FSW welds: how to extend the service life of assemblies?
FSW welds (Friction Stir Welding) represent a major advance in metal joining. Used in a wide range of sectors and demanding industries, they produce high-quality joints without melting the materials…
Friction stir welding offers superior mechanical strength to traditional methods, while limiting the usual deformations and defects. However, as with any joining process, prolonging weld life is essential.
Many factors influence this longevity, such as the choice of materials, welding parameters and the quality of in-process inspection. Precise control of these factors ensures the reliability and durability of the assemblies!
But what are the challenges involved in producing quality assemblies? What factors influence the durability of welds? And how can they be made to last longer? In this article, TRA-C industrie tells you more about friction stir welding.
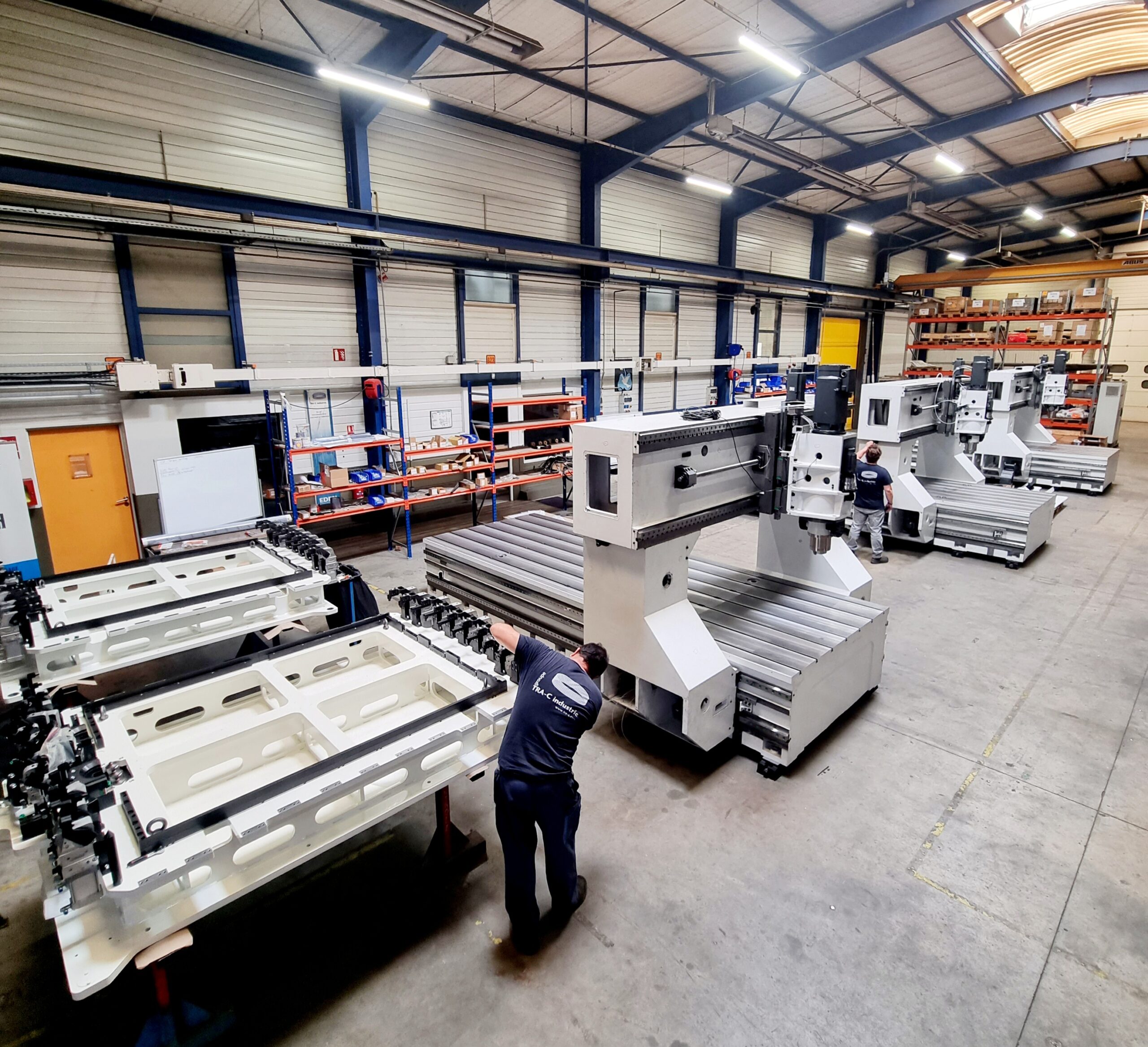
The importance of durability for FSW welds
The durability of FSW welds is a key factor in guaranteeing the performance and safety of structures in various industrial sectors. Among the challenges of achieving quality assemblies, there are:
- Reduced maintenance costs: first and foremost, durable welds require fewer repairs. This reduces long-term maintenance costs and improves operational efficiency;
- Safety of critical structures: increased durability also minimizes the risk of failure. It therefore guarantees the safety of infrastructures exposed to high stresses, such as aircraft or bridges;
- Product lifespan: durable FSW assemblies also enable equipment and structures to remain functional for longer. They therefore improve their profitability and environmental impact;
- Resistance to extreme environments: a durable weld is finally more resistant to difficult conditions, such as thermal variations or corrosion. It extends the reliability of a welded part in hostile environments.
The advantages of friction stir welding for assemblies
First and foremost, friction stir welding offers superior weld quality, with strong, homogeneous welded joints. It eliminates the problems of porosity and cracks often encountered with fusion welding processes, and guarantees greater mechanical strength…
Another major advantage of FSW is the absence of material melting. This limits thermal deformation and improves the dimensional accuracy of assemblies. This is particularly useful for high-tolerance applications such as aerospace.
This solid-state welding process is also environmentally friendly, as it requires no shielding gas, filler metal or other consumables. What’s more, the energy used for the process is lower than for traditional welding techniques, reducing its environmental impact!
Finally, this method is ideal for joining light alloys such as aluminum or magnesium. It produces high-quality welds with enhanced corrosion resistance. FSW is therefore suitable for the automotive and marine sectors.

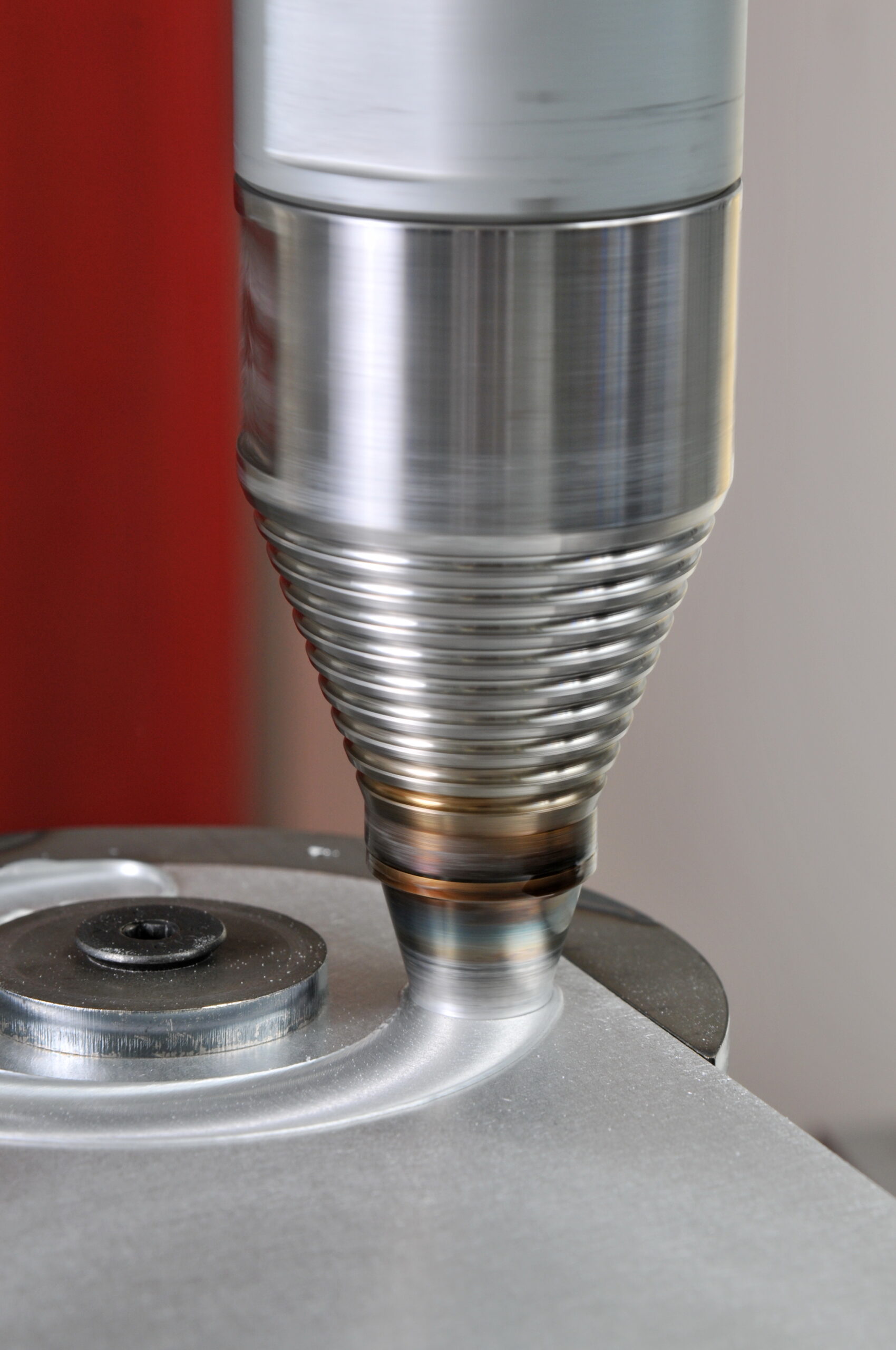
What factors influence the service life of FSW welds?
The durability of FSW welds depends on a number of key variables, from the characteristics of the materials to the quality of the welding process. Here are the main factors to consider:
- Materials used and compatibility: the nature of the metals to be joined plays a key role in the strength of the weld. Incompatible materials can lead to premature cracking or deformation;
- Speed of rotation: optimum tool rotation promotes homogeneous mixing of materials. This reduces the risk of defects and increases the service life of the welded assembly;
- Temperature and thermal control: the right temperature during the welding process prevents overheating and degradation of material properties. It also helps extend weld life;
- Tool feed: the feed speed of the rotating tool also has a direct influence on the quality of the weld joint. A feed speed that is too fast may result in incomplete welds, while a slow one may cause overheating;
- Applied pressure: insufficient pressure can create gaps and defects, while excessive friction can damage parts to be assembled or cause deformation;
- Defects and impurities in the weld: finally, the presence of impurities or defects, such as pores or inclusions, can weaken the weld and accelerate wear under stress.
How to improve the durability of FSW assemblies?
To improve the durability of FSW welds, it is essential to optimize welding parameters. Rotation speed, tool feed and pressure must be adjusted to suit the materials used, to guarantee a homogeneous, resistant weld!
Rigorous temperature control during the welding process is also essential. By avoiding overheating, the risk of material embrittlement is minimize. It helps extend the life of welded joints.
Surface preparation prior to welding is another key factor. Proper cleaning and polishing of metal parts removes impurities, ensuring better fusion of materials and reducing the risk of defects…
Finally, post-weld inspection using non-destructive techniques can detect any defects invisible to the naked eye. These checks guarantee weld quality and prevent long-term failure.


Inspection and quality control of FSW welds
Inspection and control of quality for FSW welds are essential to ensure the reliability of assemblies. They enable the presence of defects, such as porosities or internal cracks, to be detected!
Non-destructive testing (NDT) techniques are commonly used to assess the quality of welds without damaging them. Among them, ultrasonic inspection can detect internal anomalies invisible to the naked eye.
Industrial radiography is another effective method for examining the weld in depth. It can identify internal defects such as foreign material inclusions or cavities…
Regular quality control throughout the manufacturing process helps to detect problems as soon as they appear. It enables defects to be corrected quickly and ensures optimum service life for FSW assemblies.
Care and maintenance of welded structures
The maintenance of welded structures requires active monitoring of the environment in which they operate. Factors such as humidity, temperature and chemicals can affect the durability of FSW welds.
The application of protective coatings helps prevent weld corrosion. These treatments, such as anticorrosion paints or polymer coatings, create a protective barrier against aggressive elements that could weaken assemblies…
In the case of minor localized damage, weld overlay can also be used. This approach makes it possible to reinforce the affected areas without having to dismantle the entire structure. This minimizes operational interruptions.
Lastly, monitoring stresses over time helps to detect any overloading. Adjusting operating conditions or redistributing loads can reduce mechanical stress on welds and extend the durability of assemblies!

Guarantee the quality of FSW welds with an expert
Calling on an expert in friction stir welding (FSW) ensures high-quality assemblies. Experience and mastery of welding parameters are essential for durable, defect-free and strong welds.
TRA-C industrie is a recognized leader in FSW welds. Thanks to our technical expertise and state-of-the-art equipment, we guarantee high-precision assembly of parts, adapted to the requirements of the most critical sectors such as aerospace and automotive!
We control the entire process, from the design of materials to the validation of final welds. We design customized solutions, optimize the performance of welded structures, and comply with the most stringent industrial standards.
When you entrust your projects to TRA-C industrie, you benefit from complete assistance, from design to production. Our expertise ensures high performance, reliable welds, with controlled costs and optimum safety for your structures…