Thin sheet welding: everything you need to know about the process
Thin sheet welding is an essential technique in many fields, from the automotive industry to the manufacture of metal objects. It enables to assemble thin parts with precision, while preserving the integrity and aesthetics of the material.
Mastering thin sheet welding requires specific skills and the use of suitable tools. Thin sheet metal is particularly sensitive to heat, making process control essential to avoid deformation and defects.
This type of welding is distinguished by its many applications and the challenges it poses. Craftsmen and welders have to choose between various techniques, such as TIG or MIG, depending on the needs of the project and the properties of the metals to be worked.
But what are the particularities of thin sheet metal work? What are the challenges of welding on thin sheet? In this article, TRA-C industrie takes a look at the different processes involved in this metalworking technique…
Special features of fine sheet metal work
Metal rolled into thin sheets, often less than 1 mm, is used to manufacture small parts. It can be found in a wide variety of sectors, including the automotive, aeronautics, street furniture and household appliance industries.
These sheets can be used to create small, complex structures in steel, aluminum, stainless steel or other alloys. They can take a variety of shapes, such as tubes or profiles, depending on requirements…
Thin sheet welding requires extreme precision to avoid holes, deformations and stresses. This work differs from assembly work on large parts, such as structural steelwork.
Success requires specialized equipment and expertise. Industrial sheet metal work and thin sheet assembly require unique technical skills and dexterity to guarantee high-performance, long-lasting welds.
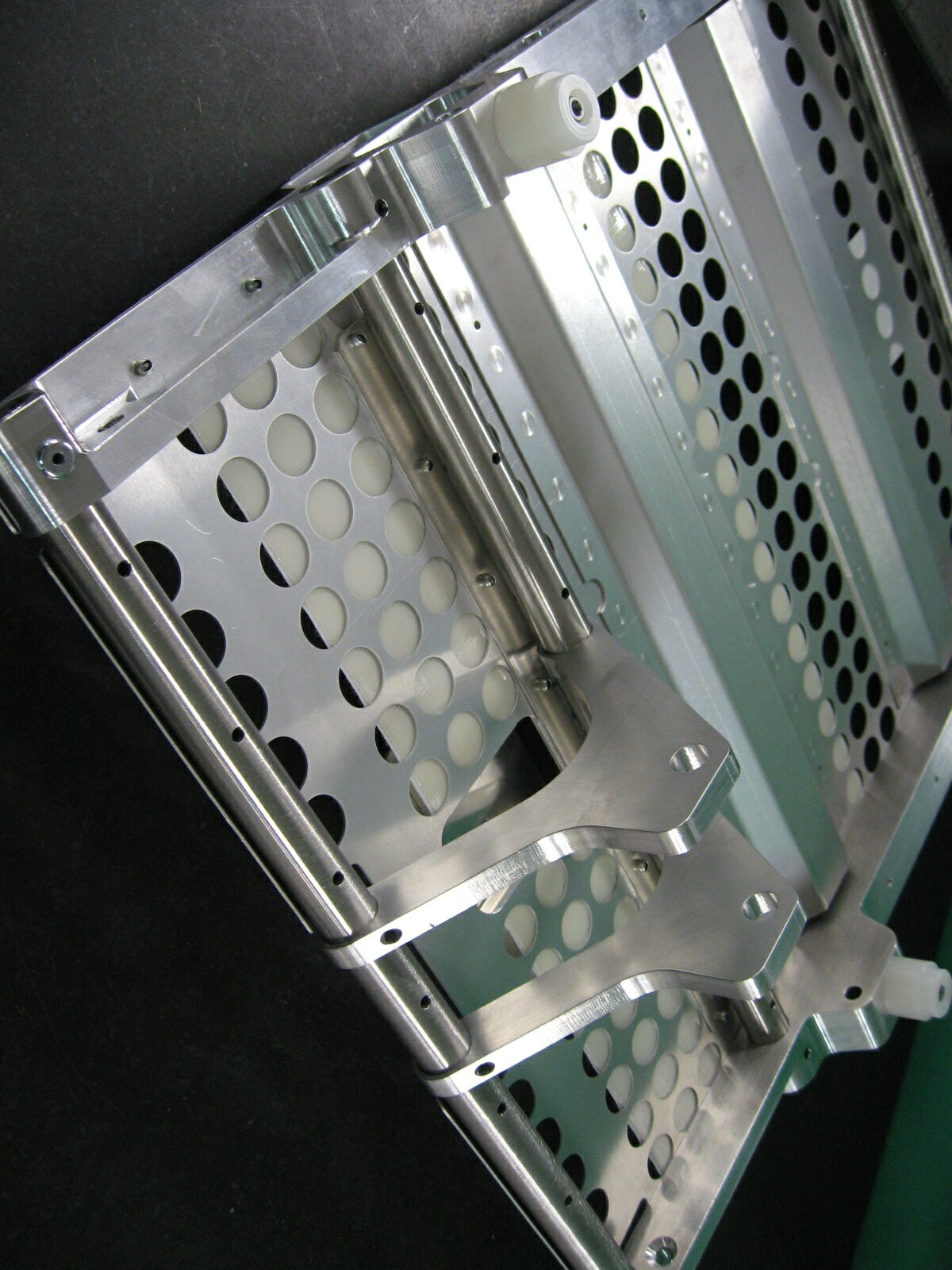
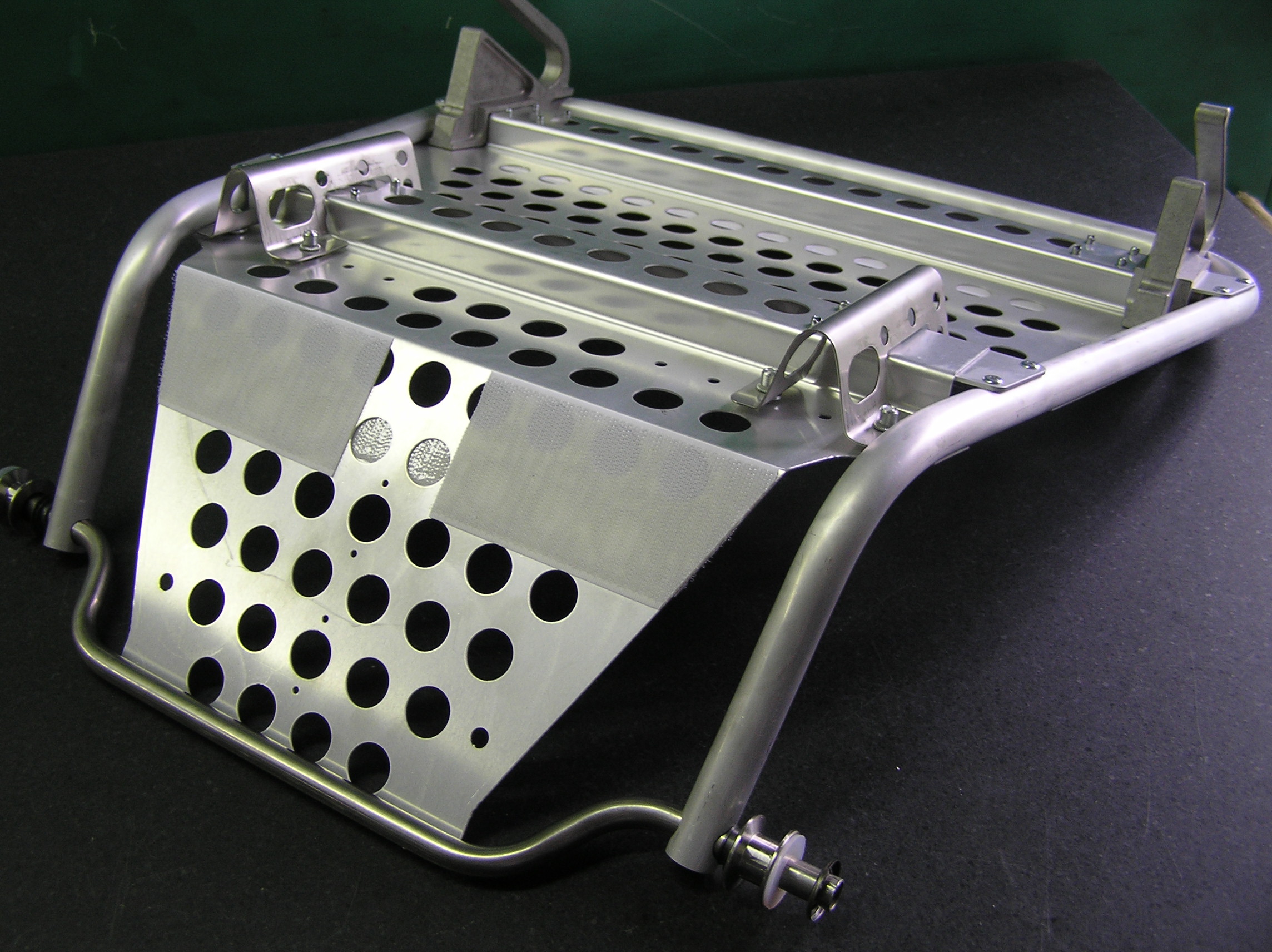
Market trends call for technical solutions
To meet safety and performance requirements, the market is increasingly moving towards pre-coated sheet metal. These coatings are applied by electroplating, chemical treatment or organic coating, depending on specific requirements.
However, this development raises a number of important technical issues. One of these concerns the early melting point of certain components, which can influence the quality of the weld and final assembly…
Another major issue is the mechanical strength of the weld once in service. It is essential to ensure that welds retain their strength over time under a wide range of operating conditions.
Finally, managing the fumes released during welding operations is another challenge. It is essential to evacuate these fumes efficiently to protect operators and guarantee safety on the production site.
The challenges of thin sheet welding
The aim of thin sheet welding is to keep the heat generated to a minimum, to avoid holes and deformation. It therefore requires rigorous control of the energy input and precise handling of equipment, particularly when using an electric arc.
The thermophysical properties and electrical conductivity of materials vary according to their chemical composition. Welding thin sheet metal requires a thorough understanding of these parameters, as well as constantly updated expertise to adapt to technical challenges.
TIG, MIG-MAG, plasma and laser are welding processes just some of the high- performance available. These techniques can be used to assemble materials, such as steel, aluminum or stainless steel. They are also designed to meet precision requirements.
Automation, thanks to industrial robotics, improves these processes by boosting efficiency and reducing margins of error. It also optimizes heat management guaranteeing, aesthetically pleasing and reliable welds.
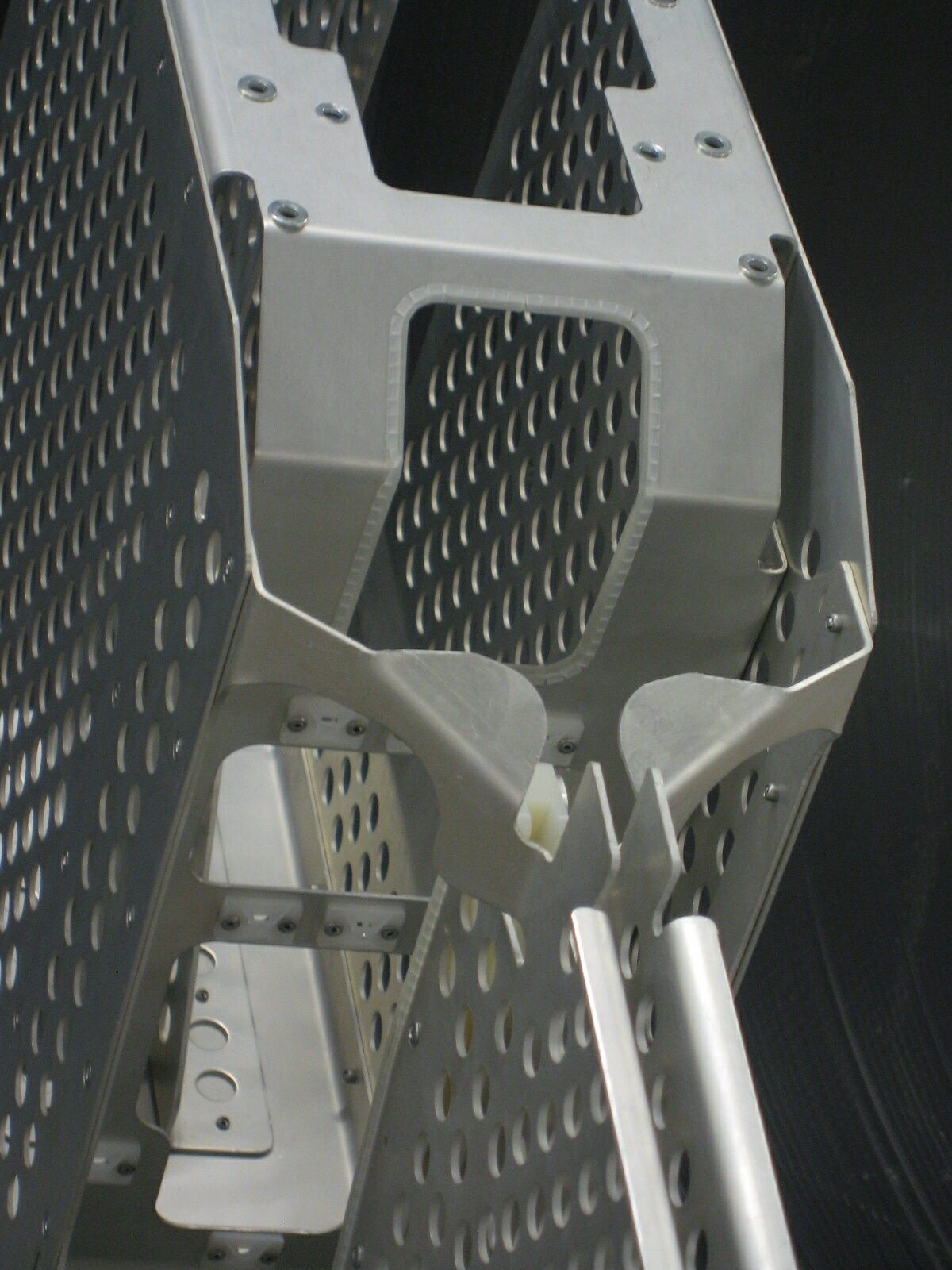
Different thin sheet welding processes
The choice of process for precision sheet metal work depends on several factors: the nature of the components to be assembled, their end use, and whether aesthetics or productivity are a priority.
Choose a professional expert in thin sheet welding
Expertise in thin sheet welding is a necessity for many industries. It has a direct influence on the quality of assemblies and the performance of structures. Material strength and user safety are determined by the precision and reliability of the welds produced.
TRA-C industrie and its subsidiary Jacques Soudure are actively involved in research and development to create state-of-the-art industrial applications. Our approach enables us to meet the stringent requirements of sectors such as aerospace and automotive.
With recognized expertise in precision sheet metal work, Jacques Soudure masters thicknesses from 0.3 to 10 mm, particularly for materials such as aluminum, steel and stainless steel. We draw on unique know-how and state-of-the-art technology, incorporating the latest innovations.
Certified to EN 9100 standard, TRA-C industrie stands out as a recognized supplier to the aerospace industry. Our achievements testify to our commitment to offering high-quality solutions tailored to the needs of the most demanding industries.
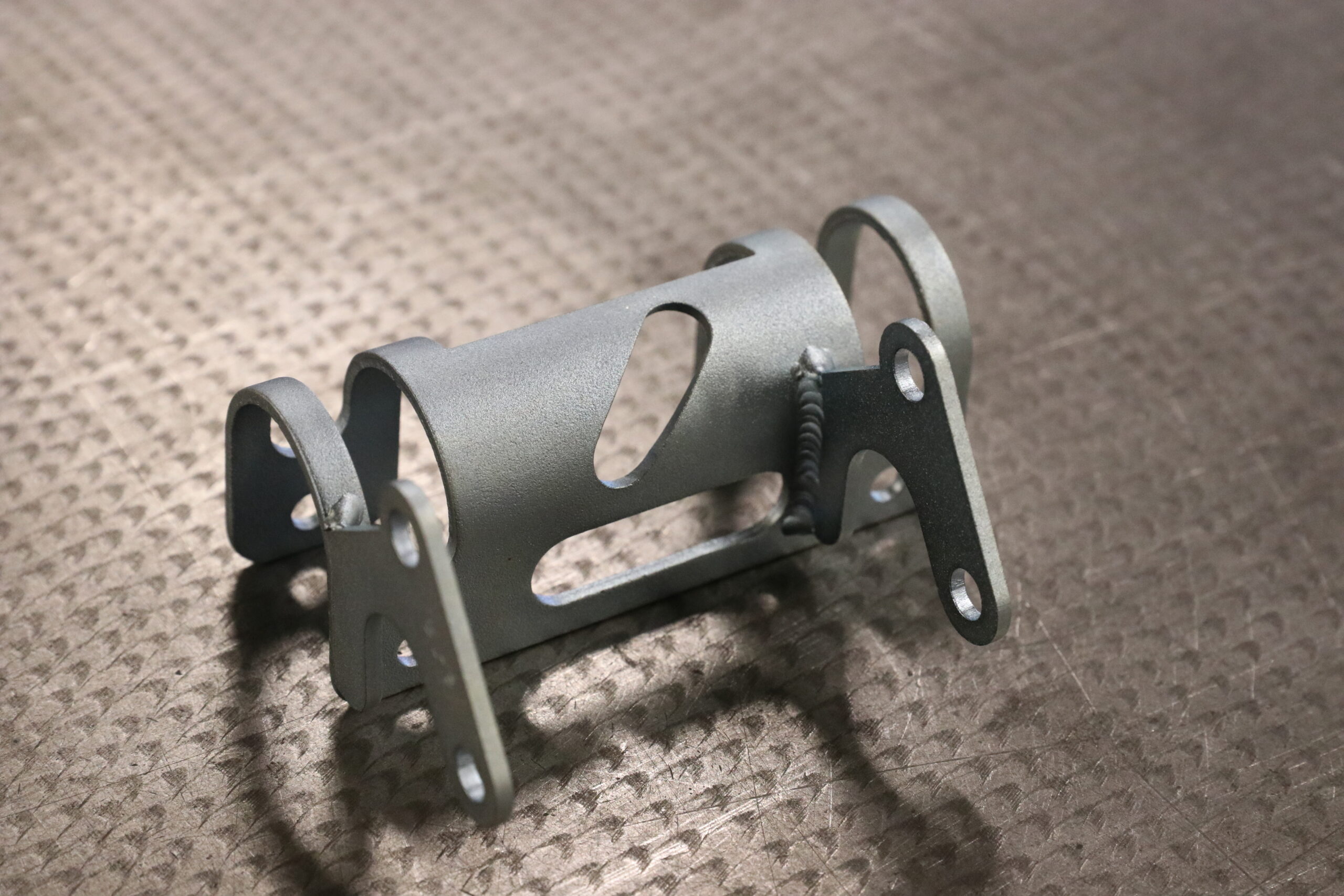