FSW in shipbuilding: challenges and benefits
FSW in shipbuilding marks a technological revolution in material joining. Thanks to the friction stir welding process, shipyards are able to meet the industry’s performance and safety requirements!
Long faced with the limitations of traditional welding methods, shipbuilding now benefits from an alternative to eliminate common defects. FSW guarantees high-quality welds, free from porosity and deformation, essential for demanding marine environments.
The implementation of FSW (friction stir welding) requires specific equipment and appropriate operator training. It is prompting industry players to rethink their processes and invest in new skills…
But what is at stake in the naval sector? And what are the interests of FSW in the naval industry? And what are the challenges of this technology? In this article, TRA-C industrie tells you more about FSW applications and innovations for shipyards.
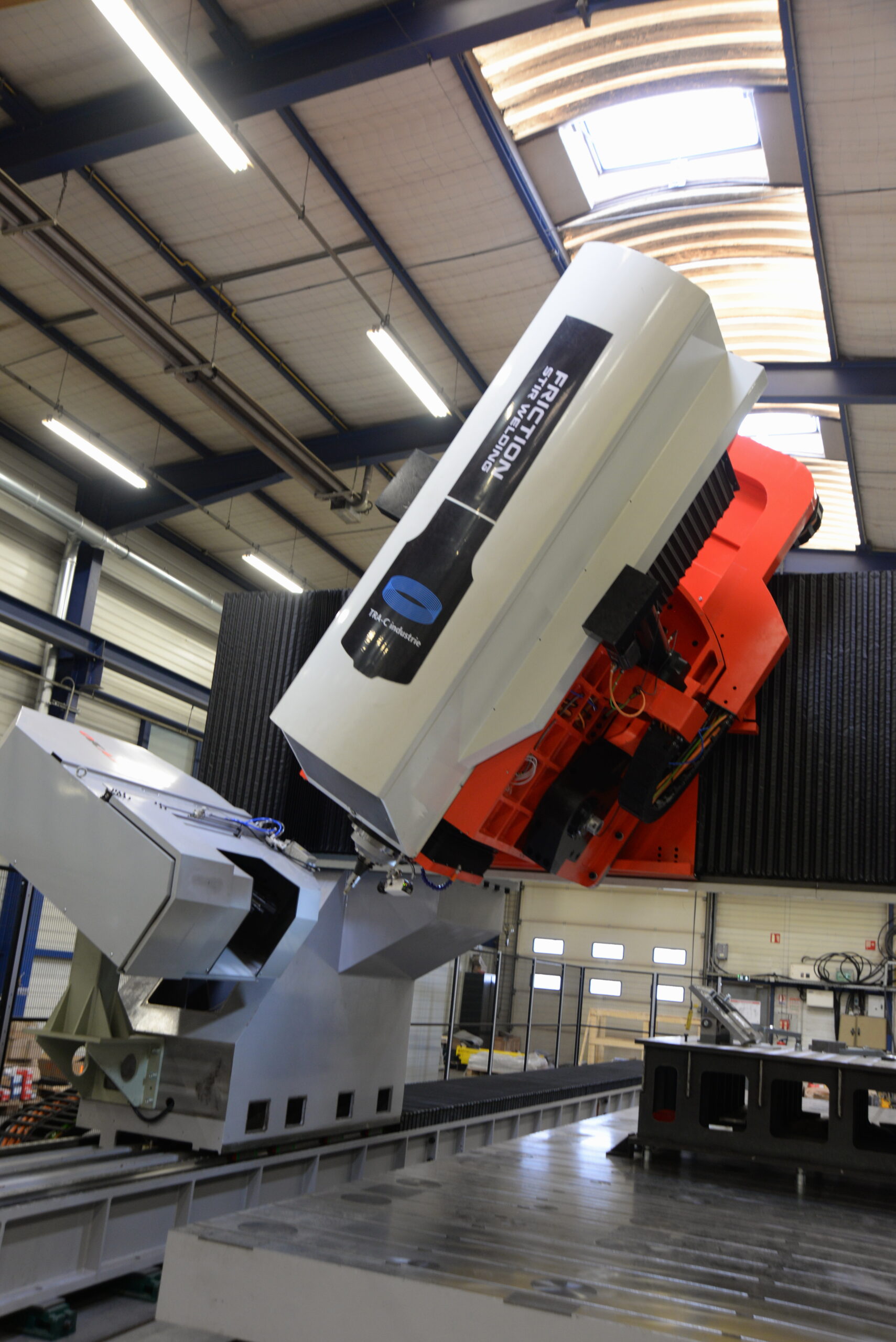
What are the challenges facing the naval sector in terms of welding?
In the shipbuilding industry, the quality of welds is essential to guarantee the safety, durability and efficiency of vessels. Shipyards face complex challenges in meeting market standards and expectations:
- Resistance to the marine environment: welds must first withstand extreme conditions such as corrosion, high pressure and constant temperature variations;
- Structural reliability: faulty welds can also compromise the integrity of ships, endangering passengers and cargo;
- Reduced maintenance costs: durable assemblies mean fewer frequent repairs. This is essential for optimizing operating budgets;
- Compliance with standards and regulations: international standards also require flawless welds to ensure that ships comply with safety requirements;
- Adapting to new materials: last but not least, the growing use of light alloys and composites for ship sheet metal requires appropriate and reliable assembly techniques.
Interests of FSW in shipbuilding
By combining performance and reliability, FSW in shipbuilding meets specific industry needs. This technology offers a host of advantages for meeting the sector’s technical and economic challenges:
- Unrivalled weld quality. Thanks to porosity- and crack-free joints, FSW first and foremost guarantees long-lasting strength. This is particularly important in marine environments;
- Better adaptation to modern materials. In addition, light alloys such as aluminum can be assembled, helping to lighten ships and improve their energy efficiency;
- Significant reduction of deformations. The absence of melting also limits thermal stress and distortion, simplifying the construction of complex structures;
- Compatibility with large dimensions. This process is particularly suitable for welding long sections, such as hull panels, without compromising joint homogeneity;
- A more economical and ecological process. FSW also consumes less energy and produces little waste. It thus offers a sustainable alternative to conventional methods;
- Reduced welding noise and vibration. FSW is a silent process compared to traditional techniques, improving working conditions in shipyards;
- Enhanced reliability for ship safety. Last but not least, this technology minimizes human error. It guarantees more homogeneous welds, in line with international standards.
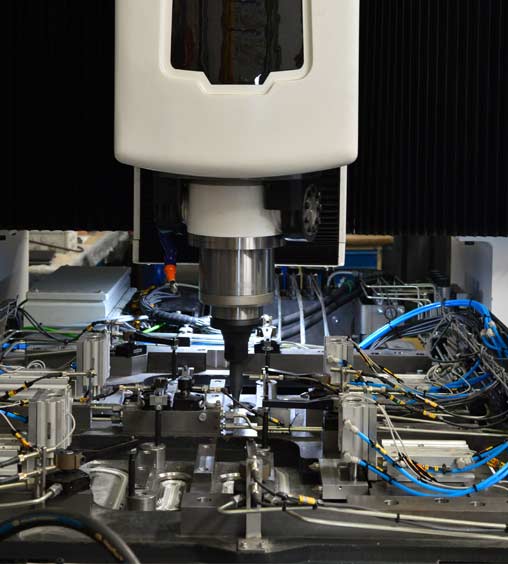
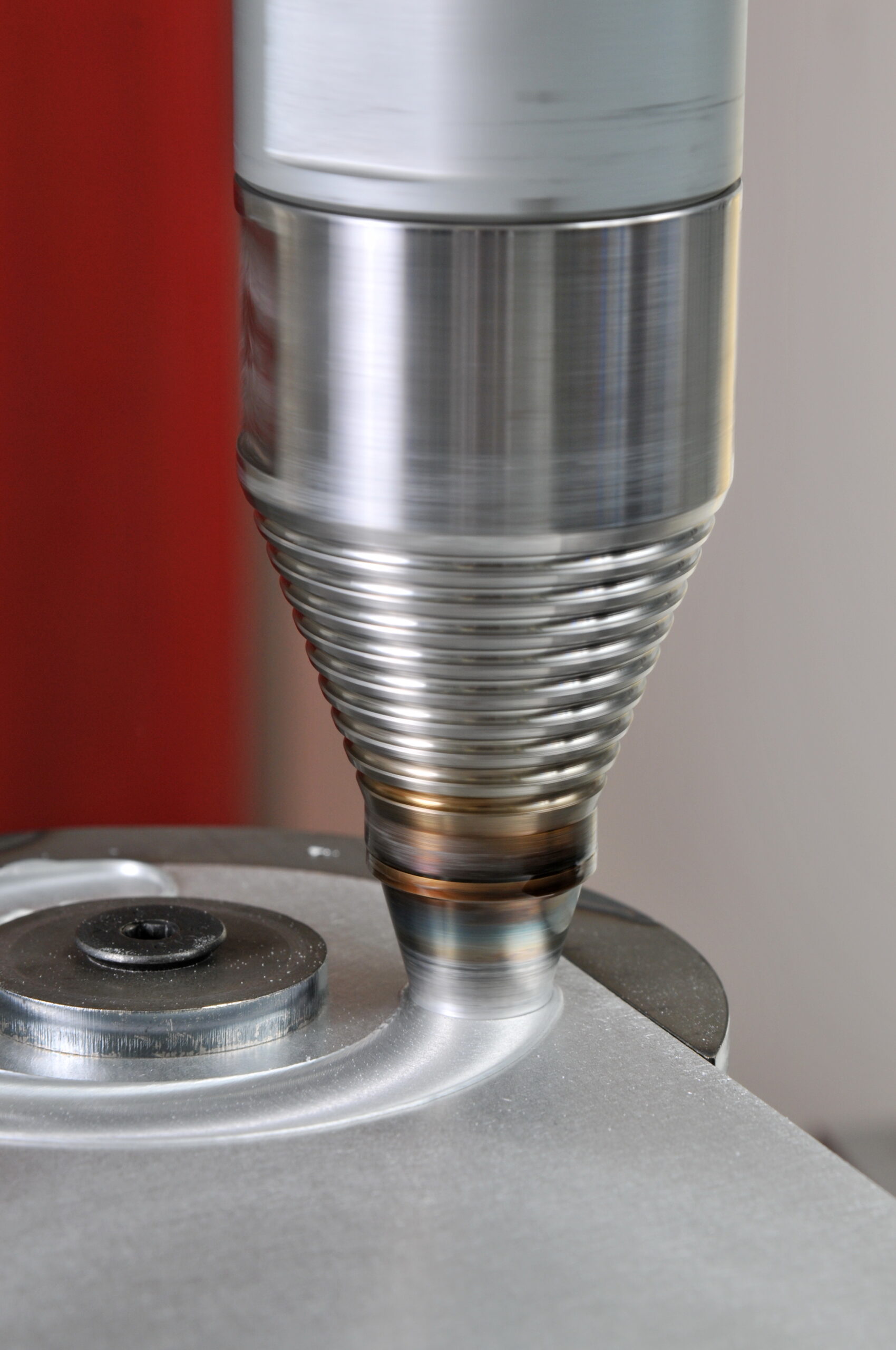
What are the challenges of friction stir welding for shipyards?
The adoption of FSW in shipbuilding requires significant investment in specialized equipment. Unlike conventional techniques, FSW requires powerful machines capable of withstanding high stresses, which may slow down its widespread use.
Training welders is another major challenge. This assembly process requires specific technical skills and precise control of parameters. As a result, companies sometimes have to set up training programs.
Adaptability to large structures is also a major constraint. In the construction of large vessels, friction stir welding has to be integrated into complex environments, which can lengthen design times.
Finally, the high initial costs of FSW may deter some shipyards, particularly smaller ones. However, these challenges could be overcome thanks to the long-term savings and increased durability of welds made with this method.
Concrete applications of FSW in shipbuilding
The use of FSW in shipbuilding is gradually gaining ground in various aspects of the sector. It offers innovative solutions for reliable, high-performance assemblies. Here are a few examples of practical applications of this technology:
- Assembling aluminum panels. FSW was first used to weld lightweight hulls and superstructures, reducing the overall weight of ships and improving their energy efficiency;
- Manufacture of cryogenic tanks. This technique guarantees the tightness and strength of tanks used to transport liquefied gases, which are essential for LNG carriers;
- Bridge and bulkhead construction. It also provides strong, precise welds for bridges and bulkheads, increasing the safety and rigidity of structures;
- Repairing damaged parts. FSW is also used to repair structural components, offering an effective and durable alternative to traditional welding methods;
- Manufacture of specific components. Last but not least, parts such as propellers and mooring systems can be precision-welded, guaranteeing optimum performance.
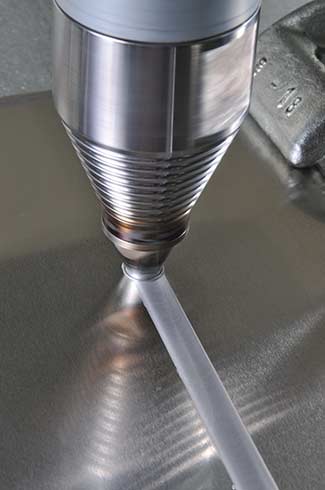
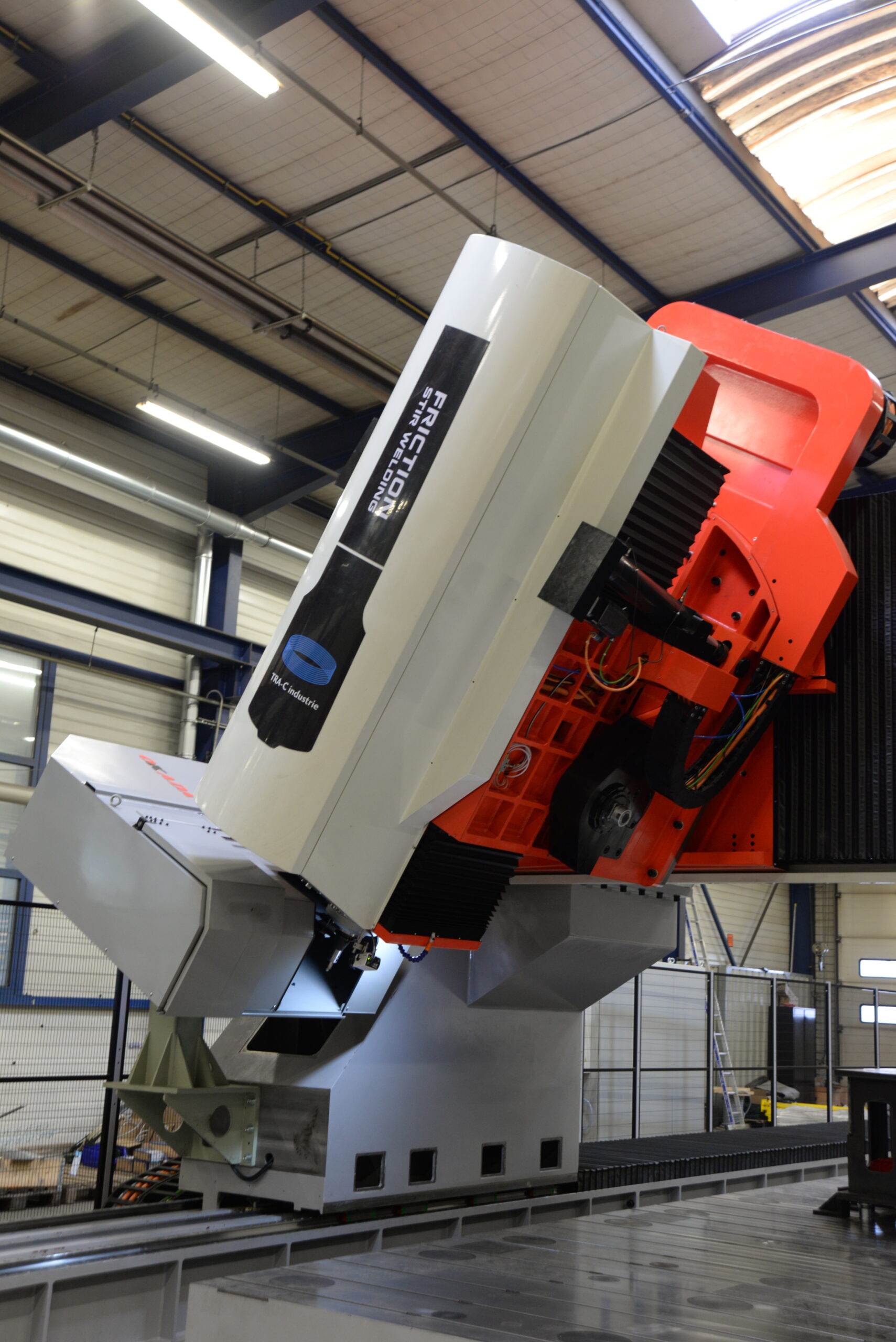
FSW innovations and developments in the naval sector
Recent innovations of FSW in shipbuilding have focused on process automation. Specialized robots can now weld complex structures with increased precision. This reduces human error and boosts shipyard productivity.
Advances in materials also enhance the efficiency of the process. High-strength alloy tools extend tool life, making FSW more competitive with other welding techniques, even for hard, tough metals…
Sophisticated systems can now monitor welding parameters in real time, guaranteeing consistent quality and early detection of anomalies. These automated monitoring tools contribute to the precision of welds and the safety of operations.
Finally, research is being carried out to extend FSW to composite materials, which are increasingly used in shipbuilding. These developments promise to push back current limits, offering solutions adapted to the evolving needs of the industry!
TRA-C industrie, specialist in FSW in shipbuilding
TRA-C industrie is a key player in the integration of FSW in shipbuilding. Thanks to its expertise and state-of-the-art equipment, the company supports shipyards in producing reliable and innovative welds!
We offer tailor-made solutions for the assembly of complex hulls, superstructures and critical components. Our know-how guarantees high-quality results, meeting the most stringent international standards for safety and durability.
Our company also invests in research and development to push back the limits of FSW. Thanks to our collaboration with laboratories and universities, we contribute to the evolution of techniques and the development of new tools adapted to modern materials.
In addition to our welding expertise, we offer training programs for operators. In this way, we pass on our expertise to shipyards, enabling them to adopt FSW effectively and remain competitive in an ever-changing industry.