional methods. These include aluminium, magnesium, titanium and their alloys…
This versatility means that high quality welds can be produced for a variety of industrial applications. Friction stir welding is particularly well suited to the needs of the aerospace, military and naval industries.
The FSW process also offers great flexibility in terms of part design. Assemblies are lighter, stronger and more efficient, which is ideal for the automotive and e-mobility sectors.
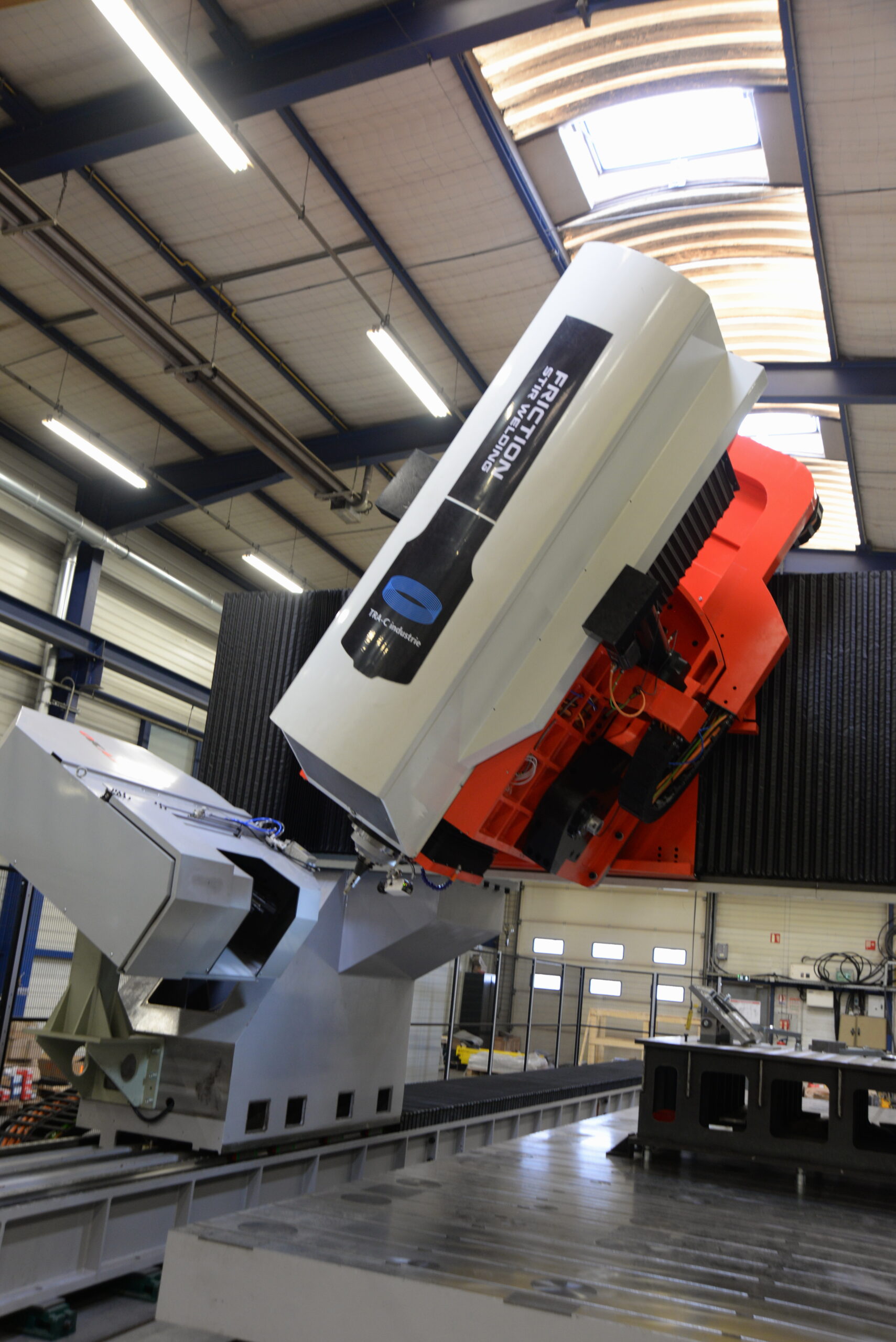
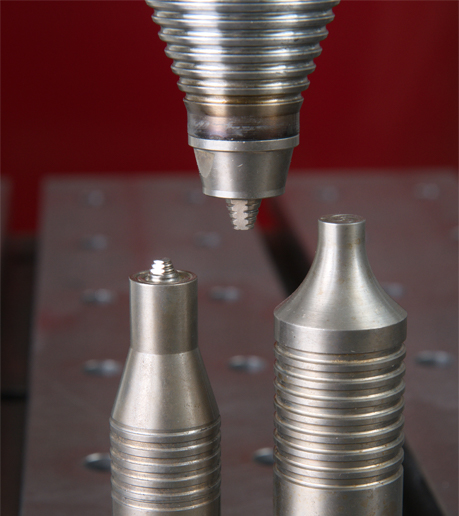
Environmental interests
The friction stir welding machine is environmentally friendly. It consumes less energy during the welding process than some traditional techniques as it does not require an intense external heat source…
Some arc welding techniques use a shielding gas to prevent oxidation of the molten metal. This is not the case with FSW. This helps reducing the greenhouse gas emissions associated with its production and use.
Finally, the FSW machine produces less waste than conventional welding methods, since it does not use consumables such as electrodes or filler materials. Remember that the manufacture of the filler metal accounts for 50% of the CO2 emitted. This limits the processes involved in eliminating or recycling them!
How to choose the right friction stir welding machine?
Most friction stir welding machines are tailor-made to suit the specific needs of the user. Several aspects therefore need to be taken into account to guarantee high-quality assemblies:
- Geometric proportions: choose them to satisfy accessibility, quality criteria and weld configurations depending on the application;
- Specific applications: specify your requirements in terms of materials to be welded, part thicknesses, joint geometries and quality specifications to the manufacturer so that the FSW machine can meet these criteria;
- Machine capacity: also stipulate the dimensions and weight of the parts you plan to weld. The FSW machine must be able to assemble long panels or mass-produced parts without compromising the quality of the weld;
- Flexibility and versatility: depending on the configuration of the parts, opt for a machine that can move along different axes, load and unload in hidden time, or even weld in 3 dimensions. This will enable you to cover a wide range of applications and projects;
- Reliability and durability: when designing your machine, use a manufacturer with a reputation for the reliability and durability of its tools. A reliable machine will require less maintenance and last longer;
- Automation and control: features such as digital control, real-time monitoring and automatic programming make welding operations easy. Ask the designer to add these features if you want to mass-produce;
- Technical support and training: make sure the manufacturer also offers maintenance, repair and training services for your technicians. A responsive after-sales service is essential to help you out when you need it;
- Acquisition cost: finally, evaluate the purchase, maintenance, operating and training costs for your FSW machine. Build a machine that will give you the best revenue.
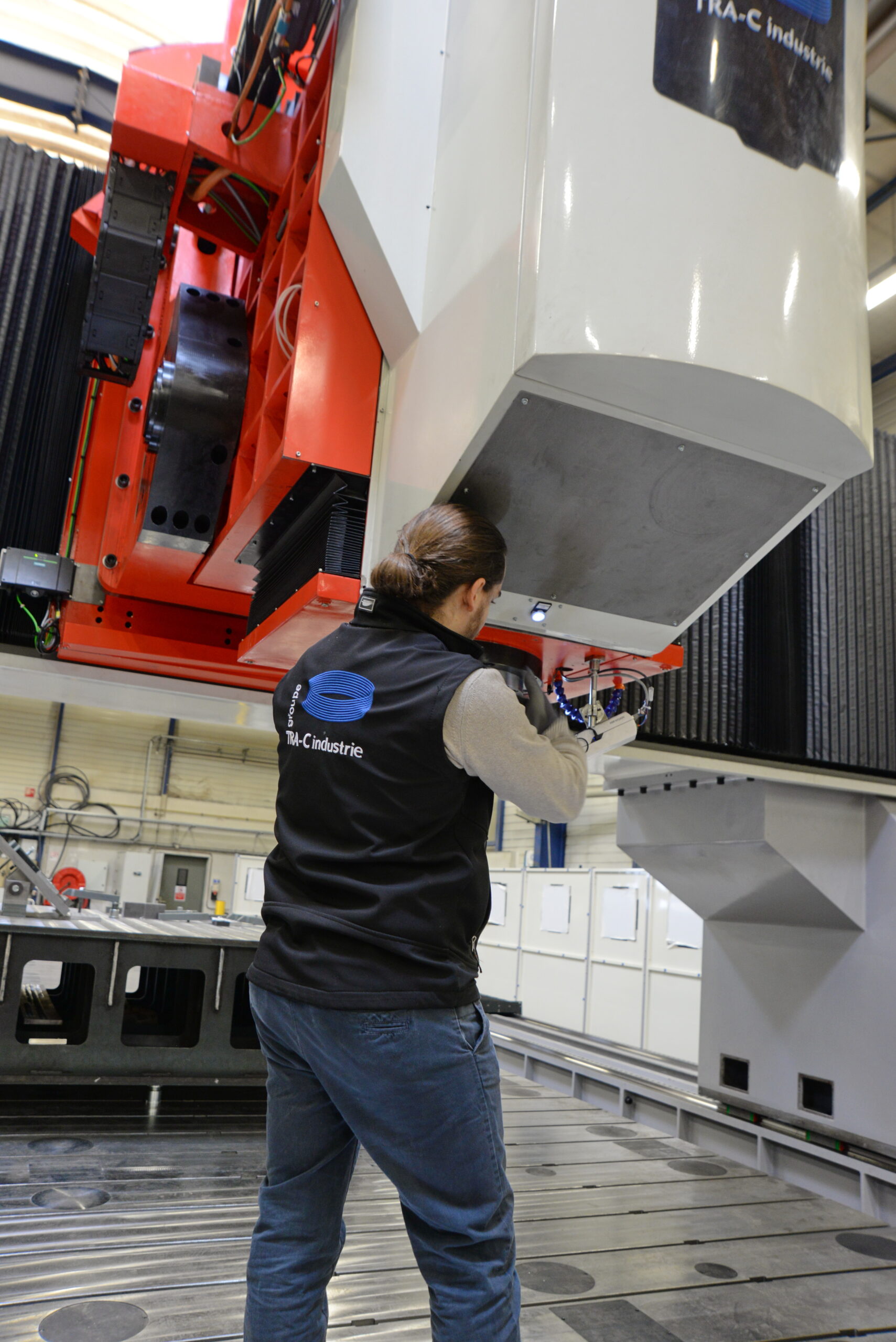
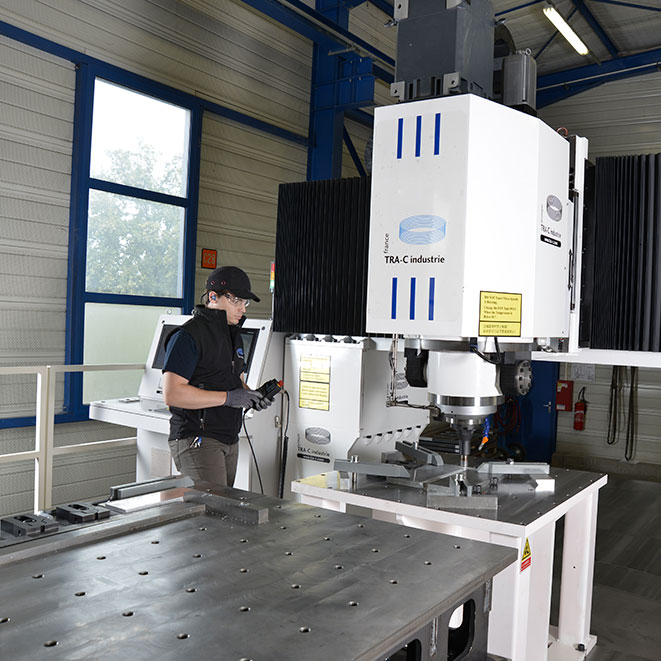
TRA-C industrie, expert in the design, development and installation of FSW machines
With 9 production sites in France, a technical design office and a workshop in Canada, TRA-C industrie is now the European leader in friction stir welding. We support manufacturers at every stage of their welding projects.
We are experts in the development, design, prototyping and on-site installation of your friction stir welding machine. We can also train your teams in its use and offer you a maintenance contract!
TRA-C industrie is also an integrator: we can load and unload your welding robots, deburring stations, integrate cells on your manufacturing execution system (MES), etc.
Finally, you can count on our strong experience in FSW to subcontract your industrial projects. Our FSW machines allow us to meet all your needs: prototyping, testing, mass production of assemblies, welding of thin (0.8 mm) or thick (40 mm) parts, etc.