Industry 4.0 represents a new industrial revolution, marked by the integration of digital technologies into production processes. It combines automation, artificial intelligence and the Internet of Things to transform value chains.
This concept goes beyond mere technological innovation, encompassing major organizational changes as well. The main objective is to increase flexibility, efficiency and customization in industrial sectors!
The stakes of Industry 4.0 are considerable: increased competitiveness, optimization of resources and improved quality. However, it also poses challenges such as cybersecurity and upskilling workers.
But what are the challenges facing tomorrow’s industry? How do we define this phenomenon? And what are the impacts of this concept? In this article, TRA-C industrie tells you more about industrial digital transformation…
Digital transformation and industry of the future
On an international scale, French industry has fallen behind in adopting new technologies. To remedy this situation, the Nouvelle France Industrielle (NFI) program, launched in 2013, aims to modernize tools and stem this loss of competitiveness.
Since 2018, with the “Industrie du futur” initiative, a new milestone has been reached. This government plan intensifies digital transformation by integrating more technologies. It impacts not only production systems, but also the business models of industrial SMEs and ETIs.
Advances in miniaturization and digital communication are profoundly transforming businesses. The cloud is revolutionizing design, production and management. It also involves all departments, from operations and human resources to marketing and finance!
With this widespread digitalization, the objectives are clear: to reinforce agility, productivity and efficiency. By relying on continuous improvement, French industry hopes to regain a strategic position in global competition.

What is Industry 4.0 ?
Is Industrie 4.0 different from Industrie of the future, or is it the same vision from different perspectives? It’s a fine line…
The concept of Industry 4.0 emerged in 2011 at the Hannover Fair in Germany, a key event for industrial technology. It refers to a 4th industrial revolution, succeeding steam mechanization, the production lines of the 19th century, and the automation of the 1970s.
Today, thanks to miniaturization and advances in telecommunications, the factory is taking on a new face: that of the Smart Factory. It uses tools such as connected objects, CAD, cobots, additive manufacturing, as well as virtual and augmented reality.
These technologies transform the production chain by integrating cyber-physical systems. The aim? Optimize production in terms of quality, pace and cost, while completely reinventing the industrial model…

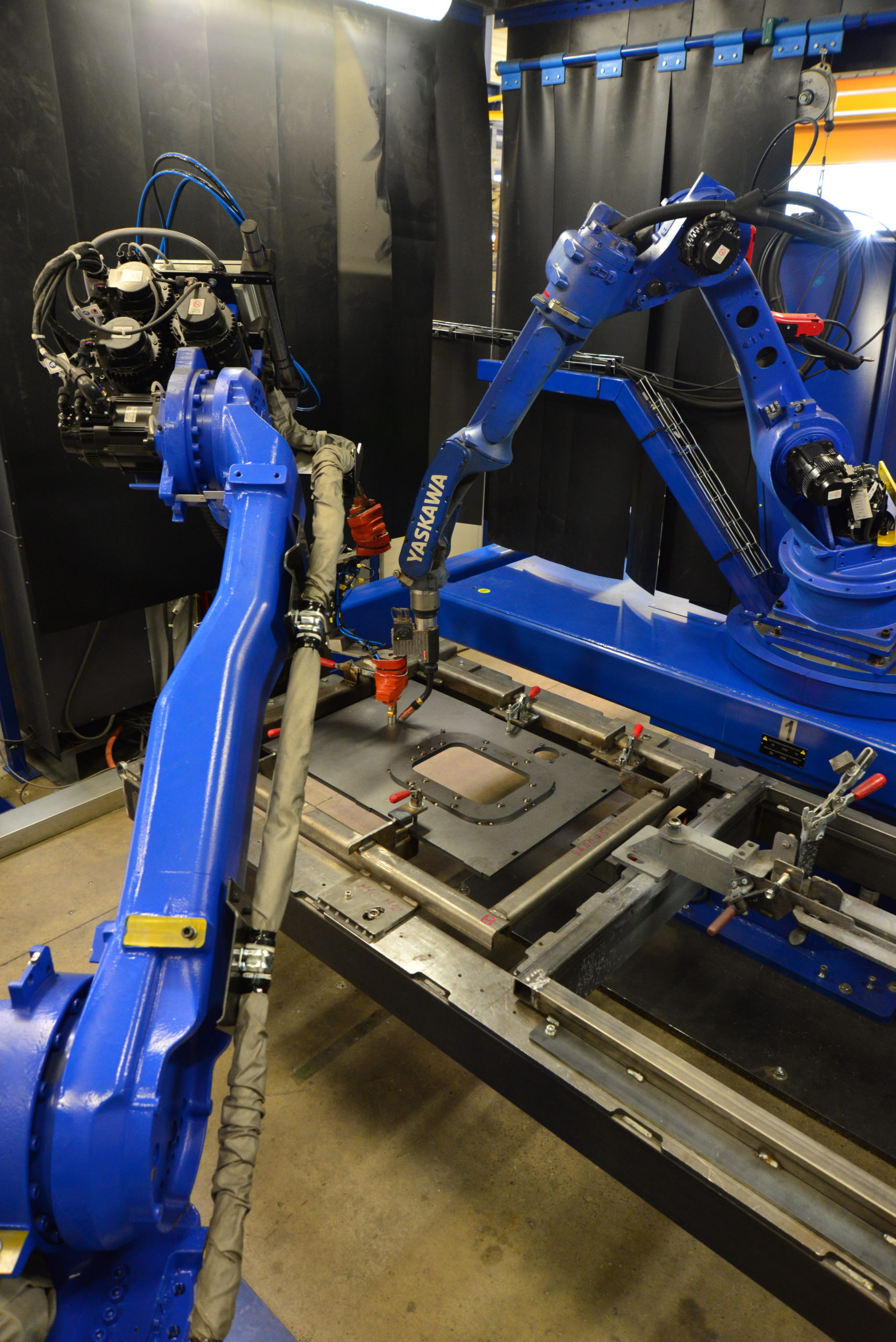
The industry of the future is today
Industry of the future goes beyond Industry 4.0, by profoundly rethinking the organization of the industrial ecosystem. Where Industrie 4.0 focuses on tools, industry of the future integrates a global vision of transformation.
The price of a product is no longer simply dictated by its manufacturing cost. New technologies also open up unprecedented opportunities, enabling fast, flexible production, while offering customized products at mass production costs.
Contrary to what its name might suggest, the industry of the future is not a distant vision, but a current reality. While innovations continue to evolve, companies are already implementing these concepts to transform their day-to-day operations.
This approach connects man, machine and information systems in an optimized value chain. Sensors collect data in real time, AI analyzes it, and human players provide high value-added expertise!
The changes brought about by Industry 4.0
Industry 4.0 represents a profound transformation, affecting the entire industrial model…
The impact of the industry of the future on the welding sector
Industry 4.0 is revolutionizing the welding sector by introducing advanced technologies that improve precision, efficiency and safety. These innovations are thus transforming traditional methods to meet modern production requirements:
- Increased automation: first and foremost, robots and cobots enable faster, more precise welding, reducing human error;
- Data analysis: sensors collect information in real time to optimize processes and anticipate faults;
- Predictive maintenance: intelligent equipment also detects maintenance needs, avoiding unscheduled shutdowns and extending equipment life;
- Process customization: technologies such as CAD and AI adapt parameters to meet specific requirements;
- Risk reduction: automated systems also limit operator exposure to hazardous environments;
- Enhanced traceability: connected technologies record every step of the process to guarantee optimal quality and compliance;
- Energy optimization: finally, intelligent systems adjust parameters to reduce energy consumption during welding operations.

TRA-C industrie, a major player in Industry 4.0
The industry of the future embodies a profound transformation that is reinventing traditional models to meet economic, human and environmental challenges. This revolution is underway, driven by a collective dynamic and innovations that are redefining the future of industry.
As a major player in Industry 4.0, TRA-C industrie plays a central role in this transformation. We are committed to meeting global challenges by providing innovative solutions in energy management, cybersecurity, worker health and know-how transfer!
With its ongoing investment in R&D and its expertise, the company actively contributes to strengthening the competitiveness of French SMEs and ETIs. Our approach, combining technology and collaboration, reflects an ambitious and sustainable vision for the industrial sector.
The TRA-C industrie group is part of the French Lab movement to propel French industry to the forefront of the international scene. Thanks to public support and technological advances, the industry of the future looks bright.