What are the main welding processes?
Welding processes are at the heart of the manufacturing and construction industries, enabling various materials to be durably joined together. Whatever the sector, these techniques are essential to ensure strong, reliable structures.
Each welding process has its own specific requirements, depending on material type, part thickness and application conditions. Among the most common are arc, MIG and TIG welding, each with its own advantages and limitations.
Evolving technologies have perfected these methods, making welding more precise and adapted to modern requirements. From robotization to innovations in materials, processes have constantly evolved to meet growing technical challenges.
But what are the main welding techniques available today? In this article, TRA-C industrie shares the main processes, their characteristics and applications in various sectors, to give you a better understanding of their specific features and importance!
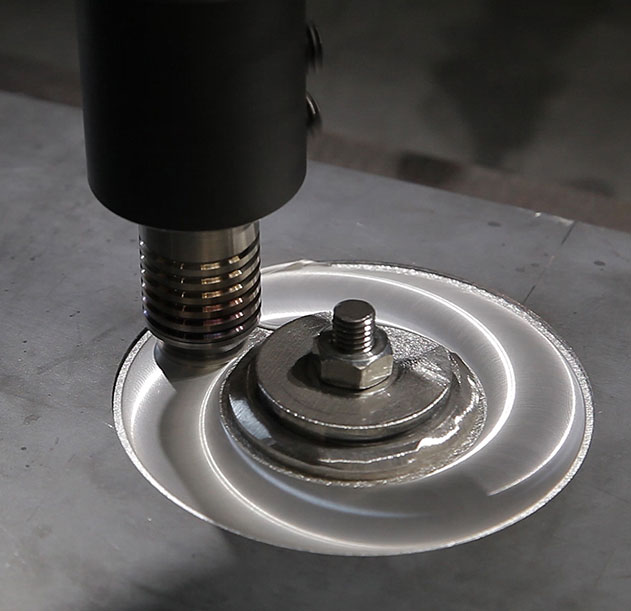
Welding processes adapted to each material
The aim of welding is to create permanent continuity between two metal elements, with or without filler metal. This is achieved either by melting, pressing or stirring, and without altering the properties of the materials.
Depending on the characteristics of the metal or alloy, the technique to be adopted differs, with different types of welding possible:
Within these different techniques inherent to the nature of the materials used, there are several welding processes, some of which have benefited from major technological innovations.
Electric arc welding
Electric arc welding produces intense energy, generating sufficient heat to bring metals to their melting point thanks to their resistivity. This technique uses a welding unit delivering direct current for heavy metals and alternating current for light metals or alloys.
With or without the addition of metal, this technique can be adapted to all thicknesses and types of metal. This generic principle can be broken down into several specific techniques. It thus offers a variety of solutions to meet a wide range of needs in metal construction…
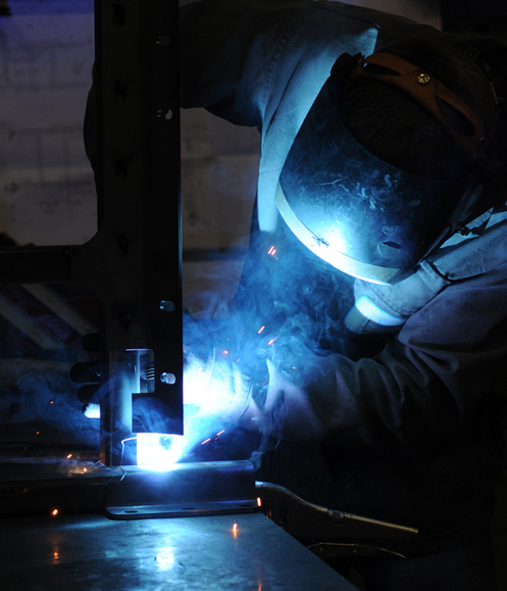

TIG welding
Amongst welding processes is TIG welding, which stands for Tungsten inert gas. With or without filler metal, it uses an electric arc to create a molten pool. This is achieved using a non-melting tungsten electrode and an inert gas, hence its name.
The arc is formed between the electrode and the component to be welded, under gas shielding, guaranteeing a very high-quality weld. This makes TIG particularly effective for assembling thin-walled parts with precision and reliability!
MIG and MAG welding processes
In this semi-automatic process, an electric arc is formed between the part to be joined and a fusible wire electrode, causing the metals to fuse together. MIG welding uses a metal inert gas, while MAG welding uses a metal active gas…
A wire-feed mechanism continuously feeds the wire to the welding arc at a controlled speed. These two welding processes can be used to produce large volumes of parts, or to produce long welds quickly, ideal for the marine industry.
Plasma welding
Plasma, an ionized material, represents the fourth state of matter after solid, liquid and gas. Plasma welding generates exceptionally intense heat, ideal for high-precision applications.
This process is distinguished by its ability to produce welds that are extremely fine, unobtrusive. It is therefore particularly well suited to work on very thin components, down to 50 microns thick.
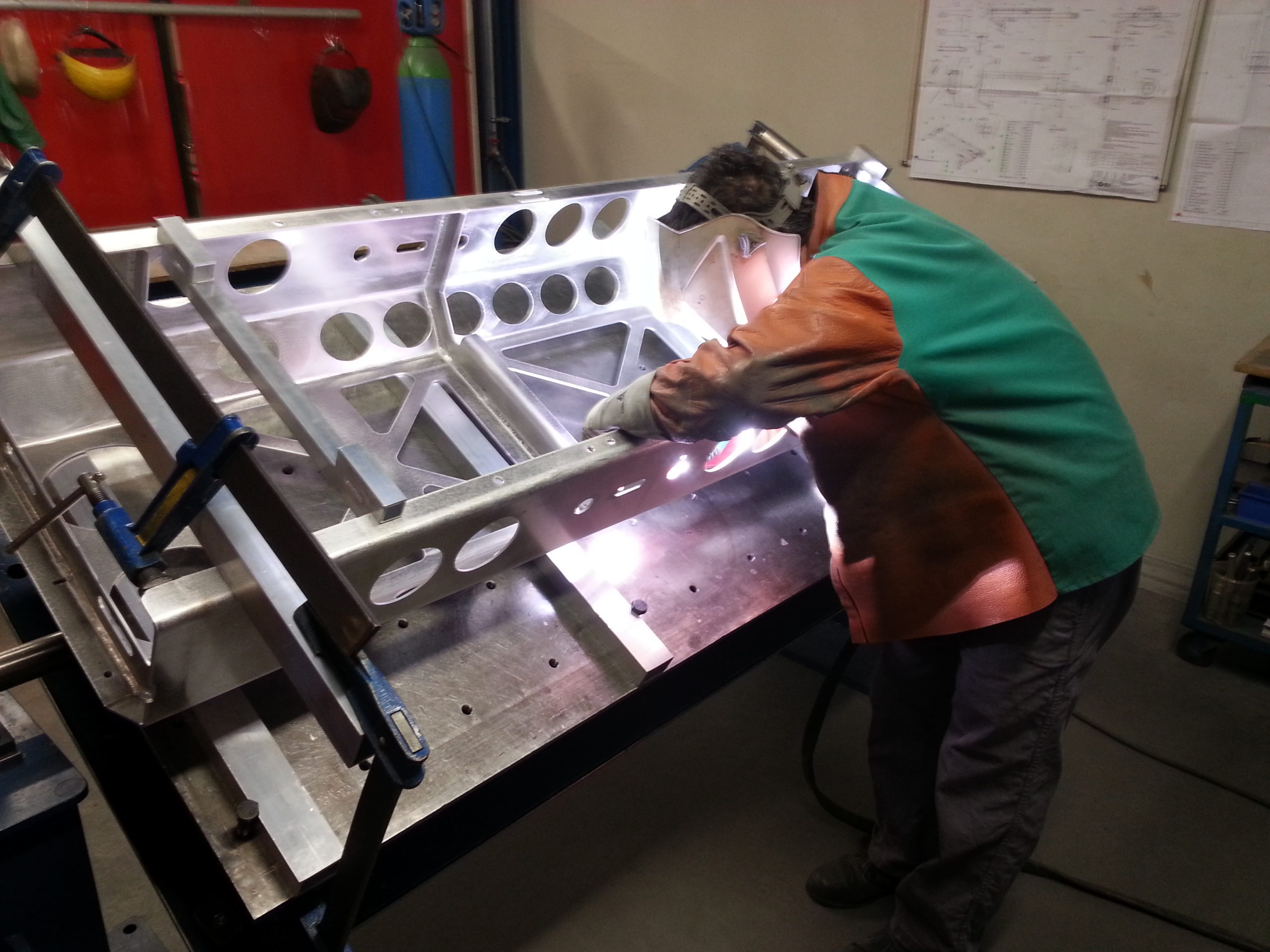
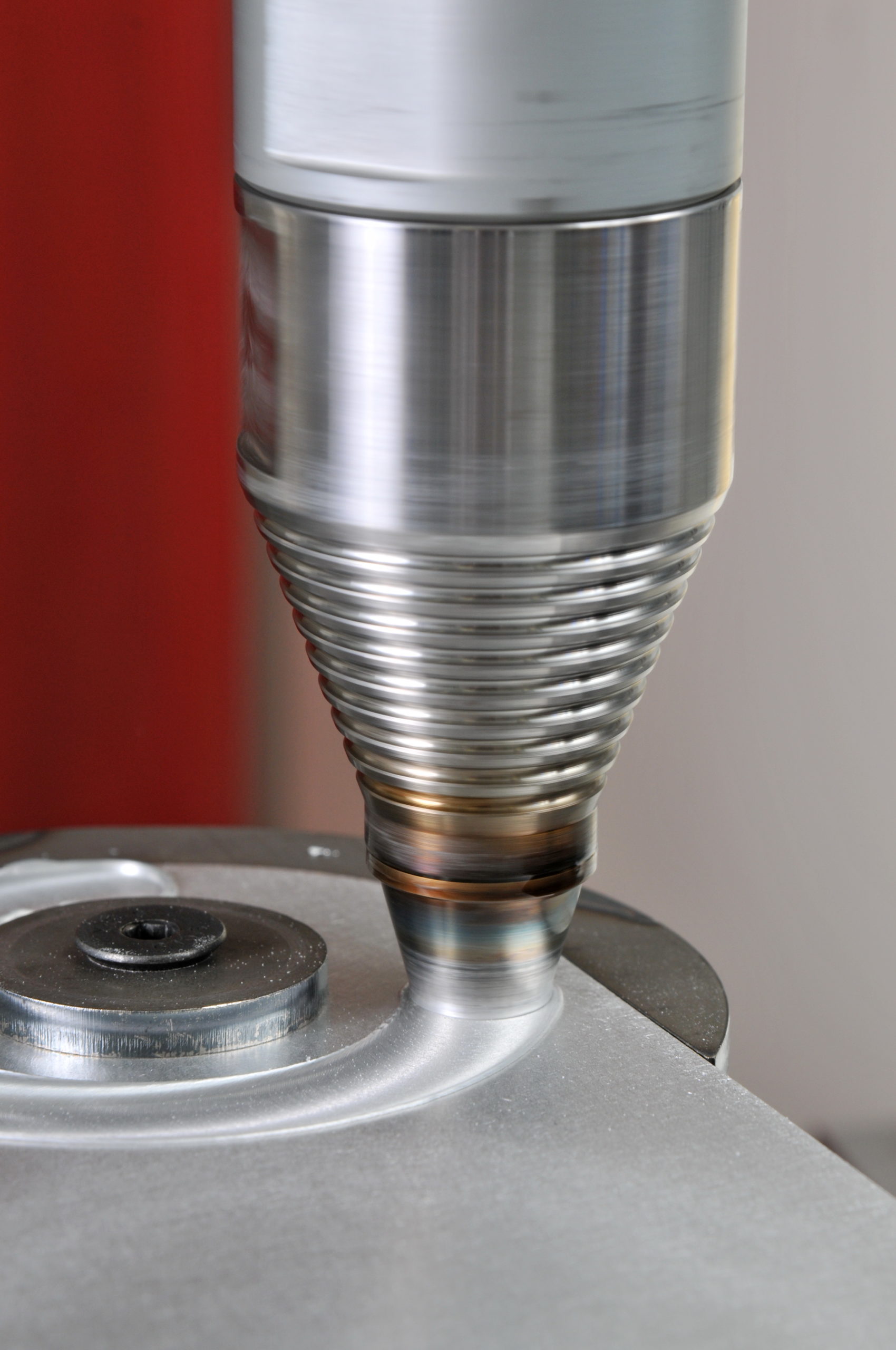
Laser welding
The special feature of laser welding is its ability to heat up quickly and extremely intensely. The metal melts and vaporizes in a matter of microseconds, without the need for filler metal, offering high precision.
This high-energy density process produces perfectly sealed joints, with excellent mechanical strength and low deformation. It is particularly well suited to the manufacture of specific structures in sectors such as railways…
Orbital welding
Orbital welding is an automated process in which the electrode makes a circular movement around the part to be welded, usually a tube or pipe. This precise movement produces high- quality welds, particularly suited to assemblies in controlled environments.
This process is ideal for guaranteeing aesthetic and homogeneous welds with low distortion. It is widely used for applications requiring perfectly sealed joints, such as the pharmaceutical, food and chemical industries.
The friction stir welding process
Friction stir welding (FSW) uses the heat generated by friction to mix and fuse materials. A rotating tool exerts pressure on the parts to be joined, locally heating the metal to its plastic state, enabling welding without complete fusion.
Particularly well-suited to lightweight materials such as aluminum and titanium, FSW is in great demand in the aerospace industry. Friction stir welding processes offer the advantage of producing strong, precise joints, with low distortion and no filler metal!
Resistance welding
Finally, resistance welding (SPR) enables the fusion of conductive metals without the addition of metal. An electric current heats the parts to their melting point. It can therefore be used to join thin parts or sheets, edge-to-edge or overlapping.
Efficient and clean, resistance welding minimizes distortion and generates little pollution. It is particularly used in the automotive industry, guaranteeing fast, precise assemblies and reliable results.
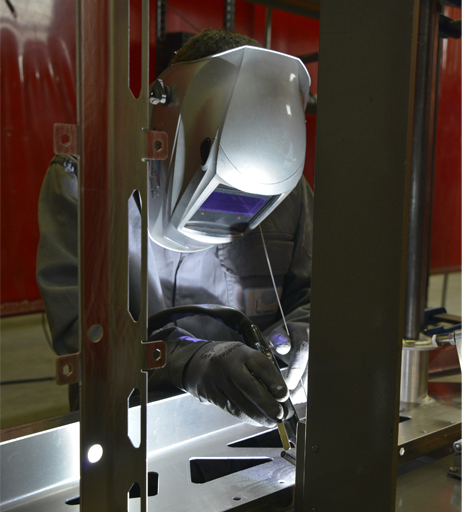
Call on an expert to choose the right welding processes
The equipment supplier provides customized, high-performance and cost-effective solutions. Its expertise in mechanical welding, as well as its ability to meet technical challenges by combining digital tools and industrial applications, are part of its mission.
This approach enables to meet the varied needs of modern industries, where every project requires a tailor-made solution. By combining technical know-how and innovation, this professional becomes a key partner in the manufacture of complex structures.
TRA-C industrie stands out for its in-depth expertise in welding processes. We offer high- performance solutions tailored to the specific requirements of each sector. We use advanced technologies to guarantee high-quality, safe and reliable welds.
As a key player in the field of mechanical welding, TRA-C industrie is able to meet all kinds of technical challenges. We combine state-of-the-art equipment and qualified welders to offer customized services in a wide range of industrial sectors.