What is Friction Welding?
Friction welding relies on friction to join materials. The process doesn’t use methods for heating the materials externally but solely depends on the energy released from the friction. This is the key difference between friction welding and conventional fusion welding.
Friction welding is a solid-state technique that can produce joins that are often as strong as the constituent metals. Various industries rely on this process for welding parts.
The Friction Welding Process
When two materials are rubbed against one another, heat energy is released due to friction. The higher the pressure and speed of this rubbing, the more energy is generated.
This principle is employed in friction welding, where the components for joining are rubbed against each other at incredibly high speeds and pressures. This results in mechanical friction between the parts.
The heat energy released will cause the materials to become viscous around the point of contact. This causes the metals to mix at the join line, creating a robust bond between the two.


Types of Friction Welding
Friction welding is an umbrella term covering all kinds of welding processes that use friction to create a bond between materials. However, various techniques fit this definition, and these all use slightly different approaches to achieve welds between metals.
The first approach is rotary friction welding. During this process, one of the two materials is rotated over the surface of the other metal. The rotation occurs at the point where the metals are to be joined. This technique relies on compressive axial force paired with a high rotation speed. The end result of such methods is that the metals are plasticised, which will cause the components to join at the point of contact.
Next is linear friction welding. One component oscillates rapidly relative to the other to create welds using this technique. Substantial compressive forces are applied to the two metals alongside the reciprocating movement. This causes significant heat output at the point of contact, leading to plastic deformation of the parts. The materials mix, resulting in a very strong bond between the components.
Friction stir welding is another approach that is commonly used to bond metals to one another. This process uses a specialised tool to generate heat between the materials due to friction. The tool is generally cylindrical in shape and uses a specially designed pin to create the weld. This pin is driven along the point of contact between the metals and is rotated to soften the metals. The stirring motion of the tool mixes the viscous materials with each other to create a strong bond.
Finally, friction stir spot welding is also used in various industries. This is very similar to friction stir welding, but there is one crucial difference. While the tool is moved along the seam between components in friction stir welding, in friction spot welding, the tool is rotated in a single spot. It spins in place and is then lifted out, which creates an excess hole.
Pros of Friction Welding
Not all welding techniques are created equally. Instead, the appropriate method often depends on the properties of the materials that need to be joined. For different metals, the strength of the bond relies on using the correct approach. With that being said, there are certain advantages of friction welding over other techniques.
For example, friction welding can be valuable for joining metals that are dissimilar to one another. This is often referred to as bimetallic friction joining. In essence, this means that two kinds of metal can be welded to one another without needing pre-treatment steps. This is extremely valuable for engineers, as they can join dissimilar metals like aluminium and steel.
Generally, all forgeable metals can be welded using a friction welding approach. This allows manufacturers much more freedom to innovate, as they can create robust joins between metals with different properties.
Another benefit of friction welding is that no external heat or flux is needed to create joints between metals. This makes the process relatively straightforward, energy-efficient and less messy than traditional welding approaches.
Additionally, friction welding is a very reliable process with a much lower incidence of defective welds than other methods. Solid-state welding results in far fewer defects than fusion welding while still creating mechanically robust bonds. On top of this, it is also a speedy way to weld materials together. It is one of the quickest ways to bond metals and is orders of magnitude faster than fusion welding.
Ultimately, the friction welding process has many advantages, especially when engineers need to create bimetallic welds between materials. Metals like steel and aluminium are challenging to weld to one another using fusion welding, but it is possible to do this relatively easily with friction welding. There are next to no downsides to the process. It is efficient, fast and produces little waste, so it is one of the most popular solid-state welding approaches.
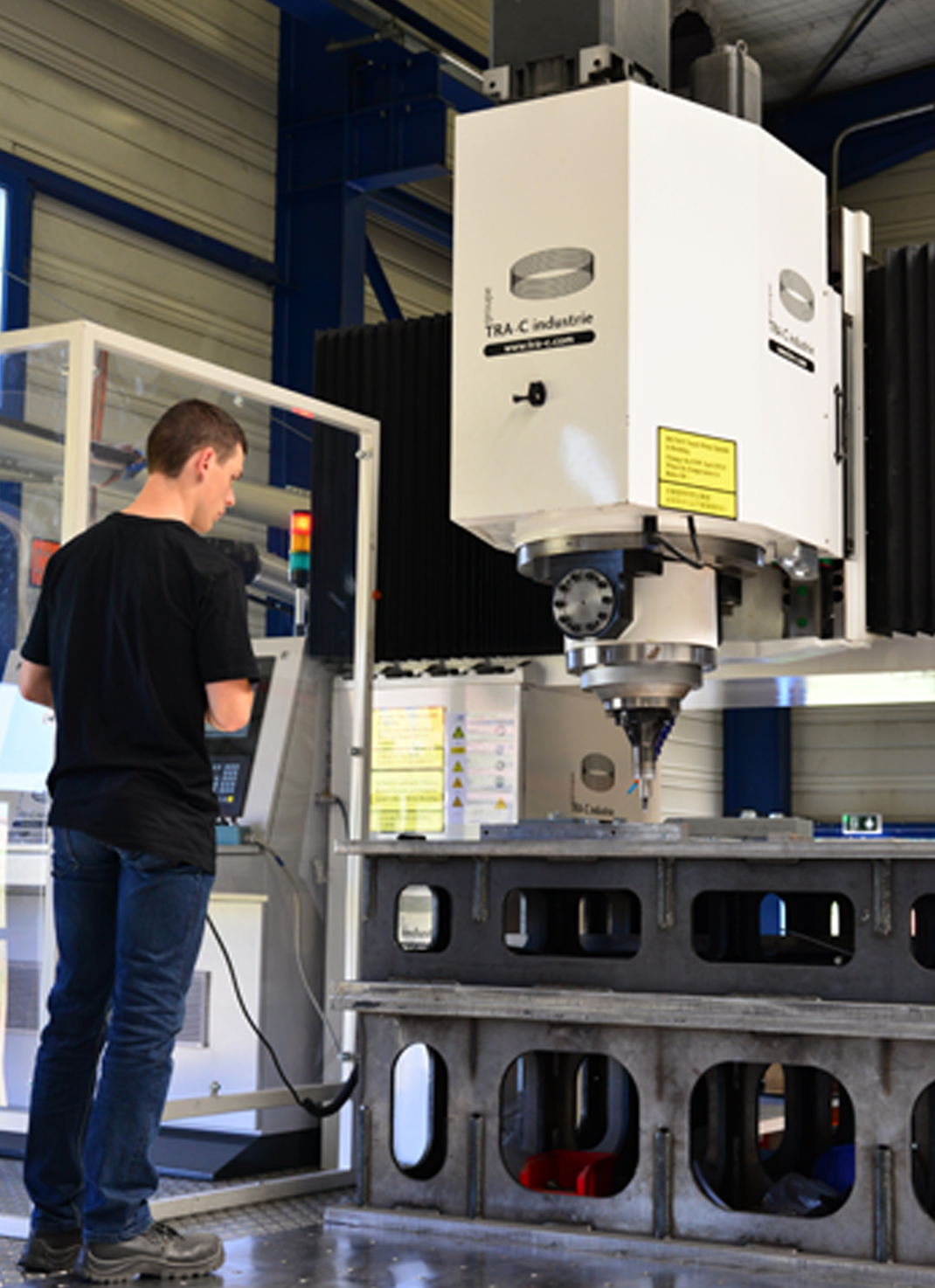

TRA-C industrie: a Friction Welding Specialist
When it comes to friction stir welding, few companies have the experience of TRA-C Industrie. As one of the early adopters of the innovative technology, the business has refined friction stir welding considerably since 2009.
By placing a considerable amount of focus and resources into R&D, TRA-C has cemented itself as the premier expert in friction stir welding in Europe. From research into new and innovative techniques to the development of cutting edge machines and tools, TRA-C is one of the industry leaders when it comes to industrial friction welding and manufacturing.
The popularity of the friction welding approach for joining alloys and materials that are challenging to work with using fusion welding has helped TRA-C develop welding techniques that have far-reaching uses across industries.
In summary, friction welding is a joining technique that relies on mechanical heating via friction rather than electrical resistance (which is used in arc welding). Friction welding can be a much more reliable method of bonding metals to one another and can also produce bimetallic joins with little to no preparation. This makes the approach ideally suited for certain industries like automotive and aerospace engineering.