Automated welding in the automotive industry has become an essential pillar of modern production lines. Thanks to industrial robotics and advanced technologies, it guarantees optimum precision and increased productivity.
By reducing human error and improving weld quality, these systems enable manufacturers to optimize costs and accelerate production. Artificial intelligence and machine vision play a key role in this transformation.
Over and above performance, automation also enhances operator safety by limiting their exposure to risks. This makes automation an essential lever for a more competitive and innovative automotive industry.
But what exactly is automated welding? What methods can be automated? Advantages, drawbacks, applications… In this article, TRA-C industrie tells you all about automated welding for car manufacturing!
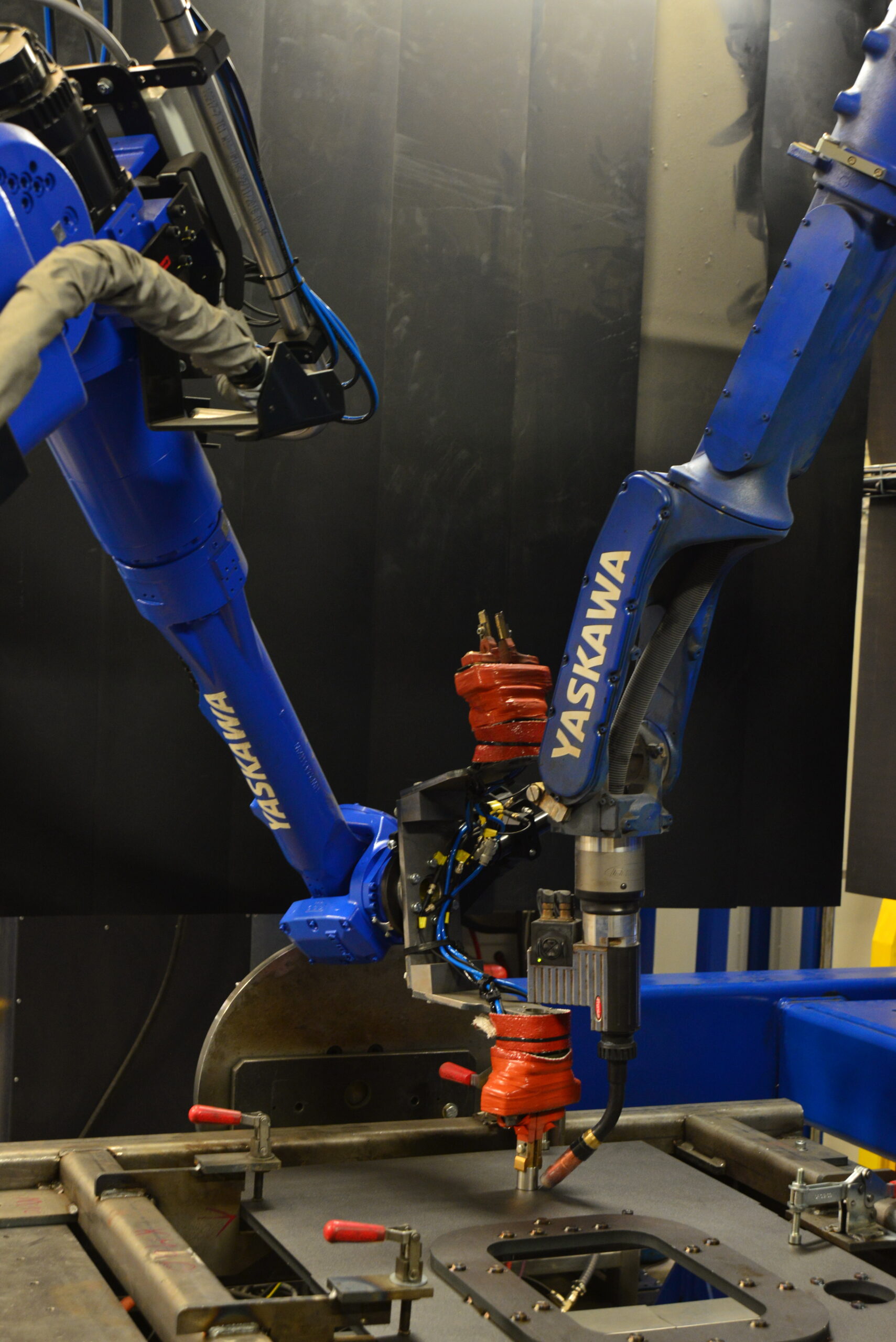
What is automated welding?
Automated welding is an industrial process that uses robots or programmed machines to produce welds autonomously. It relies on cutting-edge technologies to produce precise, repetitive welds without direct human intervention.
This process integrates various welding procedures, such as arc, resistance and laser welding. Each method is chosen according to the materials to be joined, technical constraints and production requirements…
Automated systems are equipped with sensors and control software that adjust welding parameters in real time. In this way, they guarantee compliance with the specifications defined by production engineering.
Finally, the integration of automated welding into a production line relies on robotic arms, conveyors and digital interfaces. These elements ensure perfect synchronization with the other vehicle assembly stages.
Automated welding techniques in the automotive industry
There are many different automated welding processes in the automotive industry. Six major methods require the use of specialized robots, each bringing a specific function to vehicle assembly.
Resistance spot welding
Resistance spot welding is commonly automated in the automotive industry. It works by applying heat and pressure to the parts to be welded, causing them to melt at the point of contact thanks to electrical resistance.
Once cooled, this fusion creates a resistant, invisible and solid bond, with no apparent trace of welding. This process has therefore become essential to automotive manufacturing, particularly with the advent of robots, which have improved its efficiency and profitability!
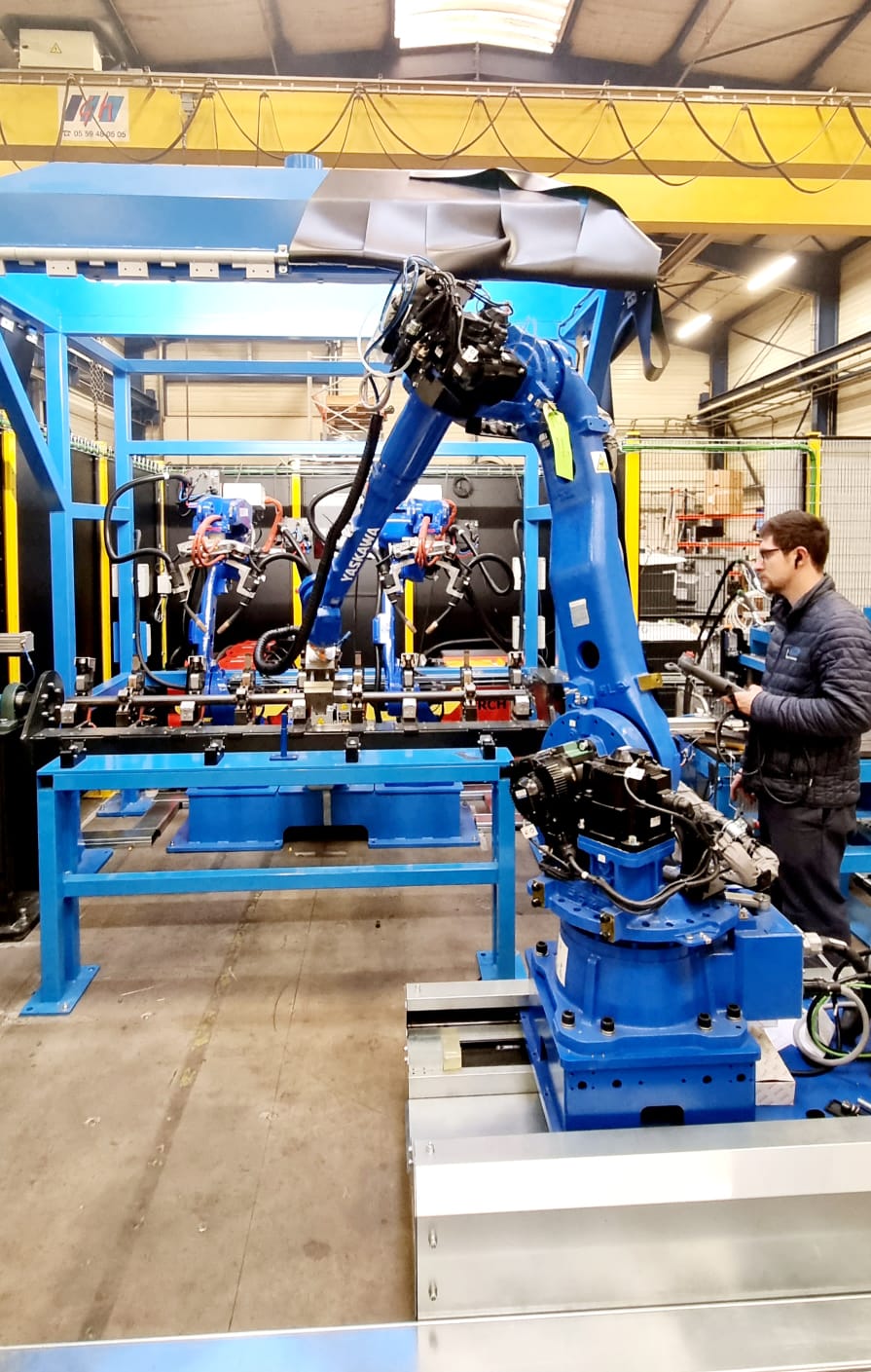
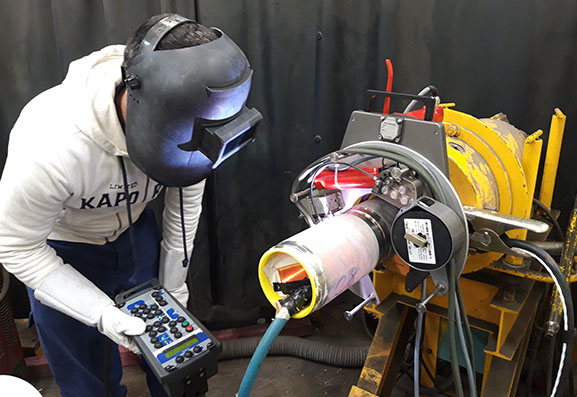
Laser welding
Laser welding is another method of automated welding in the automotive industry. It uses a high-powered laser beam to heat and melt materials at the joining point, facilitating their fusion.
Thanks to its precision and speed, this welding process guarantees solid, uniform assemblies. Its efficiency makes it an ideal solution for mass production, where consistency and quality are essential.
Arc welding
Arc welding is a technique frequently used in the automotive industry. It relies on the heat of an electric arc between an electrode and the metal parts. A shielding gas facilitates arc movement and stabilizes the process…
As the metal melts at the joint, it fuses before solidifying into a lasting bond. Inert gas (MIG) and active gas (MAG) welding robots play a key role in automating this process.
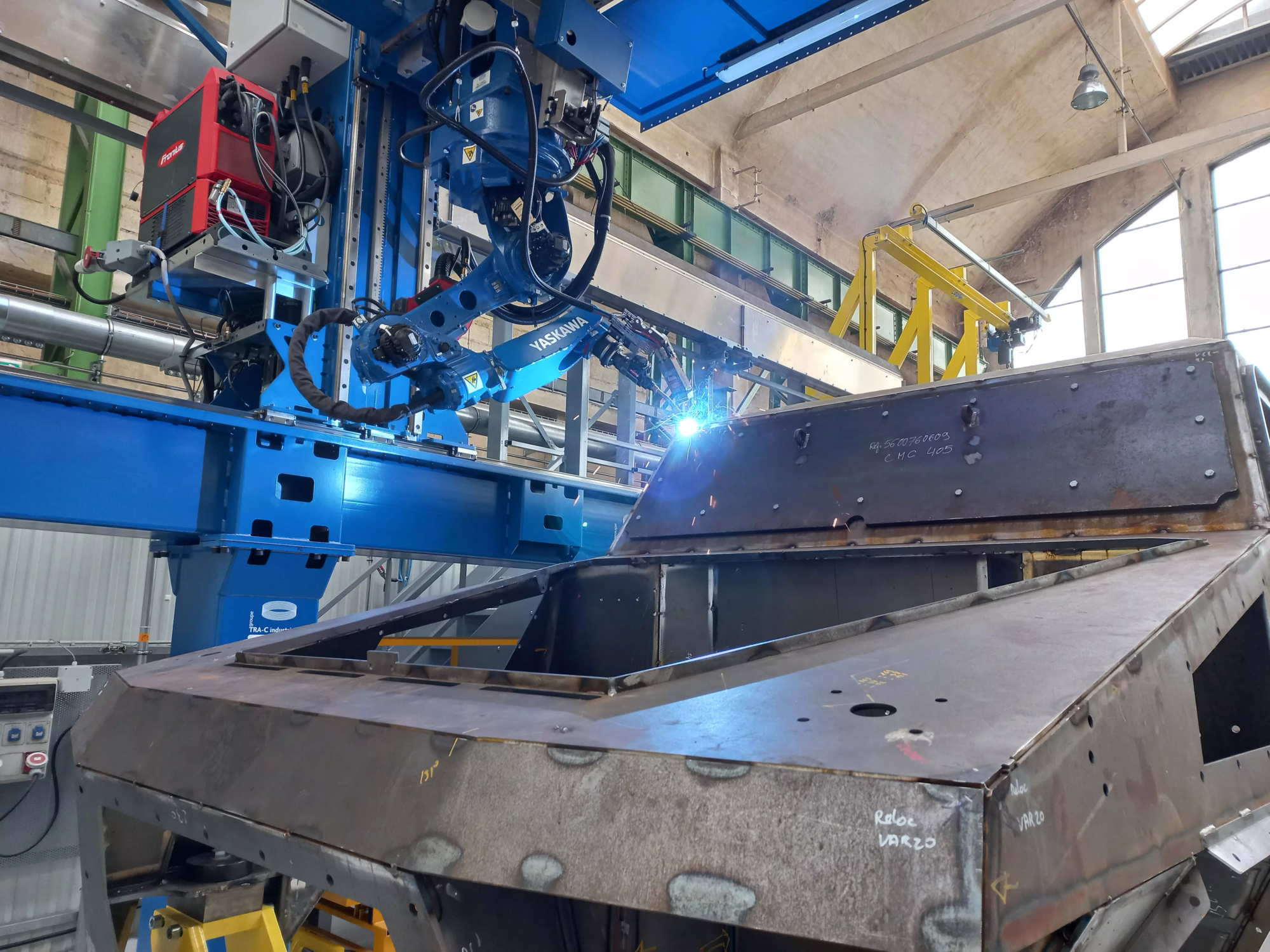
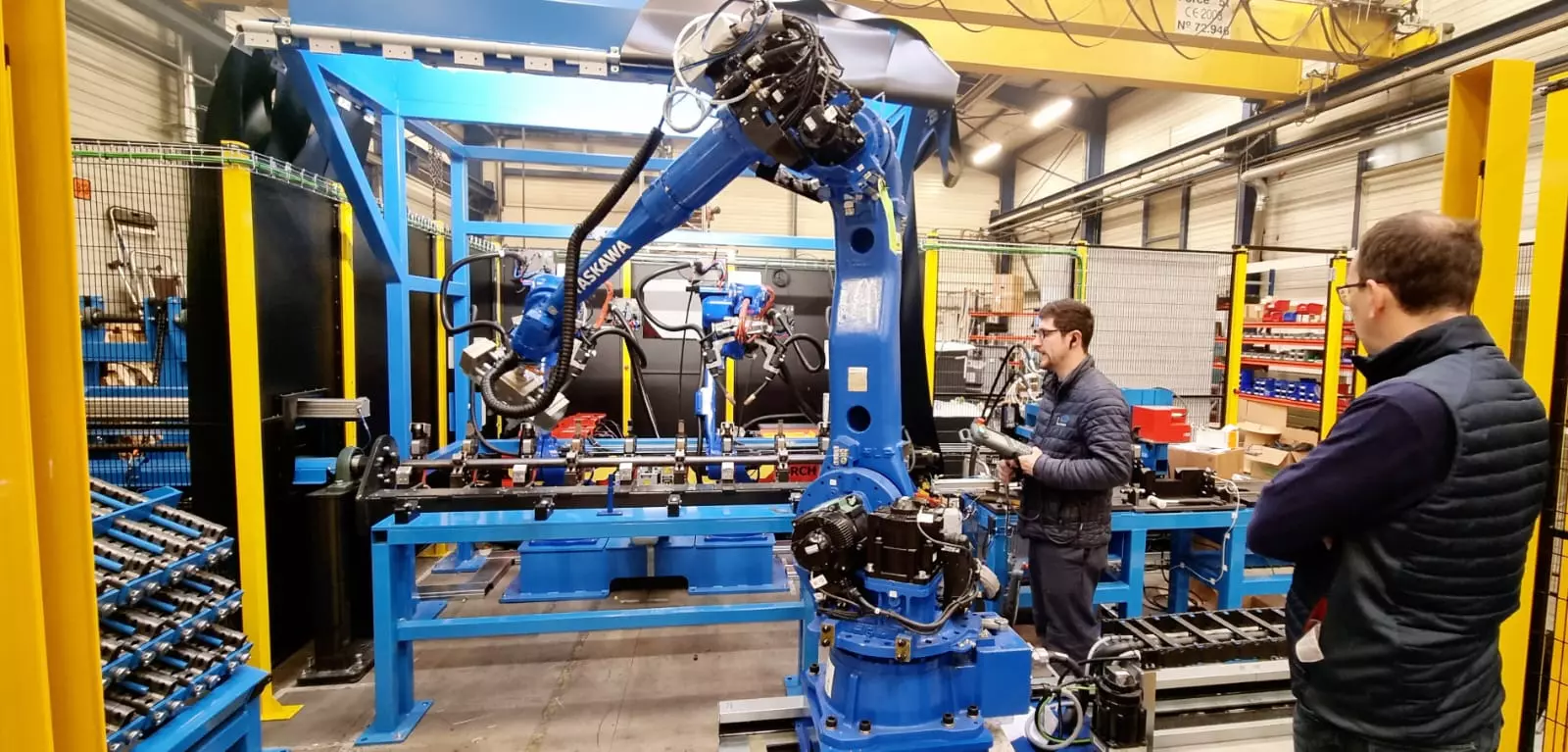
Gas tungsten arc welding
Gas tungsten arc welding is another technique of automated welding in the automotive industry. It operates by means of an electric arc between an electrode and the parts to be joined, and uses an inert gas to protect the weld zone.
The special feature of TIG welding lies in the tungsten electrode, which has the highest melting point of all metals. The result is a more precise and resistant weld, adapted to the demands of automotive manufacturing.
Thin arc welding
Thin arc welding is a method specifically used for thin components requiring special attention. This technique can be used to weld materials that are more delicate, where precise heat management is essential.
Thin sheet welding, for example, presents challenges, as it can lead to deformation and alter material properties. This refined approach guarantees a stable weld without distorting sheet metal or causing metal fractures!
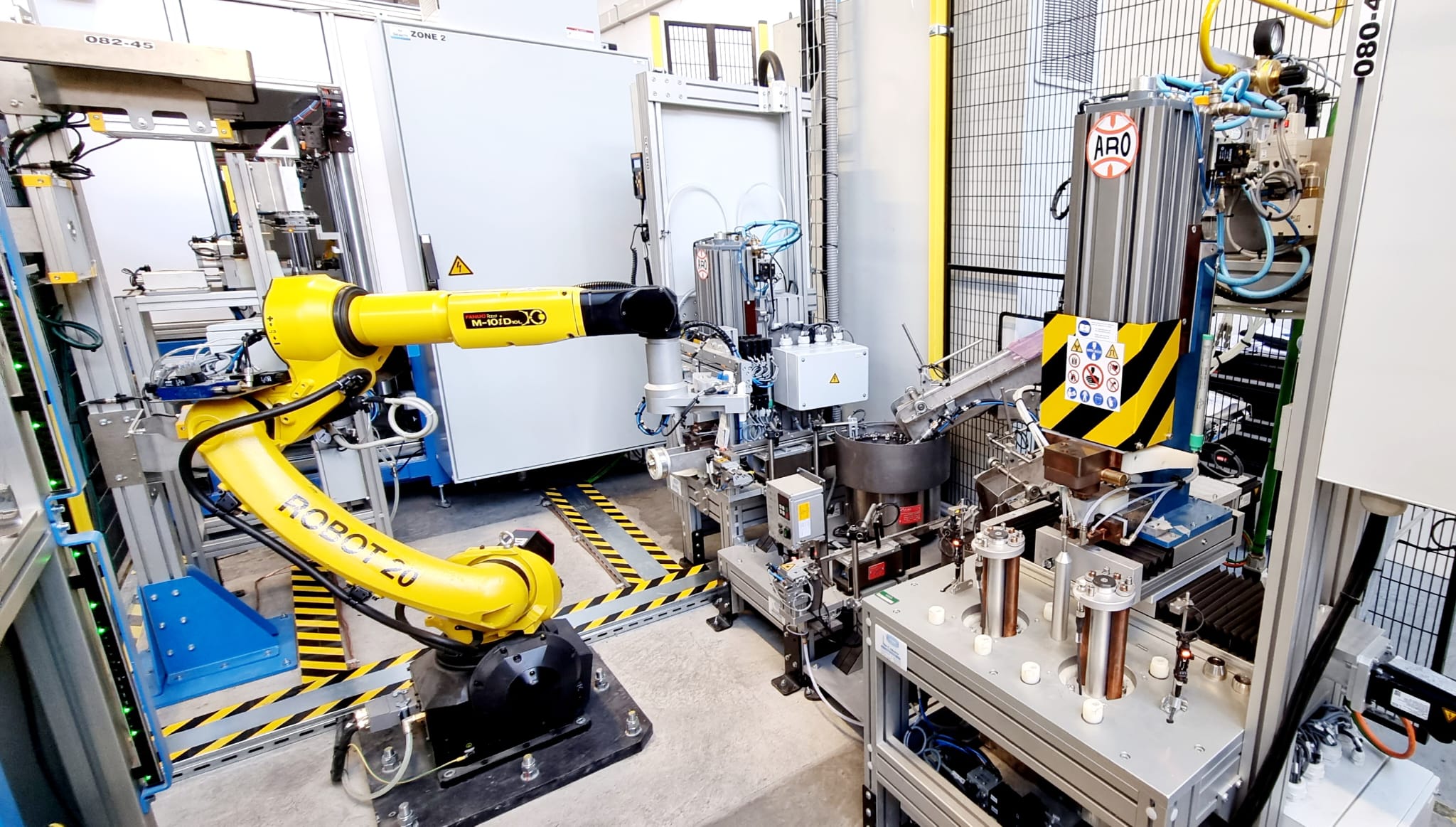
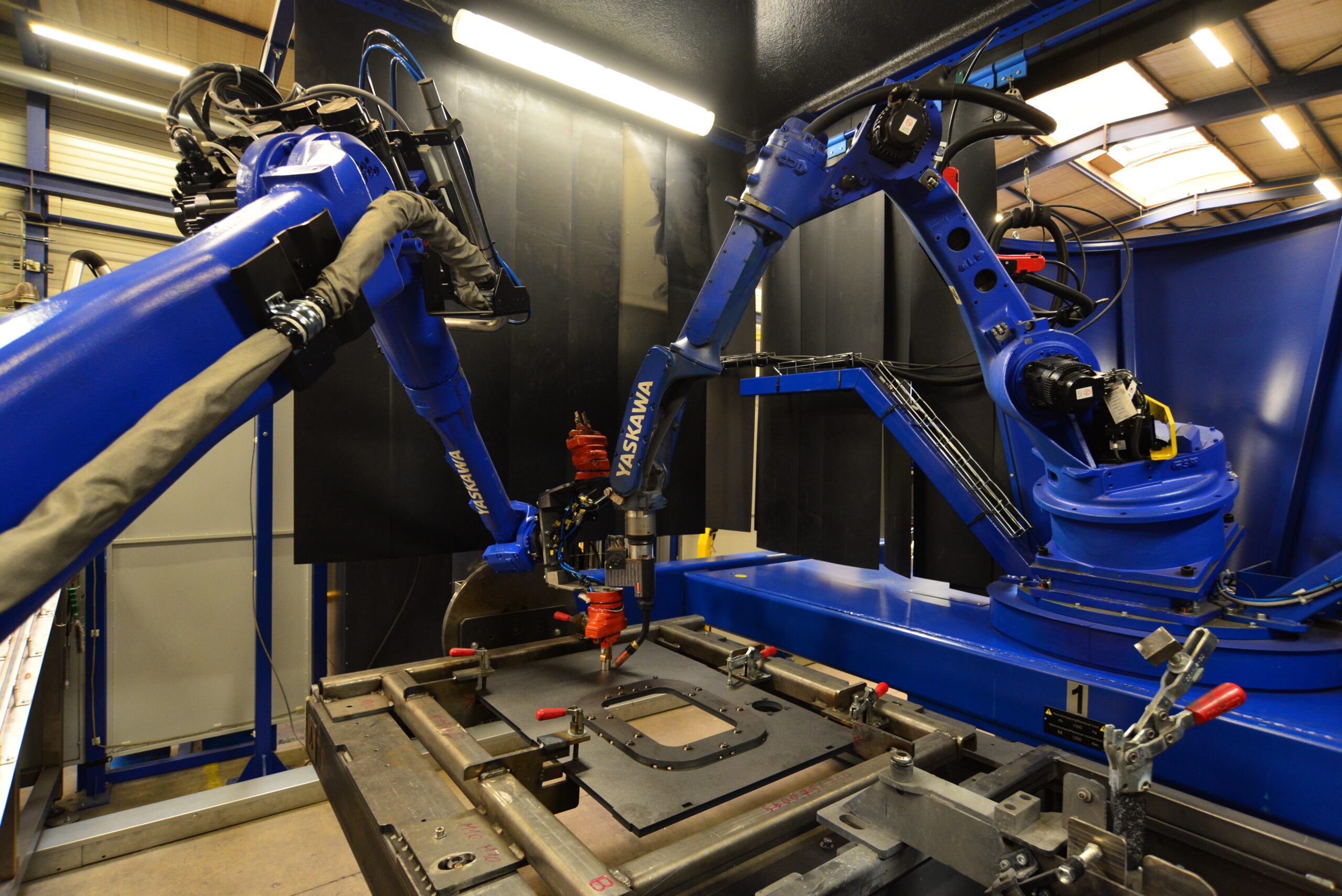
Plasma welding
Plasma welding is a welding technique similar to low-thickness arc welding, but with one major difference. The plasma arc can be separated from the shielding gas, allowing greater flexibility in process control.
The plasma is directed through a nozzle, creating a more precise, focused arc. This enables manufacturers to weld metal parts as thin as 0.1 mm, offering an ideal solution for high-precision welding.
Friction stir welding
Finally, friction stir welding (FSW) is used in the automotive industry to weld difficult materials such as aluminum. Friction is generated by a rotating tool that moves along the weld seam. This tool heats the material without melting it, and without adding metal.
This welding process produces strong assemblies with low thermal distortion. Automated, it ensures consistent quality and reduces human error, making it an ideal solution for high-precision automotive applications…
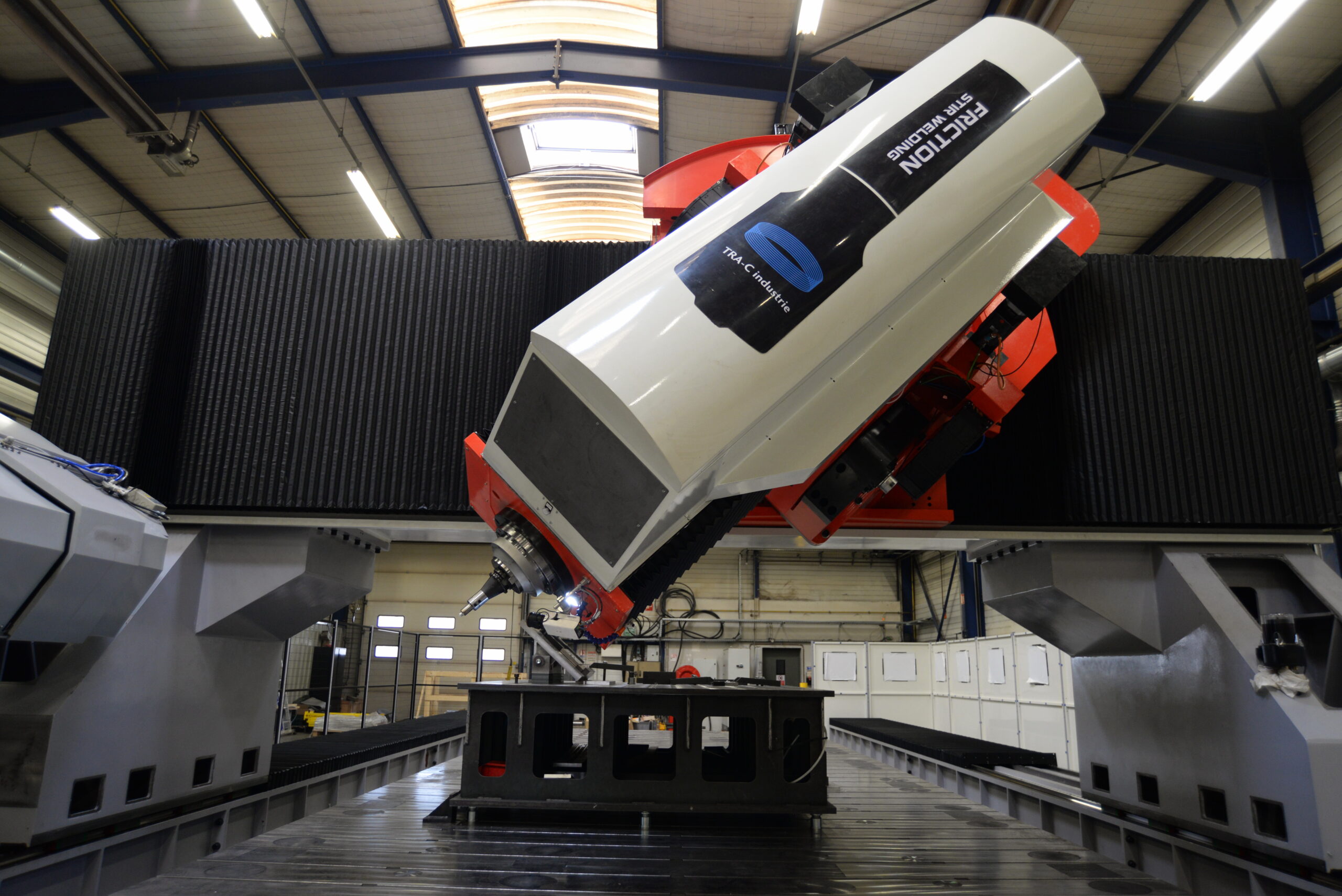
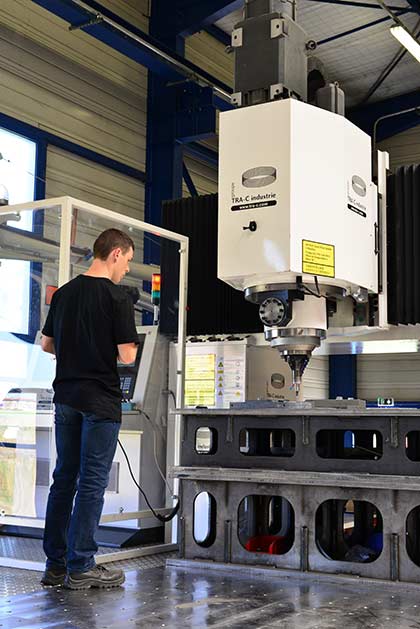
The benefits of automated welding in the automotive industry
Automated welding in the automotive industry improves efficiency, productivity and safety. Specialized machines and robots offer high precision and optimize manufacturing processes, while creating considerable advantages for factories:
- Improved efficiency and productivity: first and foremost, welding robots speed up operations. They reduce production time and increase assembly line output;
- Increased precision and quality: by eliminating human error, these robots also offer a high level of precision and consistent quality throughout the automotive manufacturing process;
- Optimization of floor space: robots require fewer staff, freeing up space in factories. This means better organization and greater flexibility for integrating other equipment;
- Improved safety: robots do not lose concentration and can perform repetitive tasks in complete safety. This reduces the risk of accidents due to human fatigue;
- Reduced waste: thanks to their precision, robots also minimize production waste and consumables. They therefore enable more efficient, environmentally-friendly vehicle manufacturing;
- Reduced wastage due to human error: automation finally makes it possible to reduce the risk of human error, which is responsible for a large proportion of waste. This ensures more profitable and environmentally-friendly operations in the sector.
The disadvantages of robotic welding
Despite the many advantages of automated systems, there are a number of drawbacks to their implementation. Integrating robotic welding solutions into the manufacturing process is costly. These tools are technologically advanced, and their production involves considerable expense!
What’s more, these robots require human supervision. Operators will need specialized training to manage welding automation, which means additional costs and training time.
Robots are also less flexible than humans in performing various tasks. Whereas a human employee can take on several roles, robots are designed for specific tasks and cannot change function without complex reprogramming.
Another major drawback is the lack of decision-making ability of robots. Although they are programmed to perform specific tasks, they cannot react to unforeseen situations in the same way as humans, which limits their adaptability.


TRA-C industrie, expert in automated welding for the automotive industry
TRA-C industrie is one of Europe’s leading manufacturers of ergonomic welding machines and robot cells. Thanks to our in-depth expertise, we are able to develop automated welding solutions for the automotive industry, tailored to every need.
Our unique approach places training and integration at the heart of the development process. Trained in-house, operators can then supervise and maintain the robots, overcoming one of the main challenges of automation!
This strategy also enhances plant flexibility. By training local, competent teams, TRA-C helps companies adapt to an automated environment and supports employee autonomy in the manufacturing process.
Finally, we work with renowned robot integrators such as Fronius and Fanuc, to guarantee optimal machine integration. These partnerships ensure maximum system reliability and performance in demanding industrial environments.