Industrial sheet metal work refers to all the processes involved in transforming sheet metal to create a variety of parts, used in a wide range of sectors. Thanks to a number of techniques, it is possible to manufacture customized components, combining precision and robustness.
An essential part of modern industry, sheet metal work has adapted to the requirements of sectors such as automotive, aeronautics and construction. The evolution of machines and the integration of digital technology have considerably improved productivity and manufacturing quality.
Beyond technical performance, sheet metal processing plays a key role in product innovation and durability. The use of new materials and efforts in eco-design make this a constantly evolving field, responding to industrial challenges.
But what is the sheet metal industry? What are the different stages in sheet metal production? And what materials and machines are commonly used? In this article, TRA-C industrie tells you more about sheet metal design and assembly...
Industrial sheet metal work, a specific metal work process
Industrial sheet metal work, and in particular fine sheet metal work, is a highly specific metal fabrication process. This cutting-edge field of metallurgy enables extremely precise and meticulous processing of different types of metal.
It can be used for metal parts as well as thin products (a few millimeters thick). Thanks to its cutting, bending and assembly techniques, it offers great flexibility in the manufacture of customized components.
Its advantages include excellent dimensional accuracy and the ability to adapt to the specific needs of each sector. It enables the design of parts, which are lightweight, robust and functional, optimizing the performance of end products!
Last but not least, the rise of digital technologies and automation has further enhanced its efficiency. Improved production processes reduce costs, minimize waste and promote a more sustainable approach to metal processing.
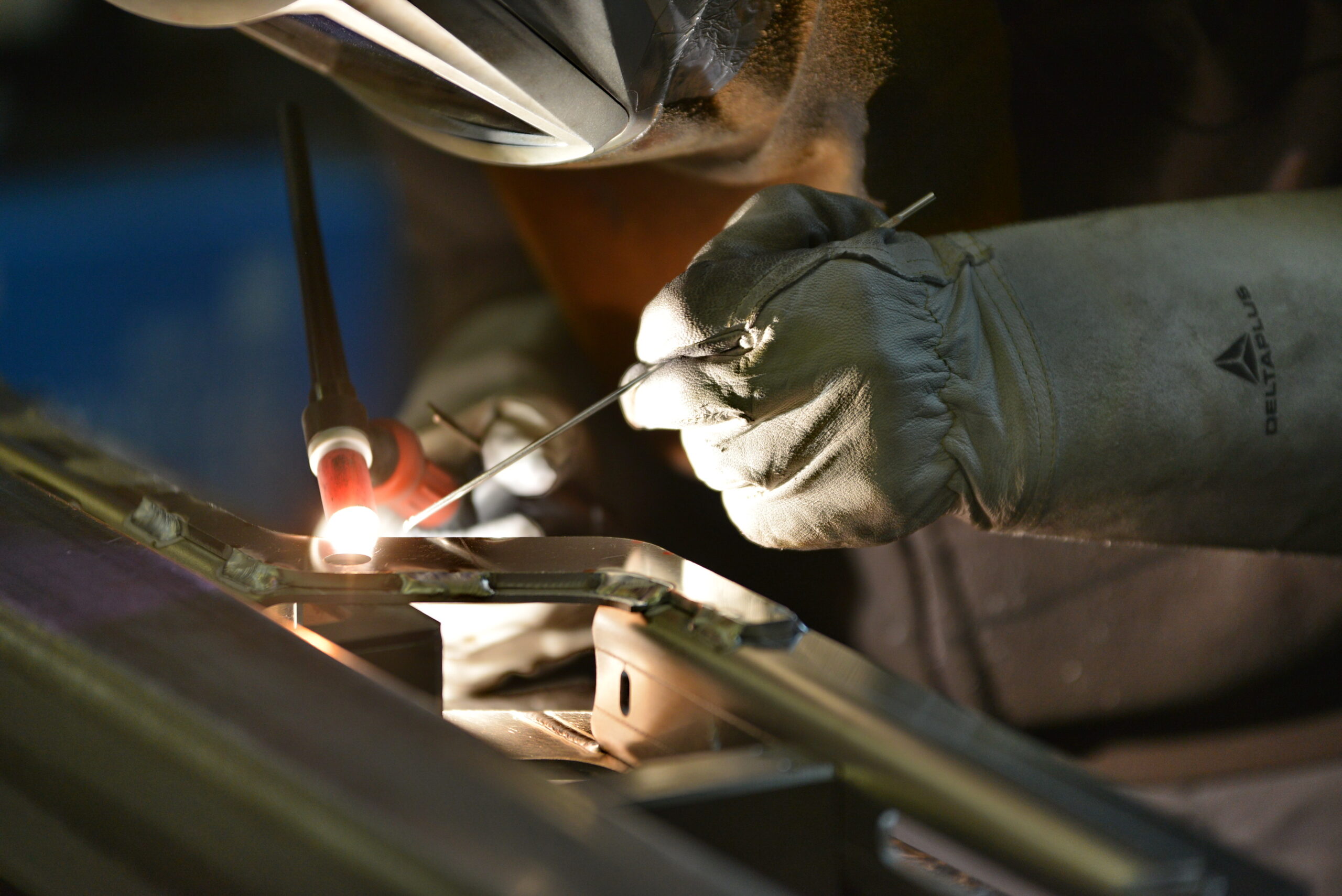

Rolling: the art of transforming metals into thin sheet metal
Rolling is a key process in metallurgy, which consists in reducing the thickness of a metal by compressing it between rolls. This technique produces thin sheets with precise dimensions, adapted to industrial needs…
There are two types of rolling: hot and cold. Hot rolling, carried out at high temperature, facilitates metal deformation, while cold rolling improves strength and surface finish.
This technique relies on sophisticated equipment, such as industrial rolling mills made up of several rolls exerting controlled pressure. These machines can process a variety of metals, including steel, aluminum and copper.
Thanks to this process, metals retain their mechanical properties while gaining in homogeneity. Rolling is used in many sectors, including aeronautics, automotive and construction.
The main stages in sheet metal work
Industrial sheet metal work involves several successive stages to transform a simple sheet of metal into a functional part. Each phase calls on specific techniques to guarantee precision, strength and quality:
- Cutting: using laser, plasma or punching techniques, precise shapes can be produced to suit industrial requirements;
- Bending: this stage consists of giving the sheet metal a curved shape using a press brake, without altering its structure;
- Stamping: by deforming under pressure, it creates complex hollow or raised shapes, ideal for certain industries;
- Welding and assembly: the parts are then fastened together using various processes (TIG, MIG, spot welding) to ensure their solidity;
- Surface treatment: aims to improve the resistance of parts to corrosion and wear, by galvanizing, painting or anodizing;
- Assembly and finishing: the next step is to assemble the various components and check their conformity before shipping;
- Quality control: finally, tests and inspections are carried out to ensure that parts comply with customer standards and requirements.
What are the differences between fine sheet metal work and industrial sheet metal work?
Fine sheet metal work and industrial sheet metal work are two distinct branches of metalworking, each serving specific needs. The main difference lies in the thickness of the sheet metal used and the precision of the operations performed.
Fine sheet metal work mainly involves the manufacture of thin metal parts, often less than a few millimeters thick. It is favored in high-precision sectors such as electronics, aeronautics and medical engineering…
In contrast, industrial sheet metal work encompasses a wider range of thicknesses and forming techniques. It is used to produce more robust parts for fields such as construction, automotive and mechanical engineering.
While fine sheet metal working relies on meticulous attention to detail and high-precision processes, industrial sheet-metal working stands out for its ability to handle large volumes and more imposing structures. So, depending on the application, the two approaches complement each other.
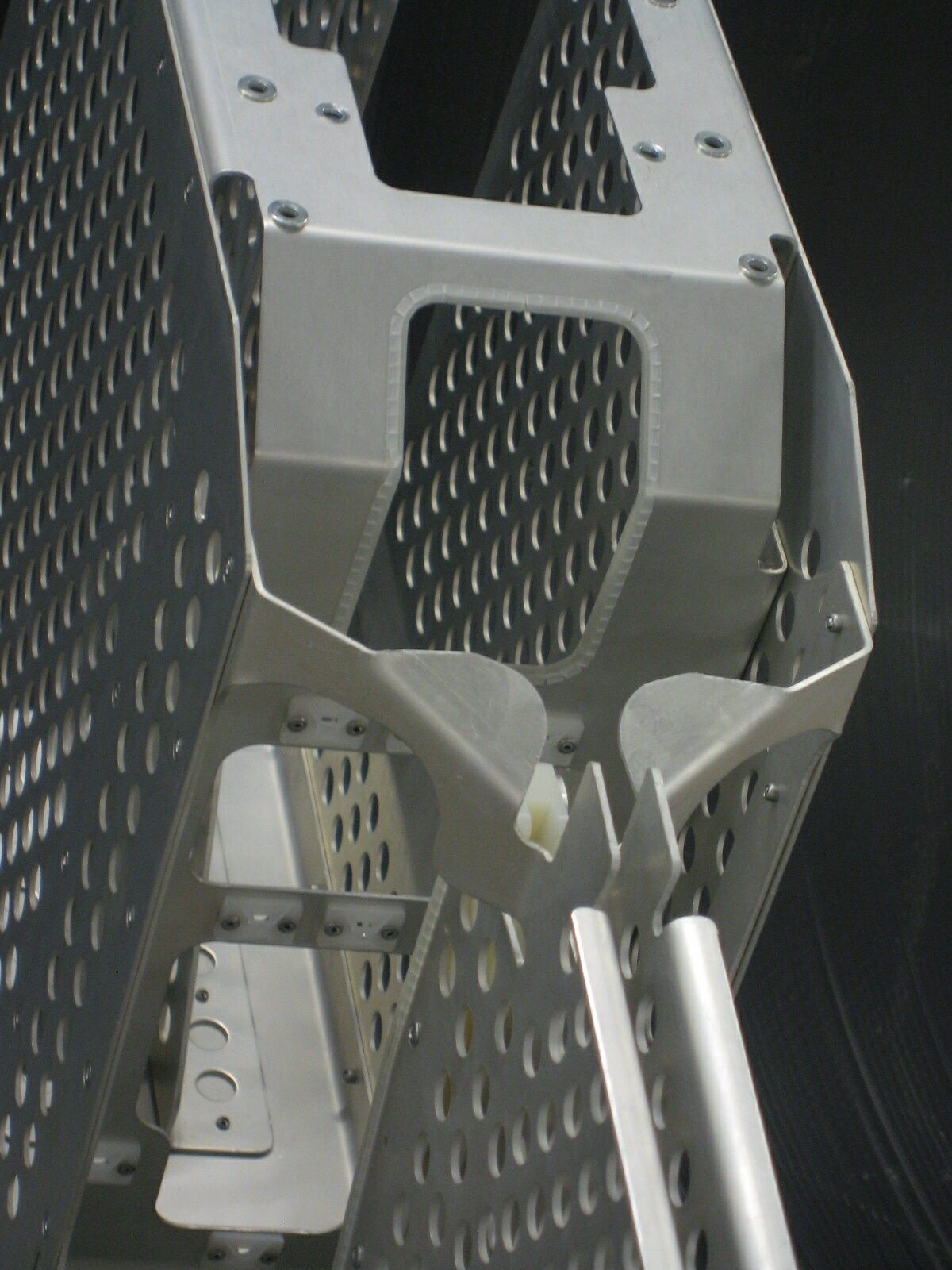
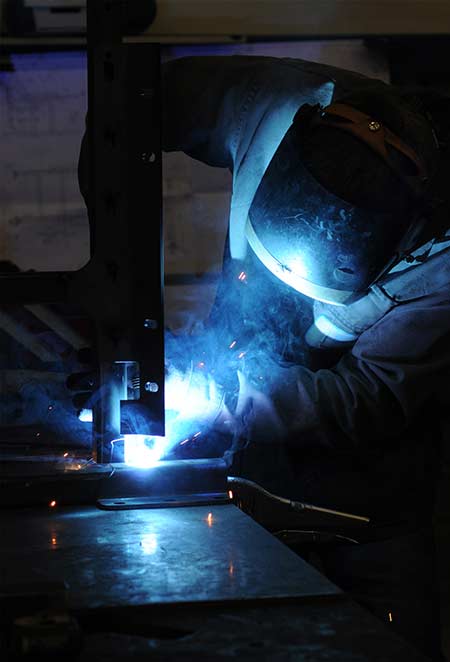
Materials used in industrial sheet metal work
The sheet metal industry uses a wide range of metallic materials, each with properties adapted to specific uses. The choice of metal depends on the mechanical, thermal and environmental constraints of the parts to be manufactured.
Steel is one of the most common materials, appreciated for its strength and impact resistance. It is used in construction, automotive and industrial structures.
Aluminum, which is lighter and more resistant to corrosion, is favored in aeronautics and electronics. But also, for equipment requiring low weight, such as in the e-mobility sector. Its malleability also facilitates cutting and forming operations.
Finally, stainless steel is chosen for its anti-corrosion properties and durability. Widely used in the food, medical and chemical industries, it guarantees excellent hygiene and long part life!
Sheet metal tools and machines
Industrial sheet metal work relies on a wide range of tools and machines to cut, bend, weld and assemble metal sheets. Automation and digital technologies have considerably improved the precision and speed of operations.
Cutting machines include plasma, waterjet and laser cutting, each offering precision tailored to the requirements of the industry. Mechanical punching is also used to drill and shape sheet metal in mass production.
Press brakes and rollers are used for bending and forming, enabling to achieve precise angles and complex shapes. This equipment ensures efficient forming while preserving the integrity of the material…
Finally, assembly and welding machines play a key role in the manufacture of metal structures. Thanks to MIG, TIG or spot-welding processes, they guarantee durable and solid assemblies, adapted to industrial constraints.


Industrial sheet metal work applications
Industrial sheet metal work is used in a wide range of sectors, thanks to its ability to produce personalized metal parts. Its versatility enables it to meet the technical and aesthetic requirements of a wide range of industries:
- Automotive: manufacture of bodies, chassis and mechanical parts combining lightness and strength;
- Aeronautics: production of aluminum and stainless-steel structures and components to guarantee performance and safety;
- Building and construction: production of facades, metal frameworks and sheet metal joinery;
- Household appliances: design of metal casings for ovens, refrigerators and other domestic appliances;
- Street furniture: manufacture of benches, bus shelters and other equipment in steel or aluminum for public spaces;
- Electronics and high-tech: creation of protective enclosures for sensitive circuits and components;
- Agri-food and medical: production of stainless-steel equipment to ensure hygiene and compliance with health standards.
Developments and trends in the sheet metal industry
The industrial sheet metal work sector is constantly evolving, driven by technological innovation and new market requirements. The integration of automation and robotization, for example, enables significant productivity gains.
The advent of Industry 4.0 is also transforming the sector, with the use of connected machines and advanced production management software. These technologies promote better product traceability and real-time optimization of manufacturing processes.
The use of innovative materials is another key trend. High-strength steel, light alloys and composite materials are increasingly in demand for their enhanced performance, particularly in the automotive and aerospace sectors.
Finally, environmental concerns are driving the sector towards more sustainable production. Recycling metals, reducing emissions and optimizing resources are becoming priorities for industrial sheet-metal working companies…
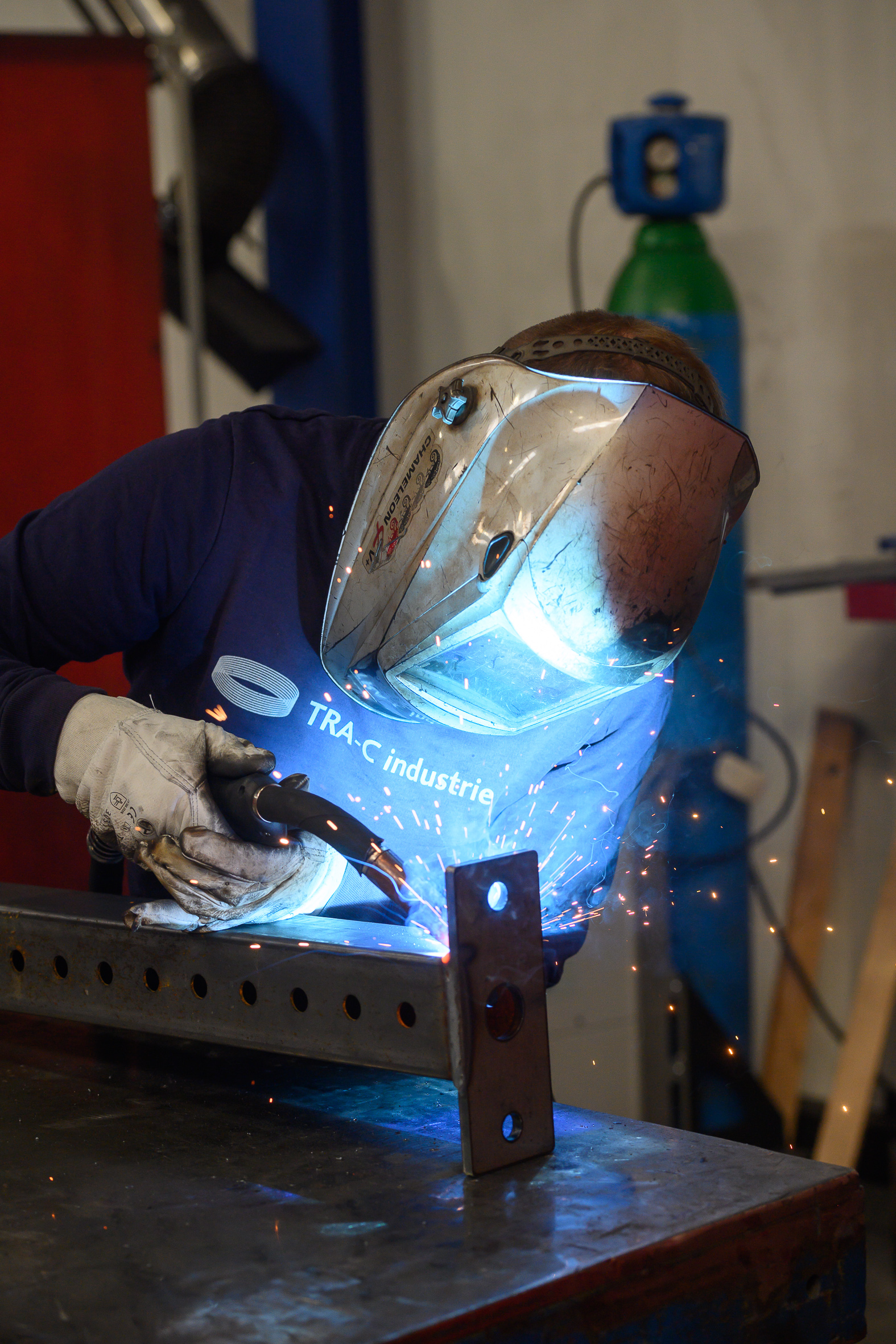
TRA-C industrie: expert in fine sheet metal work and industrial sheet metal work
TRA-C industrie is your partner of choice for precision and industrial sheet metal work. Thanks to a highly qualified team and the robotization of our machines, we are able to carry out complex projects while optimizing production costs.
Experts in the field of welding, we are recognized as European leaders in FSW welding. We also master all welding techniques, such as TIG, MIG, MAG, orbital and resistance welding, to meet your diverse needs.
Our latest-generation laser cutting ensures speed and precision, guaranteeing clean cuts, even for complex shapes. TRA-C industrie also excels in bending, industrial painting and the production of complex assemblies.
We also have the ISO certification, know-how and equipment needed to produce sub-assemblies using automated, pneumatic or electromechanical components. All within your budget and time constraints.