Welding automation and robotization: principles and benefits
Welding automation is a major challenge for manufacturers today, and offers significant competitive advantages. The key benefits are increased productivity, quality and safety for operators, as well as reduced costs, errors and waste…
This process aims to infinitely reproduce a set of repetitive tasks in order to guarantee uniformity of operations and simplify complex processes. It also enables welders to concentrate on higher added-value tasks.
In the welding industry, automating a production line increases the possibilities for a company. Many applications in virtually all sectors of activity use this method.
But what does automated welding actually involve? What are the automation tools? And what are the advantages? In this article, TRA-C industrie tells you more about the benefits and principles of robotization and industrial automation.
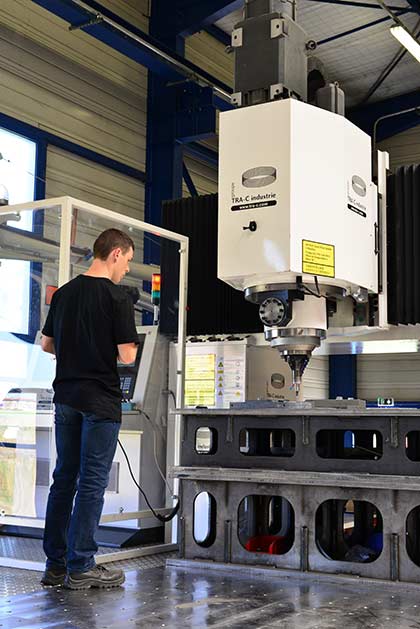
What is welding automation?
Welding automation consists of carrying out welding operations semi-automatically or automatically. The aim of this production method is to partially or totally reduce human intervention.
The plant and equipment then weld autonomously, without the need for manpower. This process is carried out to several degrees, from partial automation at certain stages of the work to complete automation of the entire production line.
Automating a production line requires electronic and IT systems, industrial robots, automated cells and machines. These different units are linked together to ensure that all operations run smoothly.
Finally, a line operator supervises these operations. He monitors production progress, checks compliance with quality criteria, makes any necessary adjustments and provides first-level maintenance.
The different automated welding technologies
Welding automation uses different equipment and systems depending on the needs and stage of production. These include:
- Standard machines: these are used for a wide range of common applications. They are versatile, but cannot perform specific tasks;
- Special machines: these are designed and optimized to meet very specific needs, such as automating complex processes, taking measurements or carrying out checks;
- Industrial robots: they are programmed to carry out specific tasks such as welding, assembly, handling or manipulating materials. Unlike machines, they can adapt to new tasks as required;
- Automated systems: they use position or quality sensors, cameras and lasers. They enable the parts to be welded to be detected and tracked, and welding parameters to be monitored and adjusted in real time;
- Programmable controllers: these include software for creating and modifying welding programs. They also include human-machine interfaces (HMI) to facilitate interaction between operators and automated systems.
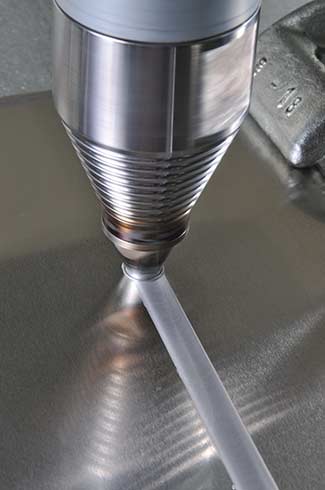
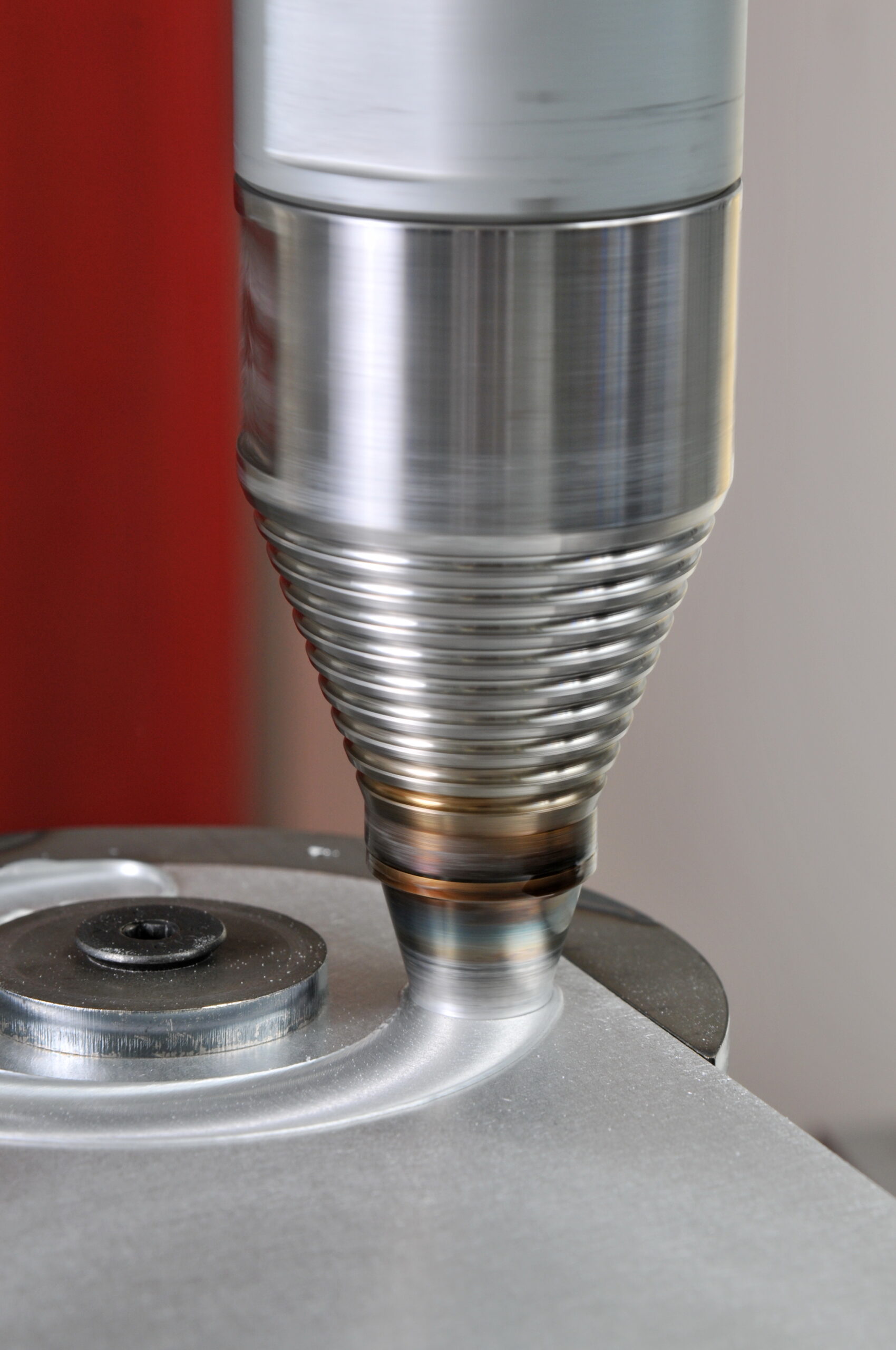
Examples of welding automation applications
Welding automation has applications in various industrial sectors, each with its own specific requirements:
- Automotive industry: welding robots are commonly used to assemble vehicle chassis. Automated production lines are used to weld body panels, structural components, battery trays and heat exchangers;
- Aerospace sector: automation is needed for welding critical aircraft components, such as wings, fuselages and engine bases. But also, for the structures of spacecraft and satellites, for example;
- Shipbuilding: production lines are also used to mass-weld the steel plates that make up the hulls of ships and river barges, as well as the internal structures, compartments and maritime containers;
- Energy sector: automated welding is effective for the mass assembly of turbines, penstocks, wind turbine structures and solar panel supports;
- Rail industry: automated systems finally make it possible to repeatedly weld components produced in large numbers, such as the frames, rails and structures of train wagons.
What are the advantages of automated welding?
Reducing labor costs
Automated welding involves high initial costs, since an industrial design office must first be called in to design a production line tailored to the company’s needs. The various welding machines, electronic systems, computer software and robots also have to be designed and integrated.
Apart from maintenance, however, automated welding remains a profitable investment over the long term. All you need is a line operator and a few technicians to supervise operations and carry out maintenance.
This reduces the cost of hiring and training qualified welders, and offers a solution to labor shortage. However, operators remain essential to ensure smooth running of the machines and cannot be entirely replaced.

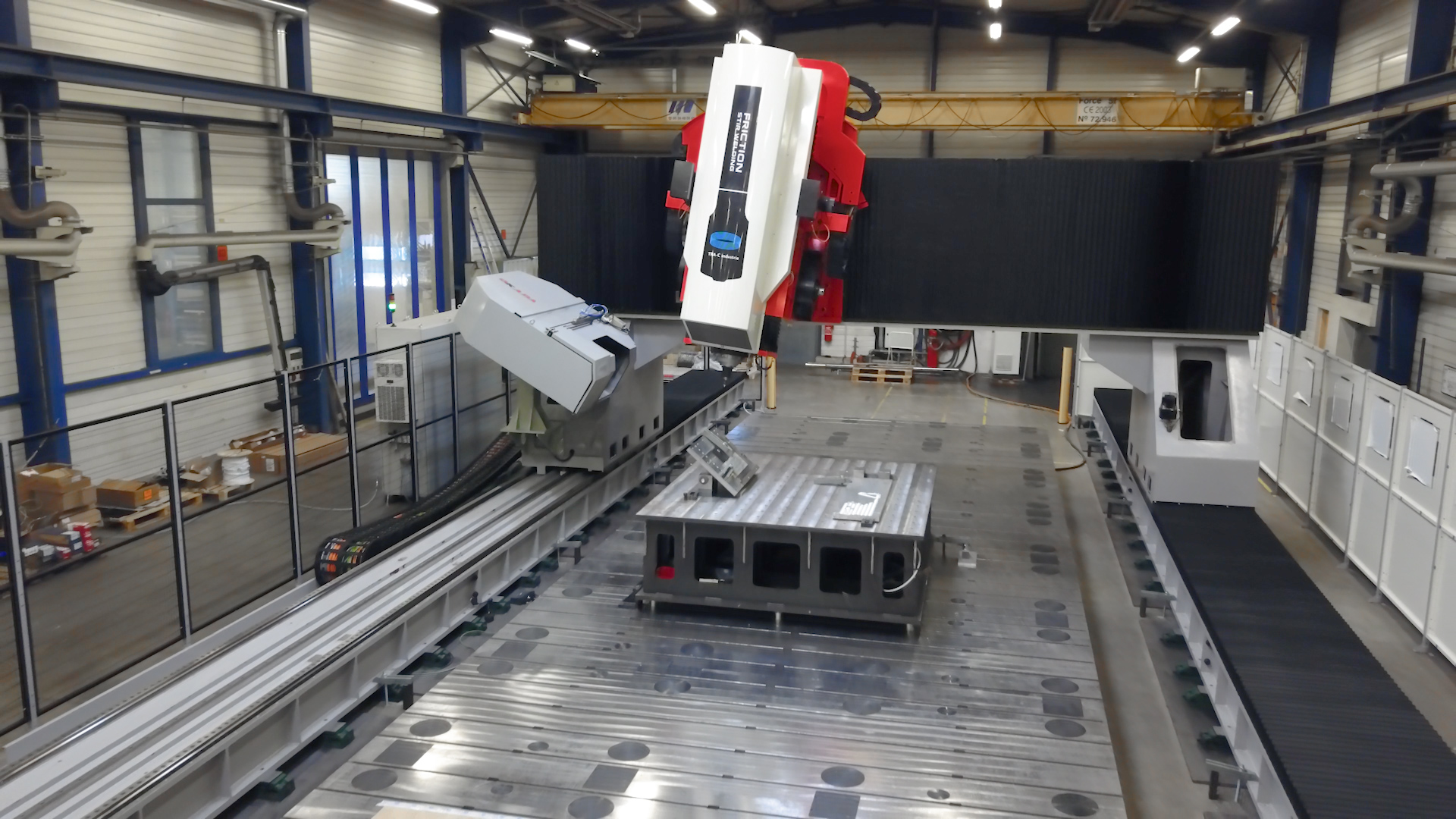
Increasing productivity
Unlike human beings, automatic machines and industrial robots operate 24/7. They carry out tasks in an optimized and continuous manner, with each work phase following on from the next with no breaks.
Even in the case of three 8-hour shifts for personnel, operations are carried out faster and more uniformly than manual work. This means that more welds can be made in the same time.
Improving operator safety
Thanks to factory automation, it is now possible to delegate repetitive, monotonous, complex or even dangerous tasks to machines. This considerably reduces the risk of accidents due to inattention or fatigue.
Operators are also less exposed to the shielding gases, fumes, heat, material splashes and sparks generated by arc welding. They can supervise production remotely, behind a screen, which guarantees their safety.
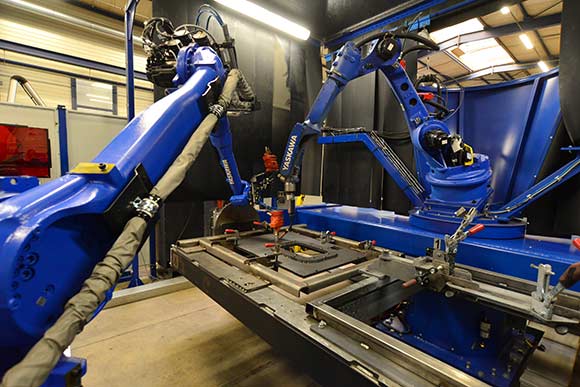

Limiting errors and non-conformities
Thanks to automated welding, simple operations are carried out less and less manually by workers. Machines and robots can perform the same movements under the same conditions, which greatly reduces errors.
Welding automation also makes it possible to simplify complicated processes and to trace digital data, which is now mandatory. As a result, companies are able to comply with directives and meet customer specifications more effectively.
Improving quality and customer satisfaction
Reducing the error rate and optimizing processes for each machine improves the quality of welds. Each parameter is programmed upstream and monitored to ensure that production is tailored as closely as possible to requirements.
It also helps to speed up manufacturing processes and meet deadlines. The result is greater customer satisfaction. They will be more inclined to entrust their future welding projects to the company.
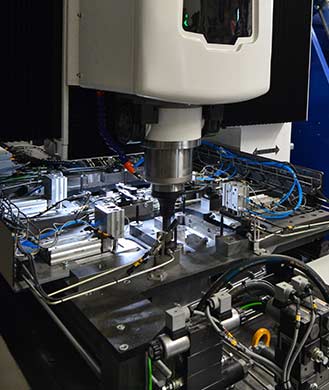
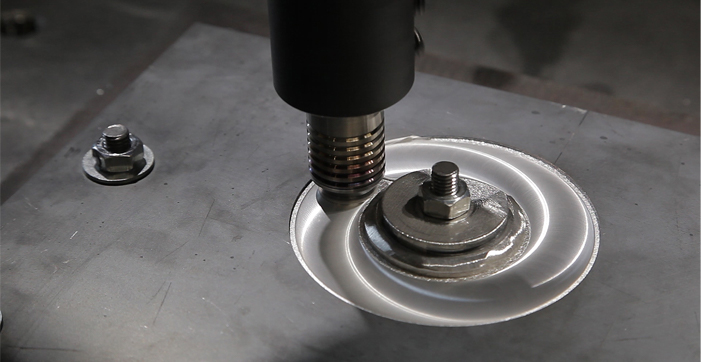
Reducing waste and greenhouse gases
Thanks to welding automation, it is finally possible to produce welds in an environmentally-friendly way. It means less material is wasted, and fewer consumables and shielding gases are used in arc welding processes.
This optimization of resources is made possible thanks to the reduction in non-conformities and non-welding times, which have no added value. But also, because of the high precision offered by the machines and the adjustment of the welding parameters.
Take advantage of TRA-C industrie expertise in welding automation
Although welding automation and robotization are of great interest in the industrial world today, their implementation remains complex. Design, integration, test phase, optimization… It can be useful to call on the expertise of a professional.
As a true systems integrator, TRA-C industrie works with SMEs, key accounts and prime contractors to automate their production lines. Through our industrial design office, we optimize all your processes.
We also design, manufacture and integrate your automated cells, industrial robots and special machines. We are at your side from the analysis of your specifications to the maintenance of your equipment, including the training of your operators.
Qualified and experienced, our teams can advise you whatever your needs to automatize your welding process. Whatever your sector of activity: rail, shipbuilding, aerospace, defense, automotive, etc.