Boilermaking : advanced welding and fabrication
Boilermaking is the process of fabricating and welding steel components to create boilers, tanks, and other pressure vessels used in various industries, such as power generation, chemical processing, and oil and gas refining. Boilermakers are the skilled tradespeople who carry out these tasks, and they are responsible for constructing and maintaining the vessels that are essential to the safe and efficient operation of industrial processes.
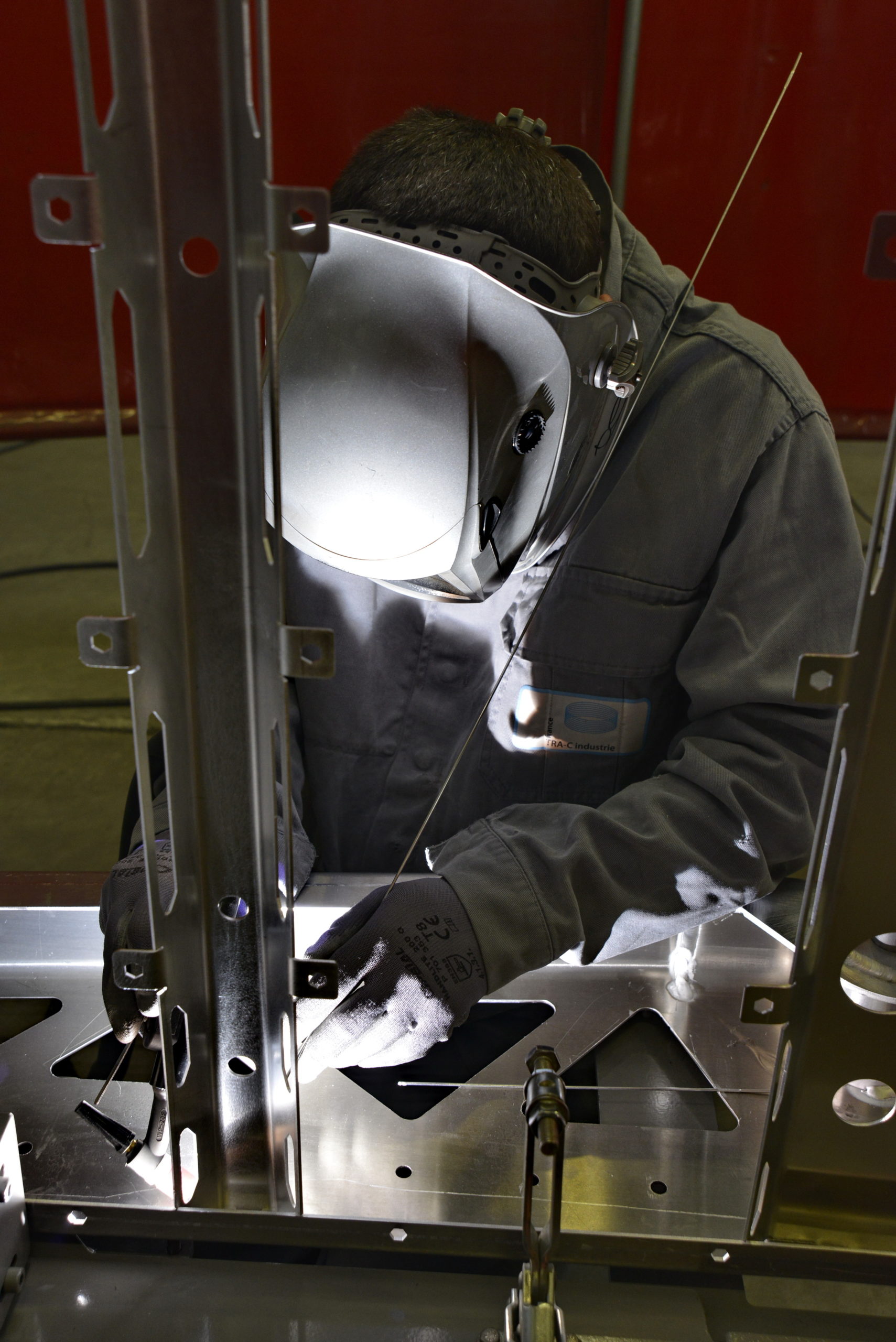
A quick history of boilermaking
The history of boilermaking can be traced back to the early days of the Industrial Revolution, when the demand for steam power led to the development of the first boilers. These early boilers were typically made of wrought iron and were used to power steam engines in factories and mines. As the demand for steam power increased, the size and complexity of boilers grew, and new materials and construction techniques were developed to meet the evolving needs of industry.
Today, boilermakers work with a wide range of materials, including carbon steel, stainless steel, and alloy metals, and they use advanced welding and fabrication techniques to create vessels that can withstand extreme pressures and temperatures. Boilers, for example, are used to generate steam that is used to power turbines in electric power plants, while tanks and pressure vessels are used to store and transport gases and liquids in various industrial processes.
The stakes for today’s boilermakers
Boilermaking is a highly skilled trade that requires a combination of technical knowledge and practical experience. Boilermakers must be able to read and interpret technical drawings and specifications, and they must have a thorough understanding of welding, machining, and metalworking techniques. They must also be familiar with a wide range of tools and equipment, including plasma cutters, oxy-fuel torches, and hydraulic presses.
The work of a boilermaker typically involves a variety of tasks, including cutting and shaping metal components, welding them together, and testing the finished product for leaks and other defects. Boilermakers must be able to work with a high degree of precision and accuracy, as even small flaws in a pressure vessel can have serious consequences.
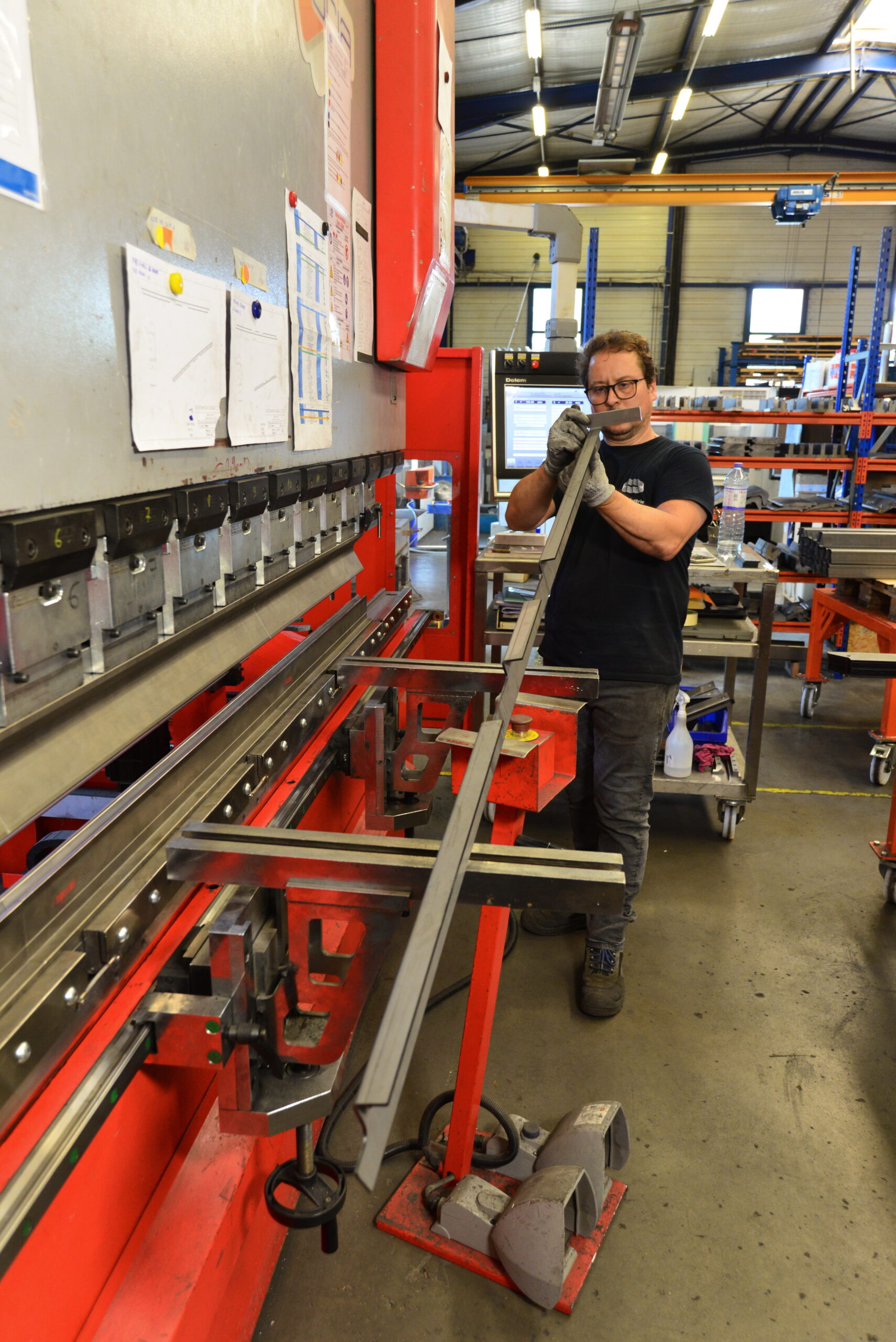
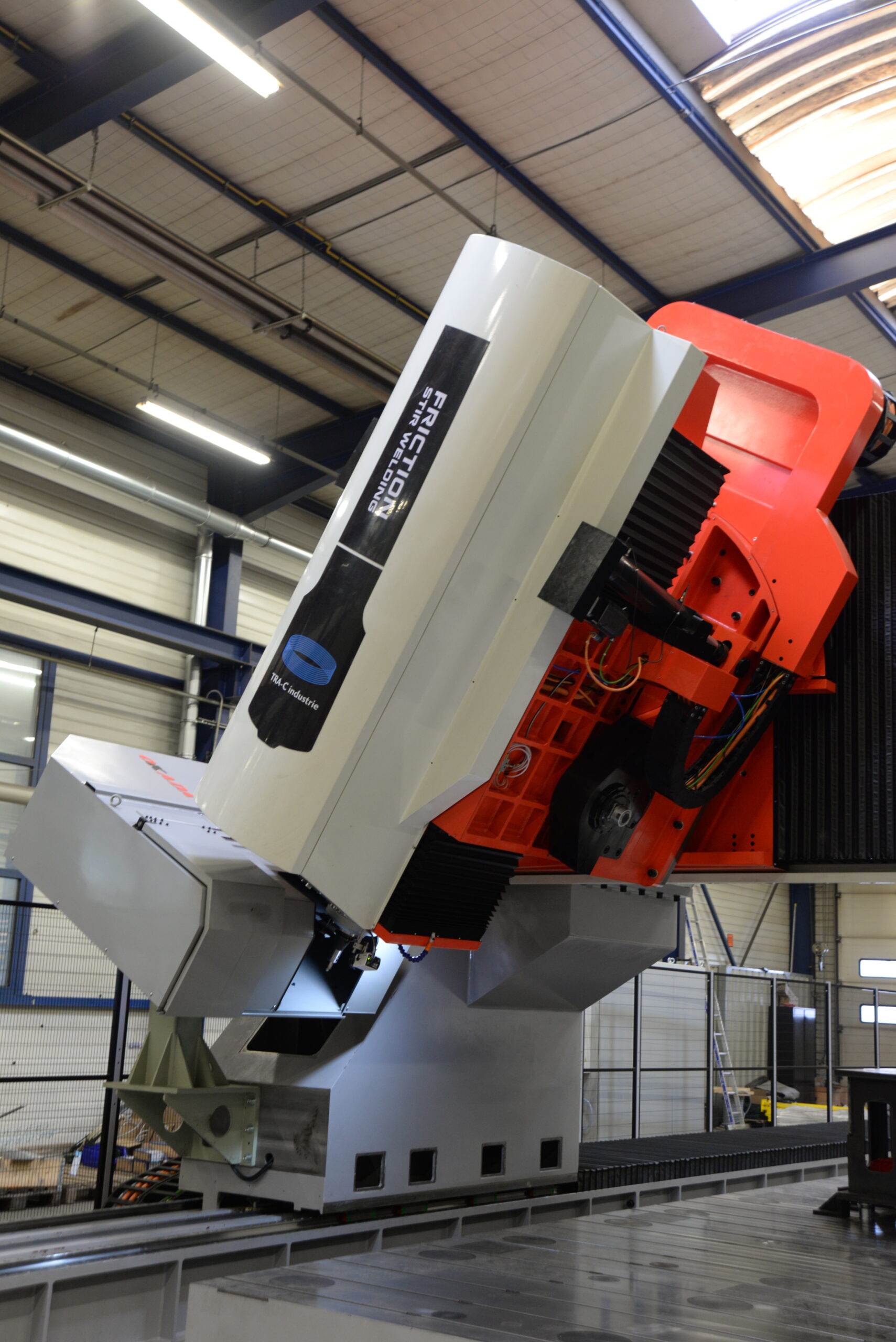
Safety first
Safety is a top priority in boilermaking, and boilermakers must follow strict procedures and protocols to ensure that they and their colleagues are protected from the hazards of the job. This includes wearing appropriate personal protective equipment, such as welding helmets and steel-toed boots, and following established safety guidelines for working with hazardous materials and equipment.
In addition to constructing new pressure vessels, boilermakers are also responsible for maintaining and repairing existing ones. This can involve tasks such as replacing worn or damaged components, cleaning and inspecting the interior of the vessel, and repairing leaks or other defects. Boilermakers must be able to identify and diagnose problems with pressure vessels, and they must have the skills and experience to carry out repairs safely and effectively.
Compliance to safety regulations and quality standards
One of the key challenges in boilermaking is ensuring that the vessels being constructed meet the strict safety and quality standards required by industry regulations. This requires careful attention to detail at every stage of the process, from the initial design and fabrication to the final testing and inspection. Boilermakers must be able to work collaboratively with engineers, project managers, and quality assurance personnel to ensure that the finished product meets all necessary standards and specifications.
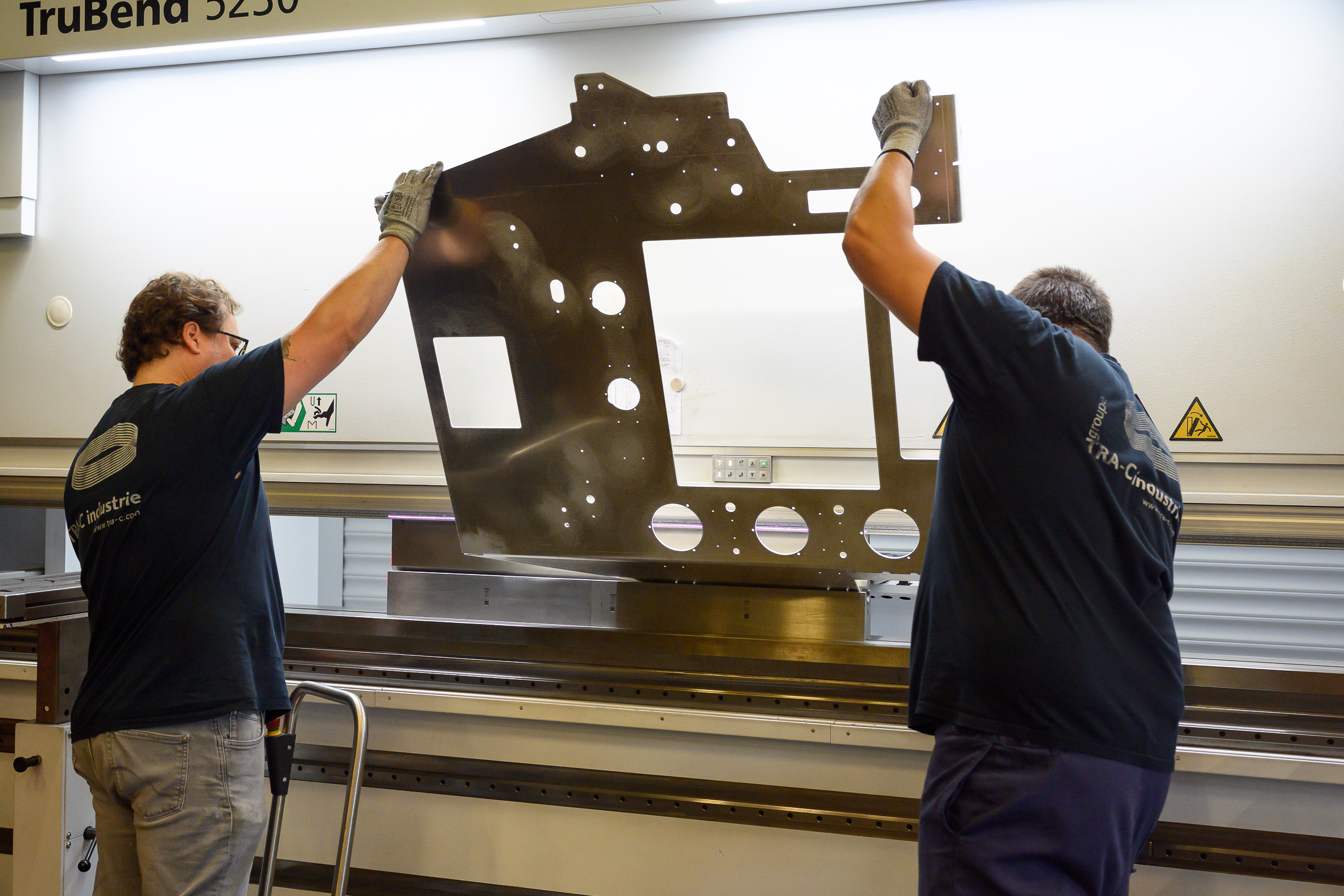
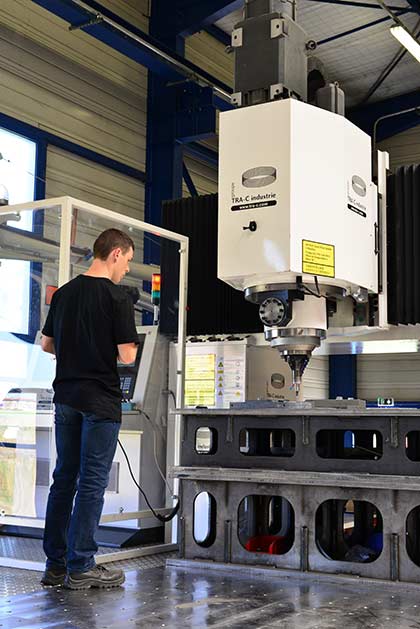
The need for innovation and continuous improvement
Another important aspect of boilermaking is innovation and continuous improvement. As new materials and technologies become available, boilermakers must be able to adapt and adopt these innovations to improve the safety and efficiency of the vessels they create. This can involve using new welding techniques, such as laser or friction stir welding, or incorporating advanced sensors and monitoring systems to detect and prevent defects before they become a problem.
In addition to technical skills, boilermakers must also possess a range of soft skills that are essential to their work. These include strong communication skills, both verbal and written, as well as the ability to work effectively as part of a team.