How do I choose my friction stir welding tool?
Because of its complexity, choosing the right friction stir welding tool is not an easy task. Given the challenges in the welding industry, however, its choice is essential to guarantee the quality of your welds…
Friction stir welding (FSW) is an innovative technique developed in the 1990s. Unlike traditional methods that use metal melting, this is a solid-state welding process.
Because of its many advantages and high performance, FSW welding is used for a wide range of applications. Today, this process is at the heart of cutting-edge industries such as aerospace, railway, shipbuilding and e-mobility!
But what is exactly a friction stir welding tool? How does it work? Why and how to choose the right FSW tool? In this article, TRA-C industrie helps you make the right decisions for your welding operations.
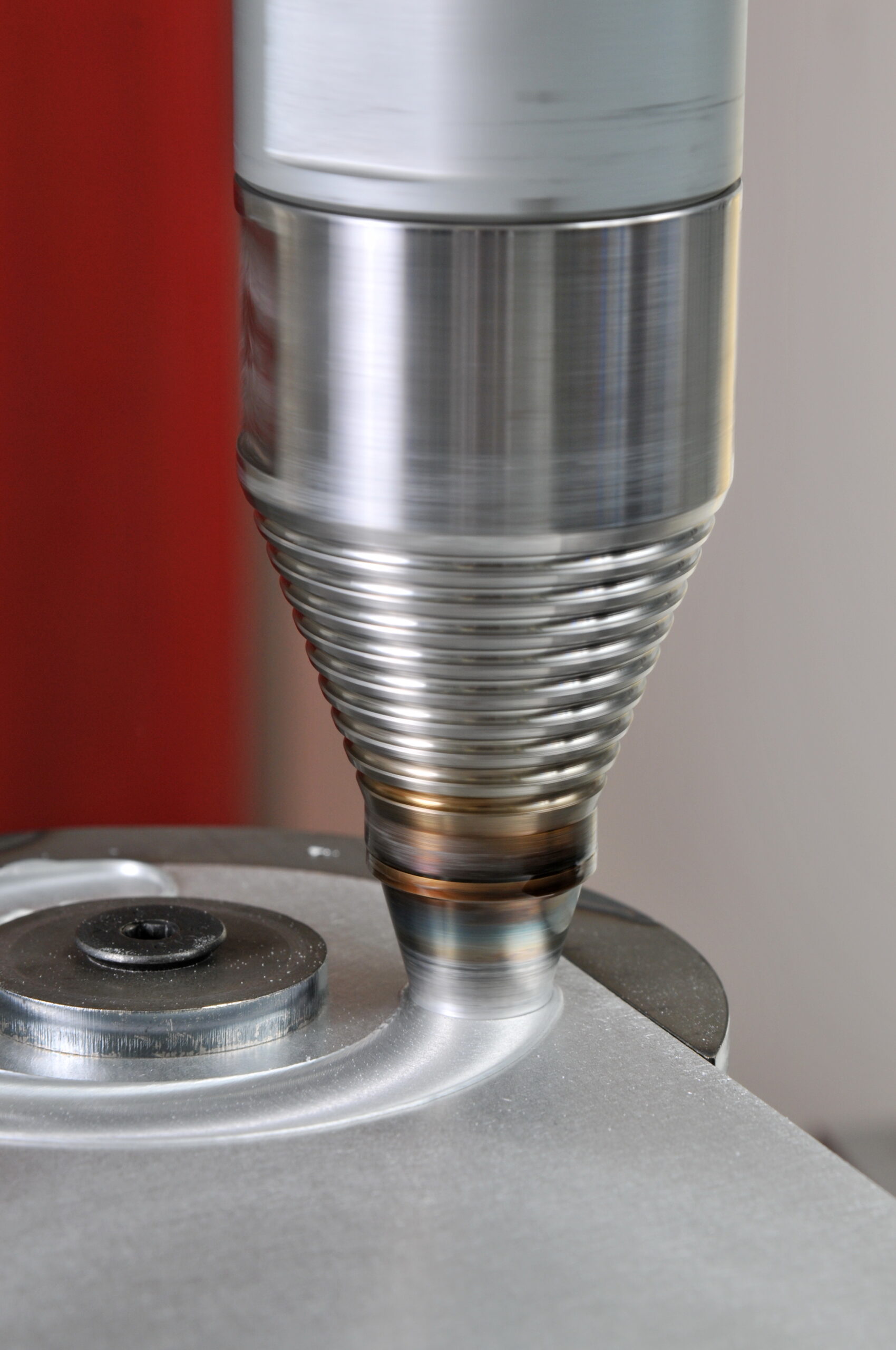
What are the components of a friction stir welding tool?
The friction stir welding tool is one of the key elements for successful FSW applications. Numerous tests and feedback from users have enabled us to determine the best possible geometric configuration.
In all cases, FSW tools are always made up of 2 main elements:
- The shoulder: in permanent contact with the surface of the parts to be welded, it generates a large proportion of the heat by friction. Cylindrical or conical in shape, this part of the tool precedes the pin and exerts a constant pressure, the forging force, to heat and soften the materials. In addition, its spirals draw the material towards the center, preventing it from leaving the weld zone. It results in improved surface finish and weld quality, greater tolerance to weld seam misalignment and reduced burrs.
- The pin: placed at the end of the tool, this threaded point penetrates the softened material and rotates at high speed to mix it by shearing. This is known as mixing. With its grooves and conical shape, it also supplements heating thanks to the plastic deformations generated. It also facilitates the mixing of materials, enabling parts to be welded together.
How does an FSW tool work in practice?
A central part of an FSW machine, the friction stir welding tool operates in 4 key stages during assembly:
- Penetration: after clamping the parts, an essential step to maintain the pieces to be welded, the FSW tool first rotates and is inserted at the interface of the components;
- Pre-heating: this waiting phase then heats the material locally, causing it to enter a pasty state and allowing the tool to heat up;
- Welding: the tool then moves along the weld seam to mix the parts and form a mechanical bond;
- Removing the tool: at the end of the piece, the tool is lifted, leaving an exit hole. As it cools, the material recrystallizes, forming the weld.
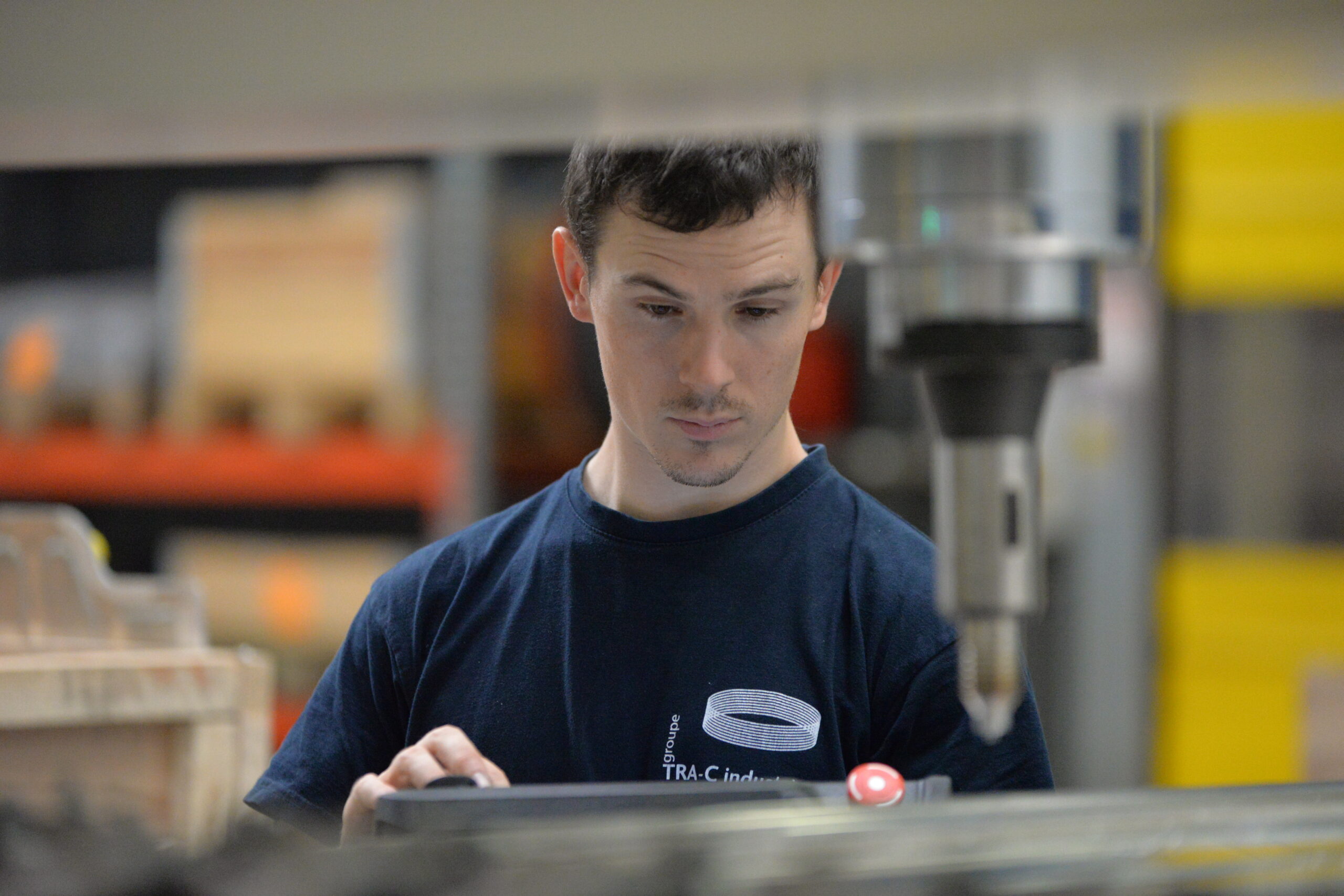
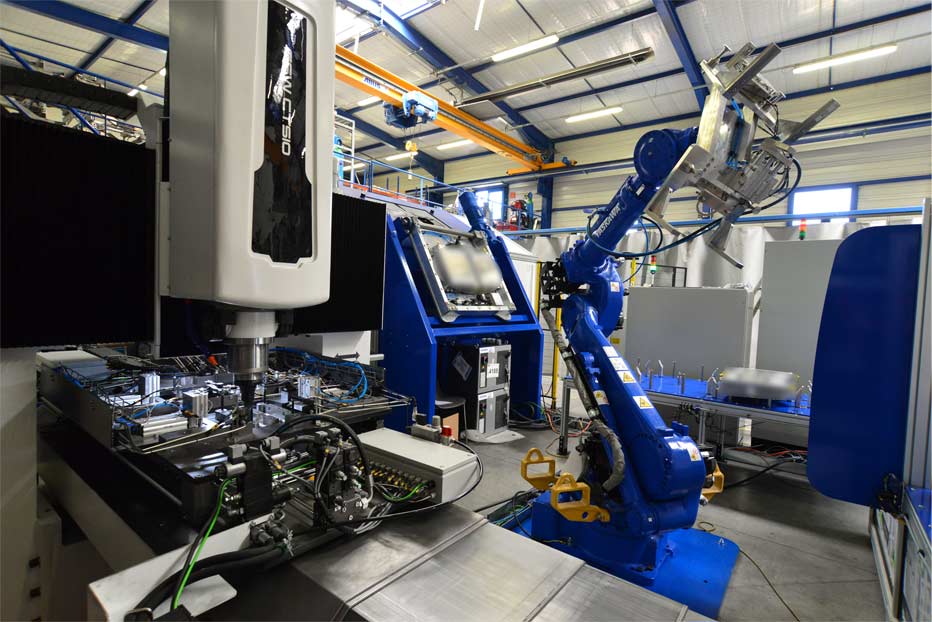
Why choose a quality friction stir welding tool?
Choosing a quality friction stir welding tool is essential because its performance has a direct impact on the finish, strength and integrity of the weld. But also on the durability of the tool:
- Wear resistance: FSW tools are subjected to extreme conditions, with high rotation speeds and high-pressure forces. A quality tool is designed to withstand these stresses, which extends its life span;
- Tool geometry: the shape of the pin and shoulder contribute to the mechanical strength of the weld. Precise geometry therefore reduces weld defects and the need for rework;
- Suitable materials: friction stir welding tools are made of special steels, carbides or composites. Alloys should be chosen according to the performance required;
- Reliability and safety: a quality tool is also tested and certified to ensure that it is reliable and safe to use. It must be able to operate for a long time without any risk of failure during the welding process;
- Weld quality: a good tool produces uniform welds with no major defects and excellent mechanical properties. This reduces the risk of parts being rejected, which could be costly in terms of time and resources.
How do you choose the right FSW tool for your application?
To choose the right friction stir welding tool, a number of parameters need to be taken into account:
- The distance to be welded: first of all, choose a tool that can weld long pieces easily;
- The depth to be welded: also select the pin and shoulder according to the thickness of the parts to be assembled;
- The geometry of the tool: the larger the diameter of the shoulder, the greater the contact surface. This in turn increases the tool’s frictional capacity. Always adapt the dimensions of the shoulder to the thickness of the components;
- The material of the parts: choosing the right alloy for the FSW tool depends on the material to be welded.
In the latter case, choose a tool specifically adapted to the parts:
- The Al/Al tool for welding standard or high-density aluminium (2xxx, 5xxx, 6xxx, 7xxx). Made from an alloy with high elastic limits, it is ideally suited to the aerospace industry;
- The Al/Si tool for welding cast aluminium, widely used in the automotive industry. Made from ceramic, this tool is ideal for this alloy, which contains silicon, a highly abrasive material;
- The Al/Fe tool for welding aluminium and steel composite alloys in the construction sector;
- The Cu tool, finally, for welding copper parts, commonly used in the energy field.

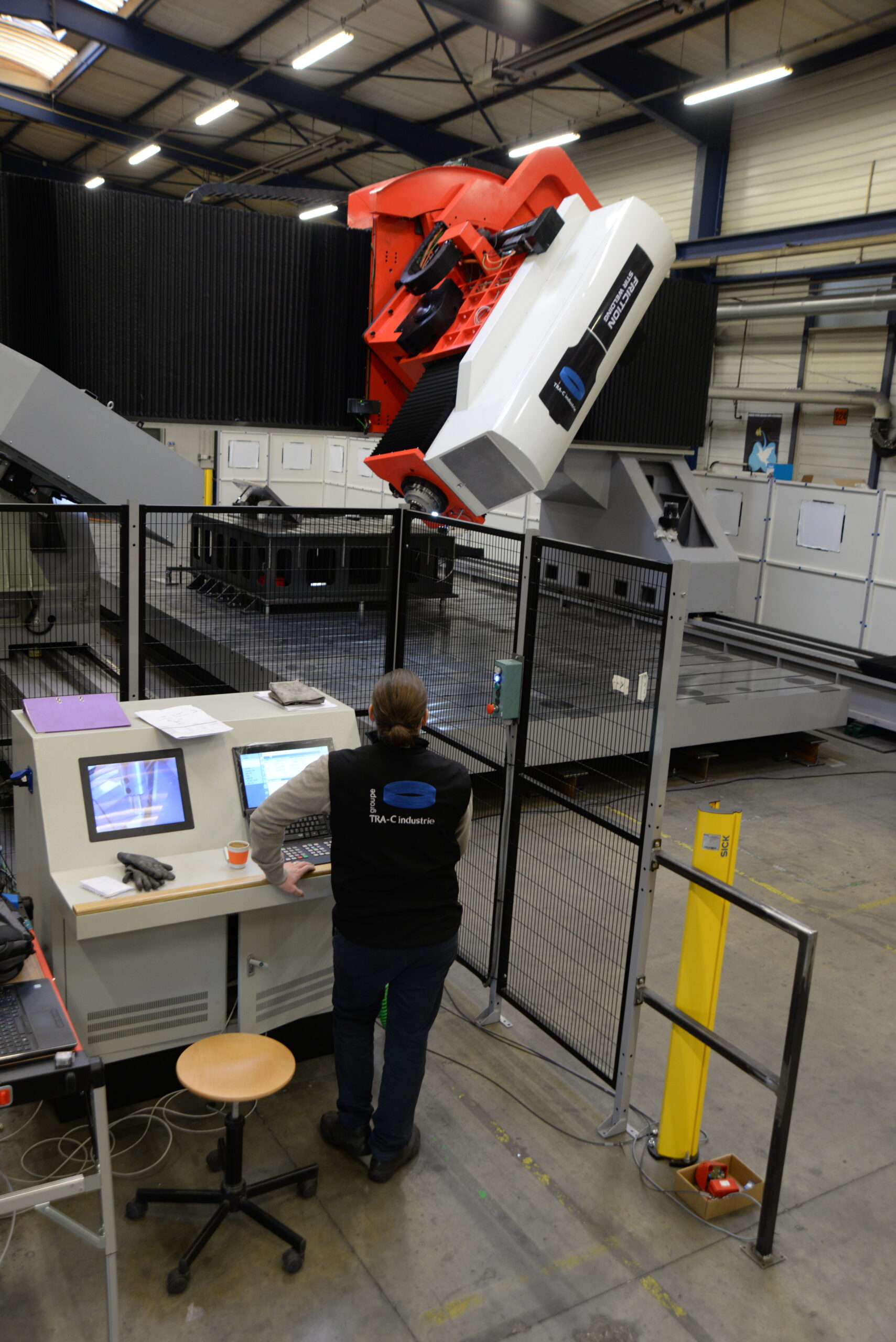
What is the life span of a friction stir welding tool?
The service life of a friction stir welding tool depends on 3 main elements. They need to be taken into account in order to anticipate the replacement of the pin and the shoulder, even before this has an impact on the quality of the joints:
- Abrasive wear: the friction between the tool and the welded material causes fatigue on the spiral of the shoulder, which wears out over the long term;
- Cyclic fatigue: the drag force, as the tool moves along the weld bead, leads to fatigue at the base of the pin and premature failure;
- The materials to be welded: the denser the alloy, the greater the friction, which makes mixing more difficult and wears out the FSW tool.
What are the innovations for FSW tools?
There are 3 major innovations in friction stir welding tools. The first is the absence of an exit hole, characteristic of the FSW process. When the FSW tool comes up at the end of the welding process, it leaves a hole.
This can be problematic for certain demanding applications, such as those in the automotive, aerospace or space industries. The retractable pin tool allows this hole to be filled without the need for subsequent intervention.
Another improvement for FSW tools is real-time temperature measurement. Using a system of sensors that send signals to a software, it is possible to accurately determine the temperature of parts during the welding process.
This advance enables manufacturers to optimize welding parameters (feed speed, rotation speed and pressure).
The final innovation is the stationary shoulder FSW (SSFSW) process. Unlike the conventional FSW tool, which has 2 functional parts, this configuration comprises a rotating pin and a stationary shoulder.
The result is a flat, smooth welding surface and greater robustness, particularly on complex 3D paths. This reduces the amount of re-machining required. SSFSW tools are nevertheless more complex to design and manufacture.
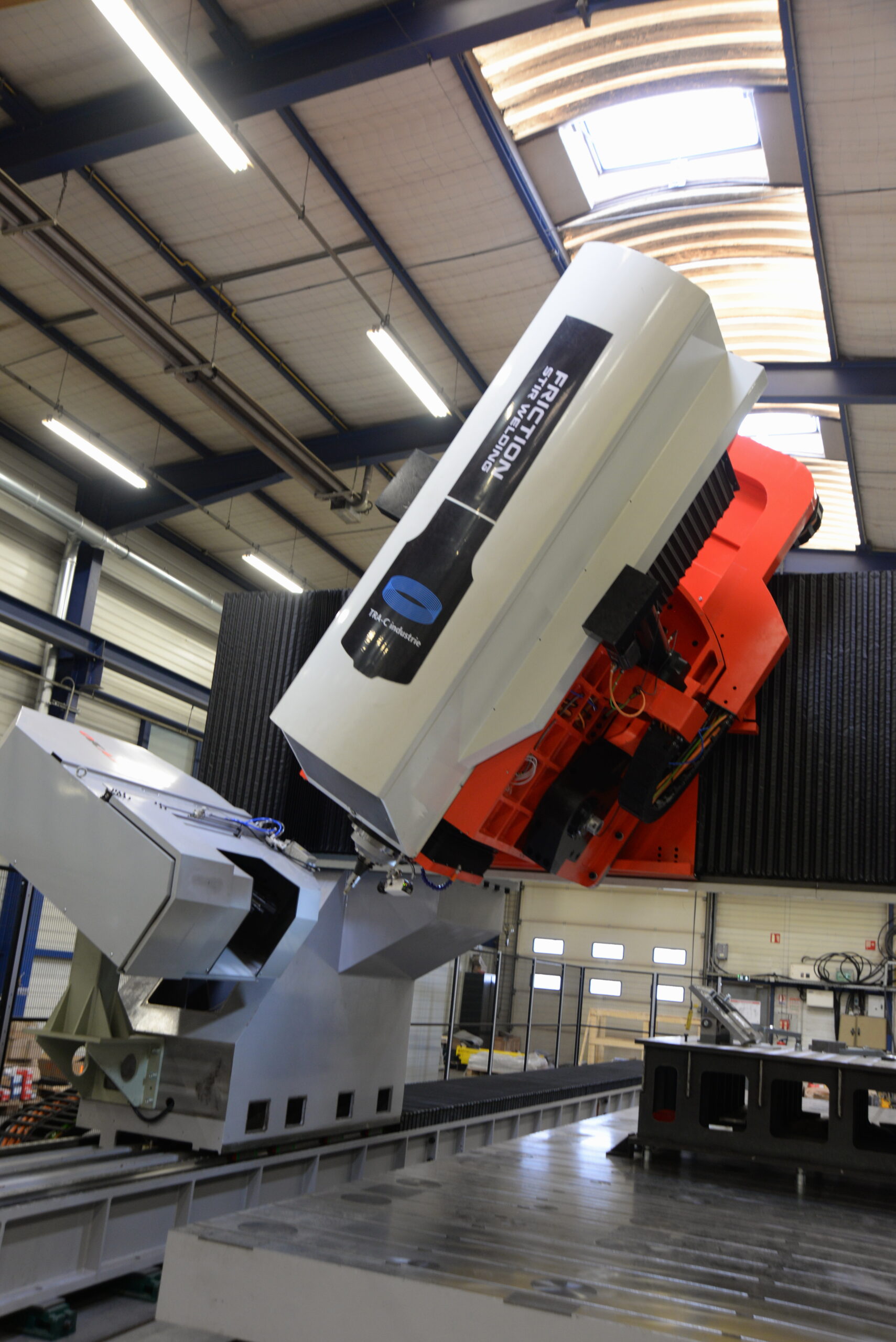
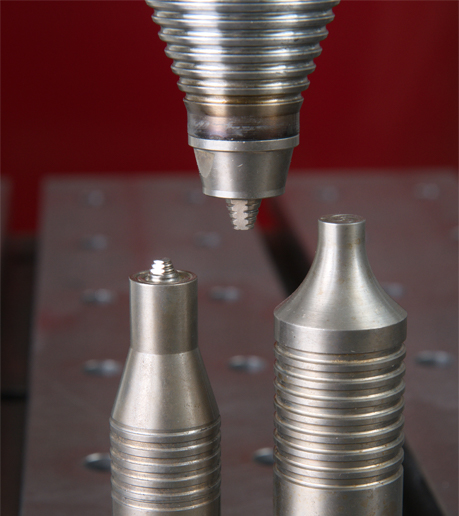
TRA-C industrie helps you choose your friction stir welding tool
As the European leader in the friction stir welding market, TRA-C industrie supports companies and manufacturers in the study, design, manufacture, installation and maintenance of their FSW tools. We are also here to train your technicians and welders in its use, in complete autonomy…
Certified to EN 9100 and EN 9001 standards, our experience and know-how enable us to operate in cutting-edge sectors such as aerospace, shipbuilding, defense, railway, automotive and e-mobility. And for major companies such as Dassault Aviation, Safran, Thalès and Stelia Aerospace.
We offer you high-performance quality tools. moreover, we test all our FSW tools and ensure their traceability thanks to a unique identifier. Finally, we carry out rigorous checks to ensure that they comply with European standards!
Do you want to find out more about FSW welding? Would you like advice on choosing your friction stir welding tool? We answer all your questions and guide you towards the best options based on your needs: