Friction stir welding: major advances
As a revolutionary welding method, Friction Stir Welding (FSW) is a more efficient technique than traditional welding methods. It is characterised by a heating process that produces high-quality welds with fewer defects.
FSW’s major innovation lies in its ability to assemble heterogeneous parts that are difficult to weld. The method can therefore be used for a wide range of materials, including aluminium and light alloys.
But what is this innovative welding method all about? In this article, TRA-C industrie takes a look at the principle, technological advances, challenges, prospects as well as the economic and environmental impact of friction stir welding…
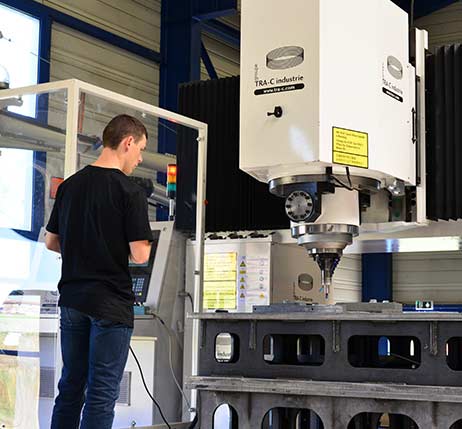
Principle of friction stir welding
Discovered in 1991, friction stir welding is a solid-state welding process. It uses heat and pressure to create a weld without the need to add additional metal.
A rotating welding tool is then inserted into the metal. The rotation at high speed generates frictional heat, which softens the metal without melting it. The metal is then kneaded by the tool to form the weld. This process is also known as cold welding.
The FSW welding tool consists of two main parts:
The heat generated, with no melting, will soften the metal around the pin while the shoulder of the tool maintains the heat and kneads the ‘plasticised’ metal. Finally, the tool is moved along the joint to form a solid, uniform weld, then removed at the end of the process.
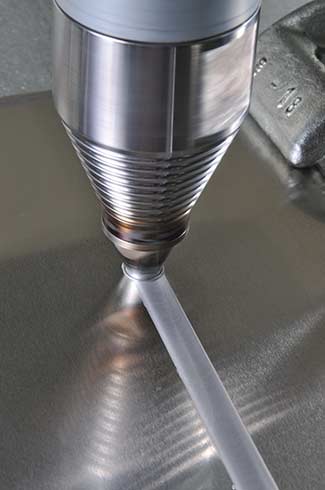
Technological advances in FSW
Force control
The FSW welding process has undergone numerous technological advances since its appearance in the welding industry. In addition to increasingly high-performance tools capable of withstanding higher temperatures and pressures, the major innovation is force control.
Pistons are used to exert constant pressure on the parts. The pressure is then automatically adjusted according to the condition of the parts. In the machining industry, on the other hand, only the position of the tool remains constant, but the pressure varies.
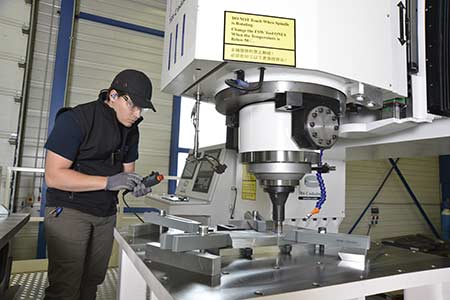
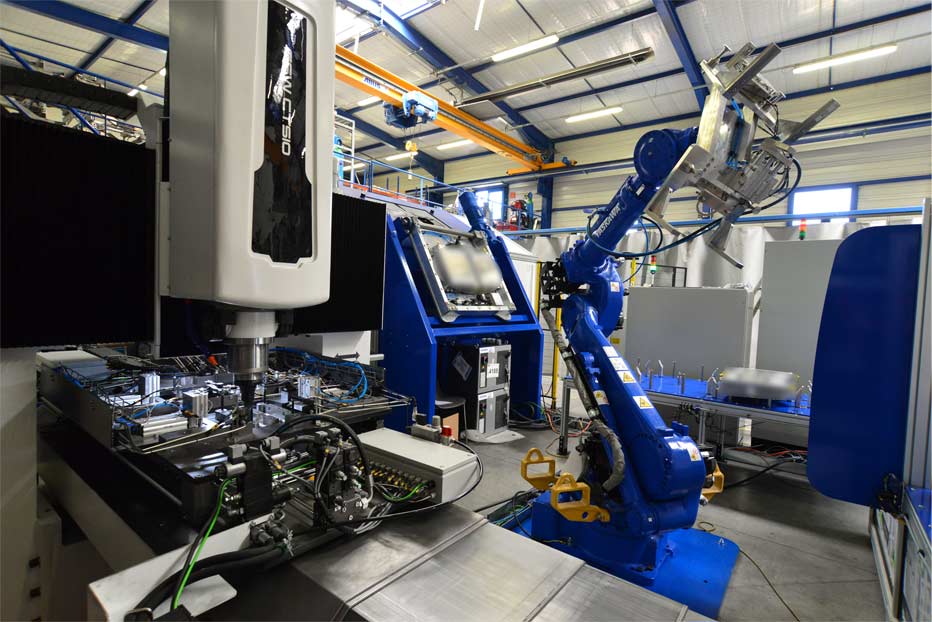
Welding thick alloys
The friction stir welding process can now be used to assemble cast aluminium alloys or alloys with high thickness (up to 50 mm). This was previously difficult to achieve with conventional welding methods.
Thanks to FSW, welds are extremely strong and homogeneous. This is essential in sectors where reliability is paramount, such as aeronautics, rail and space.
This method also preserves the integrity of aluminium alloys. It limits the deformation and defects typical of traditional welding techniques. This is essential to preserve the mechanical properties of the assembled parts.
HMI interface
HMI stands for Human Machine Interface. Technically, it consists of a control panel that connects man to a machine, device or system. However, the term is mainly used in the industrial sector.
In the field of friction stir welding, the HMI interface has made it possible to optimise industrial processes by digitising and centralising data. As a result, operators can easily monitor and track production progress in real time, and stop or speed it up it if necessary.
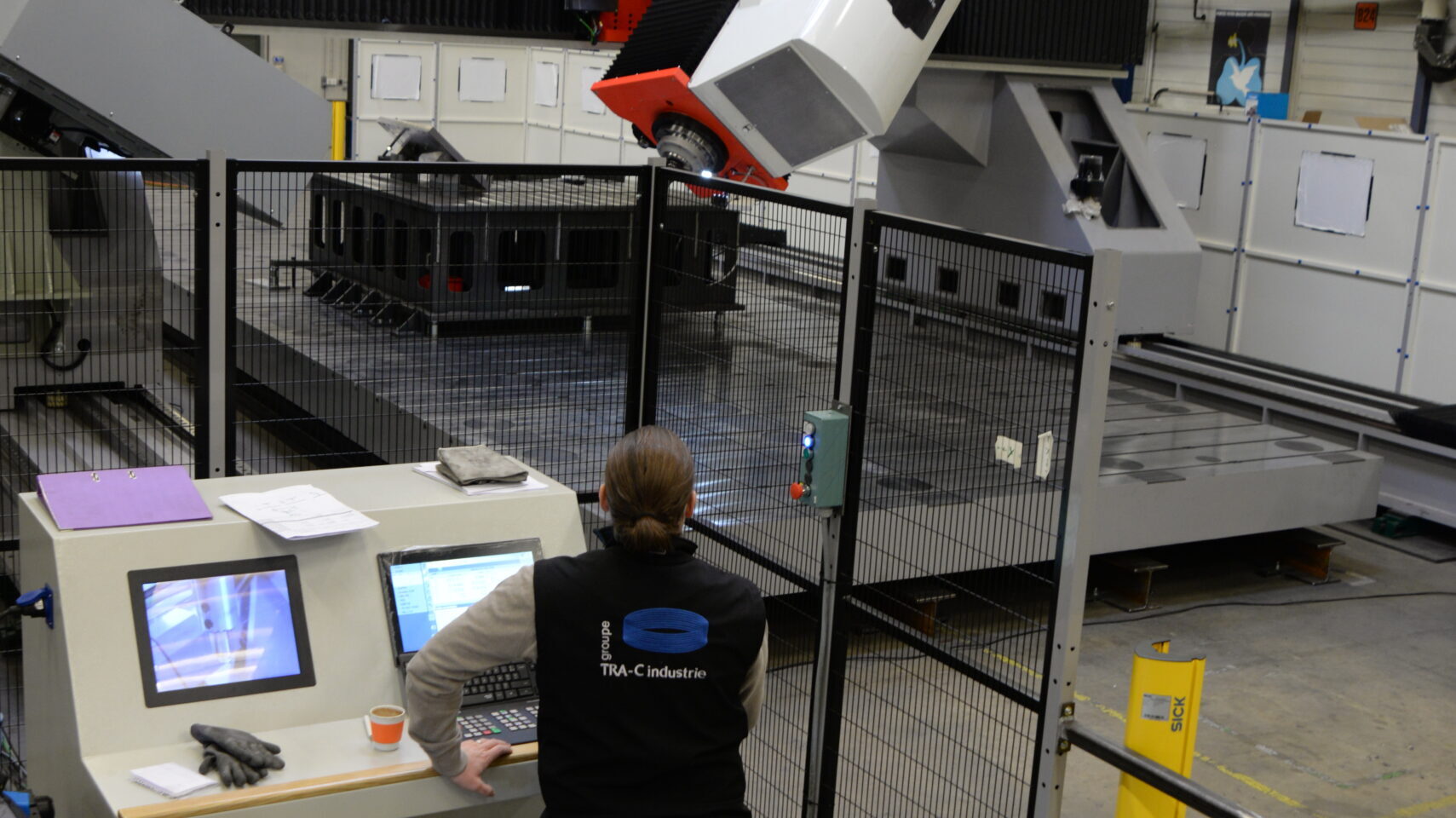
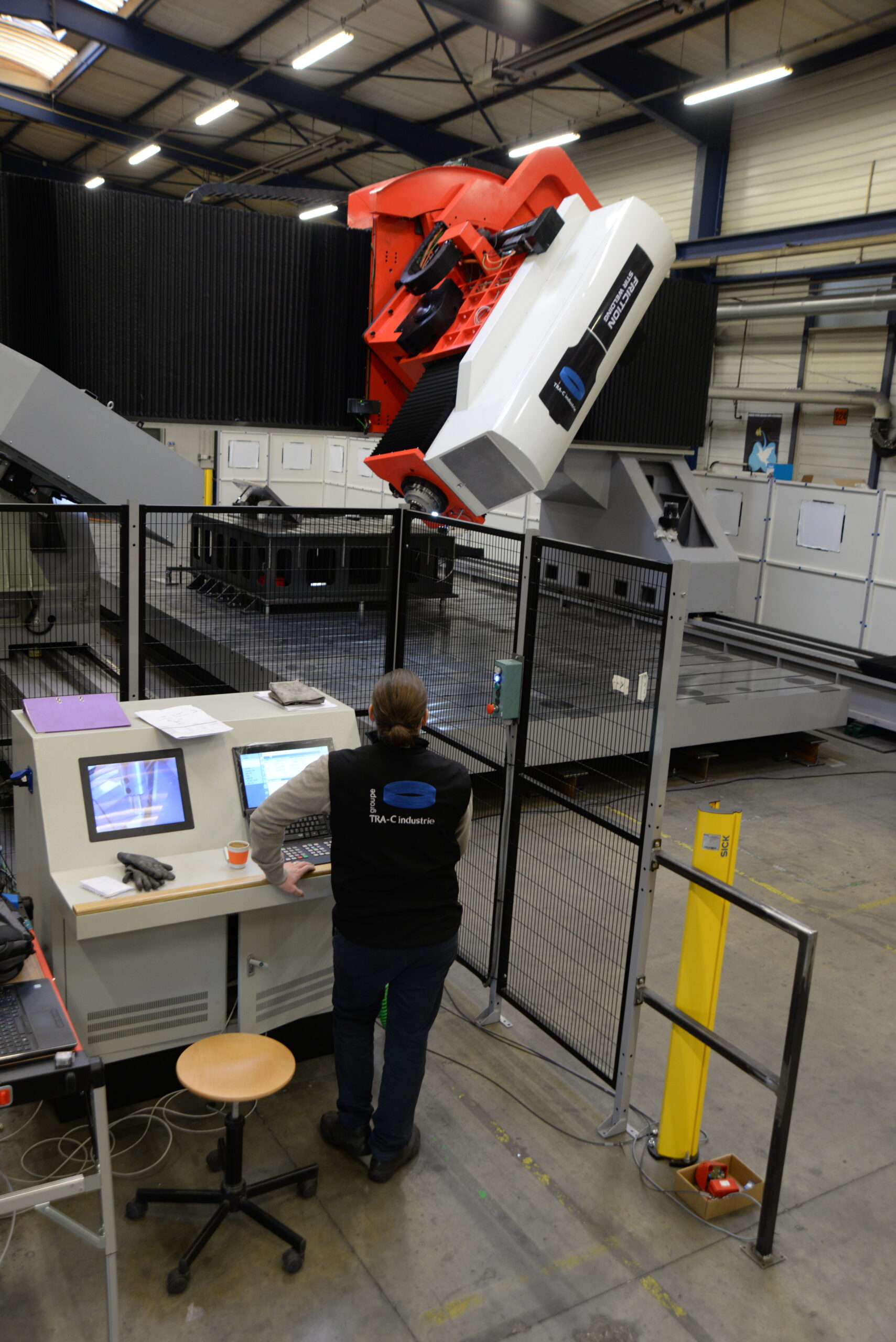
FSW robotic cells
Robotic cells are now widely used with FSW. They offer high welding precision. By working continuously, they also increase production volume.
Some companies, such as TRA-C industrie, have designed FSW welding cells capable of welding in 3 dimensions and on thin sheets, which is a great step forward in the sector…
Future innovations and outlooks for FSW
Friction stir welding, a promising technology
With many innovations and developments expected in the coming years, the future of FSW looks bright. These include the development of new alloys and welding processes…
Because of its reliability, FSW can be used in many fields. These include the transport (aeronautics, automotive, rail), space, defence and energy industries.
This should lead to new market opportunities and stimulate growth in the welding industry. This is particularly the case for aluminium and light alloys, which cannot be joined efficiently using current welding methods.
By investing in the right equipment and the necessary training, companies can take advantage of the benefits of friction stir welding technology.

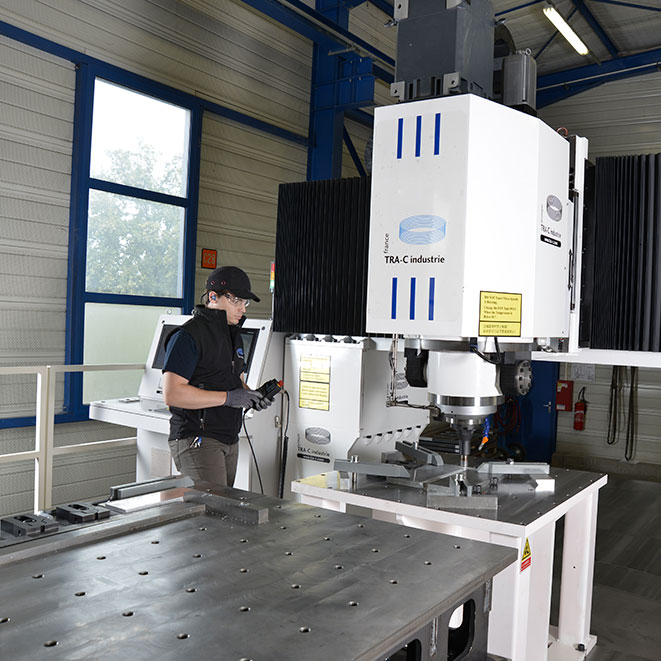
Overcoming the challenges of FSW technology
To make further progress in the welding sector, research and development must continue. The aim is to go beyond the applications already developed.
We therefore need to work closely with all the players in the industry to understand their specific needs and design appropriate solutions. Partnerships between researchers and companies to develop new applications for FSW are a good way of doing this.
We also need to democratise the use of FSW. To do this, manufacturers can ask expert companies such as TRA-C industrie to produce prototypes. This will enable them to assess the advantages of friction stir welding.
Finally, it is important to promote the benefits of FSW and encourage its use. Awareness campaigns, training programmes and innovation support initiatives are all excellent strategies!
Economic and environmental benefits of FSW
Today, there are innovative welding technologies that maximise economic benefits while reducing the ecological footprint. TRA-C industrie has designed a friction stir welding machine capable of assembling metal parts in an optimal and more environmentally-friendly way.
Thanks to a cold-welding process, this FSW technology minimises the use of excessive heat. This reduces energy consumption and costs, without releasing UV rays, smoke or toxic gases. By stimulating innovation in the metallurgy sector, it also promotes economic growth.
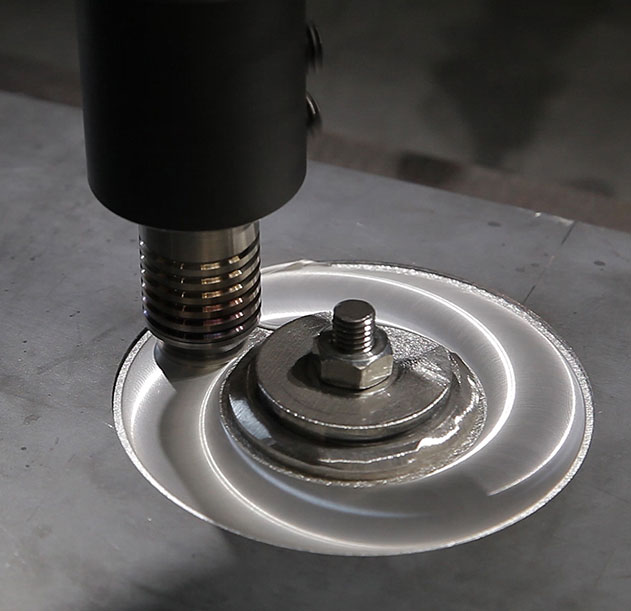

TRA-C industrie, specialist in friction stir welding
With its revolutionary and innovative solution, TRA-C industrie is now the European leader in friction stir welding. The company offers an alternative to more traditional welding techniques.
Its unique heating process enables materials that are normally difficult to weld to be assembled reliably. Its cutting-edge technology is also effective in optimising the welding of aluminium without defects or deformation, thereby preserving the properties of the initial material.
Thanks to its design office, TRA-C industrie is constantly innovating. It has been using and perfecting this process since 2009. As a result, the company is able to offer appropriate all-in-one solutions, from research to production, including machinery.
Would you like to use our friction stir welding services? Would you like to benefit from our expertise in this field? Or do you want to find out more about this innovative technology?