FSW interests in the aerospace industry
FSW in the aerospace industry represents a major breakthrough in the assembly of metal structures. This process of friction stir welding differs due to its absence of fusion, resulting in stronger, more homogeneous joints.
Primarily used to weld aluminum alloys, FSW meets the stringent requirements of lightweight, high-performance aircraft. Its ability to reduce defects and thermal stresses makes it an ideal alternative to traditional methods.
Thanks to its precision and automation, FSW optimizes the manufacture of fuselages, tanks and other critical components. Its growing adoption is the proof of its impact on the efficiency and reliability of aeronautical structures.
But what are the aerospace industry welding requirements? And what are the advantages of this welding process over other methods? In this article, TRA-C industrie shares with you the principles, benefits and applications of FSW for the aerospace industry…

Aerospace welding challenges
Aluminum and its alloys are key materials in aerospace engineering, thanks to their light weight and excellent mechanical strength. Their low density makes it possible to design lightweight, high-performance aeronautical structures, thus reducing fuel consumption.
However, these advantageous properties pose challenges for joining, especially welding. Aluminum’s relatively low melting point and low reactivity complicate the application of traditional welding techniques.
Conventional fusion welding processes often result in structural defects such as porosities, cracks and thermal stresses. These imperfections compromise the strength of welded joints and increase the risk of deformation.
Faced with these challenges, the aerospace industry is looking for more suitable alternatives, capable of ensuring homogeneous welds without material deterioration. The development of advanced techniques such as FSW responds to this need, offering more reliable, high-performance solutions.
What is friction stir welding?
Friction stir welding (FSW) is a solid-state welding process that uses a high-speed rotating tool. Pressed along the joint line of the parts to be joined, it generates heat by friction. It thus enables materials to be assembled without reaching their melting point.
As the tool passes over it, the material is softened and kneaded, forming a weld bead. This mechanical action mixes the materials of the two parts, creating a homogeneous, robust weld…
Thanks to this approach, friction stir welding minimizes residual stresses and preserves the integrity of the welded parts. FSW in the aerospace industry therefore ensures stronger assemblies, contributing to aircraft lightness and performance.
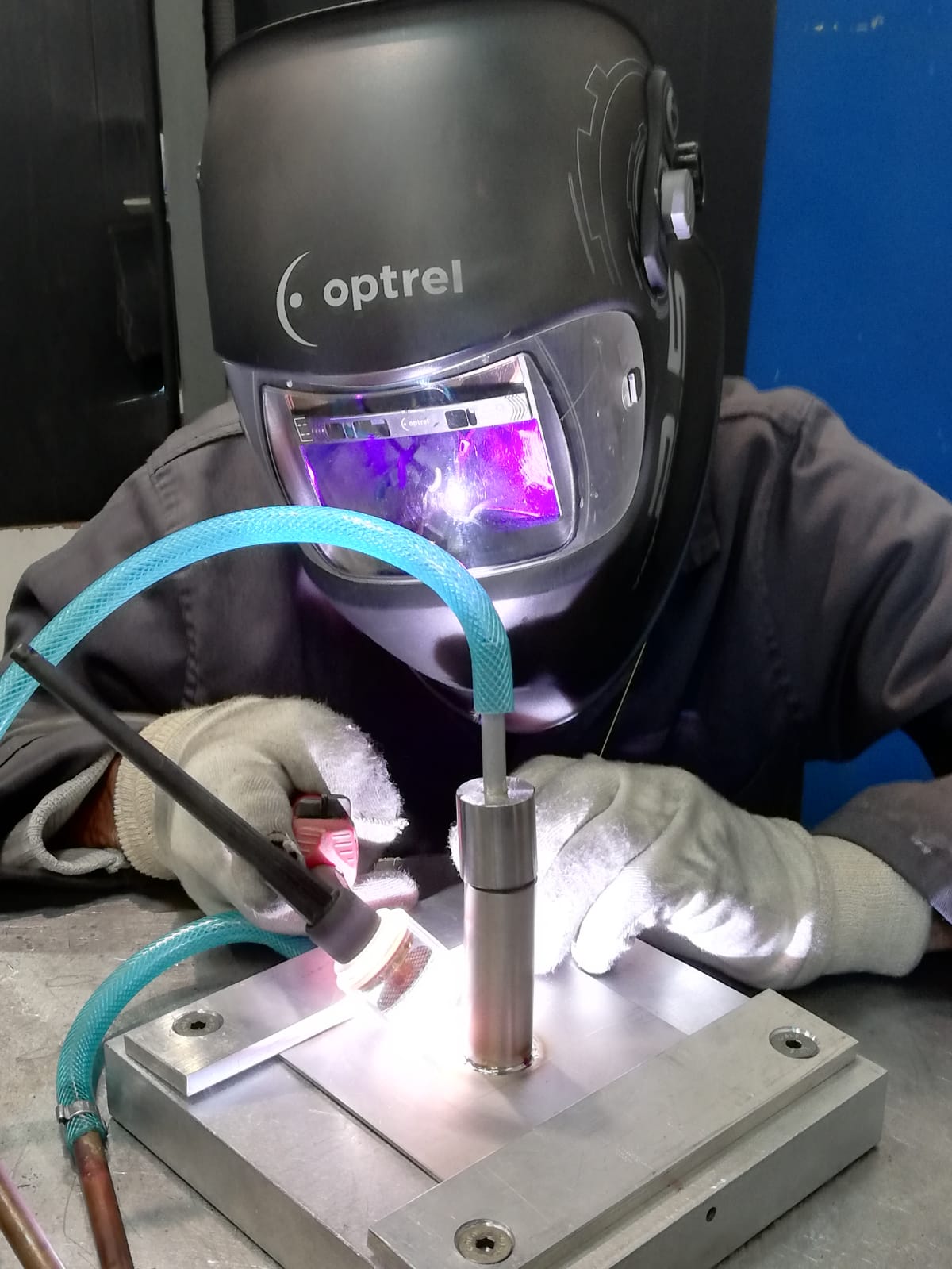
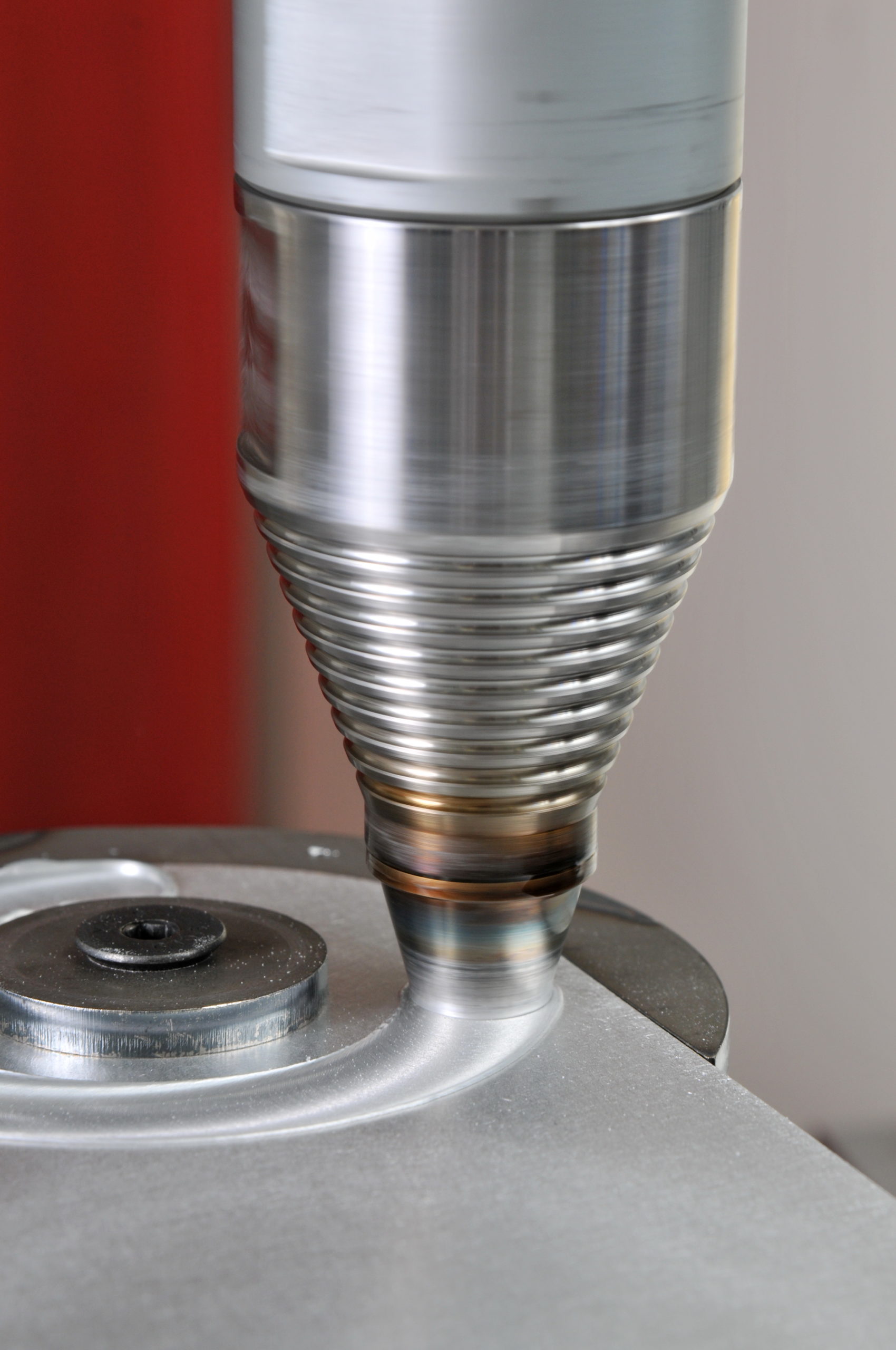
Traditional assembly in the aerospace industry
Until the 1950s, gas welding, particularly oxyacetylene, was widely used to assemble aeronautical structures. This process was suitable for thin materials, but was gradually replaced by arc welding, deemed more economical and efficient.
TIG welding (Tungsten Inert Gas) became the industry standard for joining metals such as magnesium and stainless steel. It remains a preferred method for aircraft repair and maintenance, thanks to its precision and versatility.
There are two other arc welding techniques: SMAW (Shielded Metal Arc Welding) and MIG (Gas Metal Arc Welding). SMAW is sometimes used for steel assemblies, while MIG is widely used for mass production.
However, these methods have their limitations when it comes to welding aluminum to other materials. Due to the specific properties of this metal, fusion welding often generates defects, making it necessary to adopt new solutions such as FSW.
The advantages of FSW in the aerospace industry and aluminum welding
FSW in the aerospace industry offers many advantages over traditional fusion welding methods, particularly for joining aluminum and its alloys:
- Compatibility with aluminum and alloys. Unlike arc welding, FSW enables aluminum to be joined without creating brittle intermetallic compounds. It therefore guarantees stronger joints for aeronautical structures;
- Saving time and money. FSW is fully automated and requires no filler metal. These factors considerably reduce manufacturing costs and increase process efficiency;
- Reducing aircraft weight. By eliminating the need for filler metal, FSW also makes aircraft structures lighter. It therefore improves aircraft fuel efficiency;
- Reduced deformation and residual stress. FSW operates in the solid state, avoiding melting and sudden cooling of materials. It limits distortion and internal stresses, guaranteeing longer-lasting, stable assemblies;
- Improved weld quality. The absence of fusion also reduces the risk of porosity, cracks or inclusions in welds. FSW ensures better joint homogeneity, essential for aeronautical safety;
- Compliance with environmental standards. Unlike fusion welding, FSW generates no harmful fumes, molten metal spatter or UV radiation. This makes it a safer and cleaner alternative for operators.
- Reduced maintenance requirements. Finally, thanks to its robustness and the quality of its assemblies, FSW reduces the need for maintenance and frequent inspections, optimizing aircraft profitability over the long term.
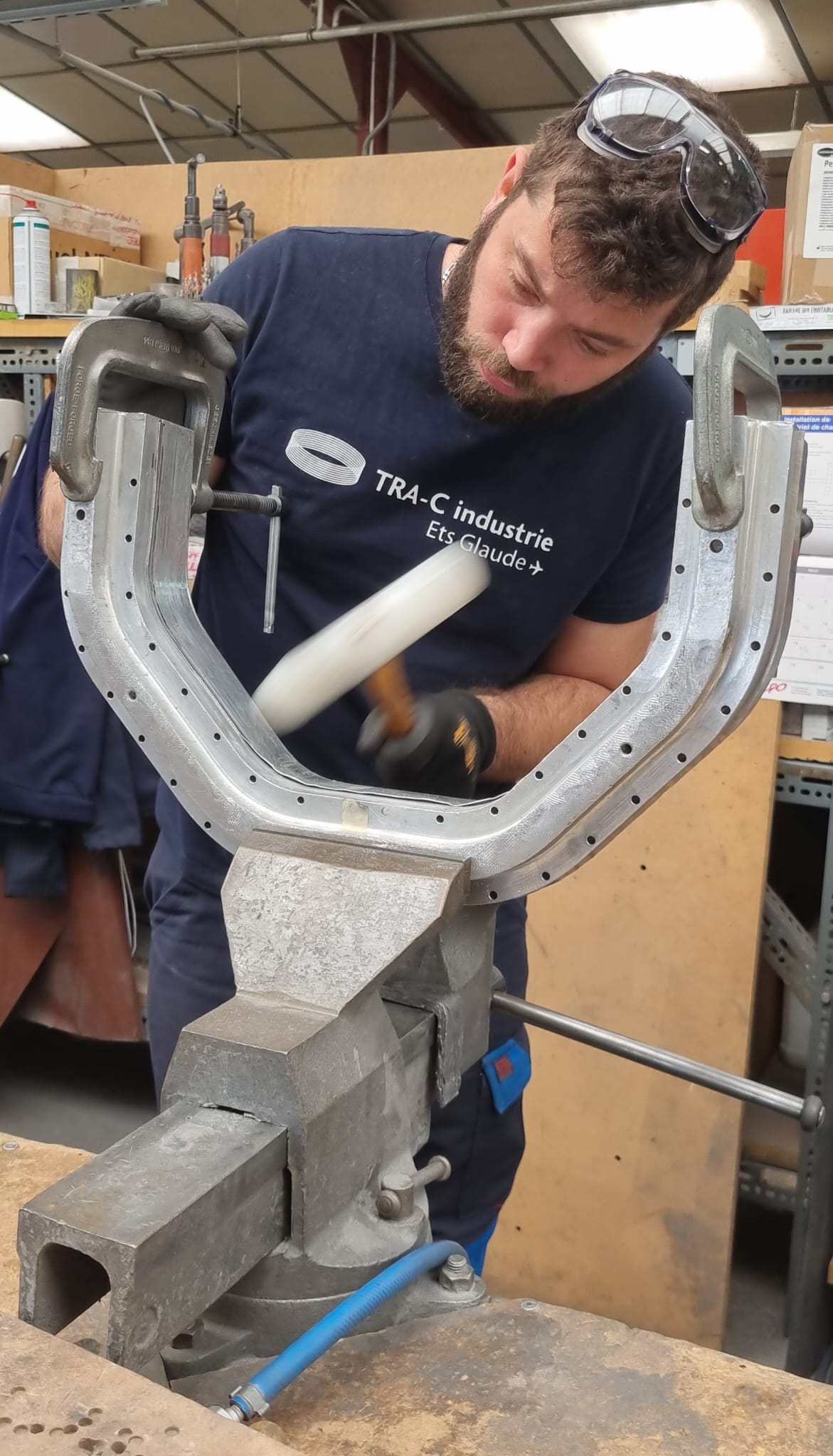
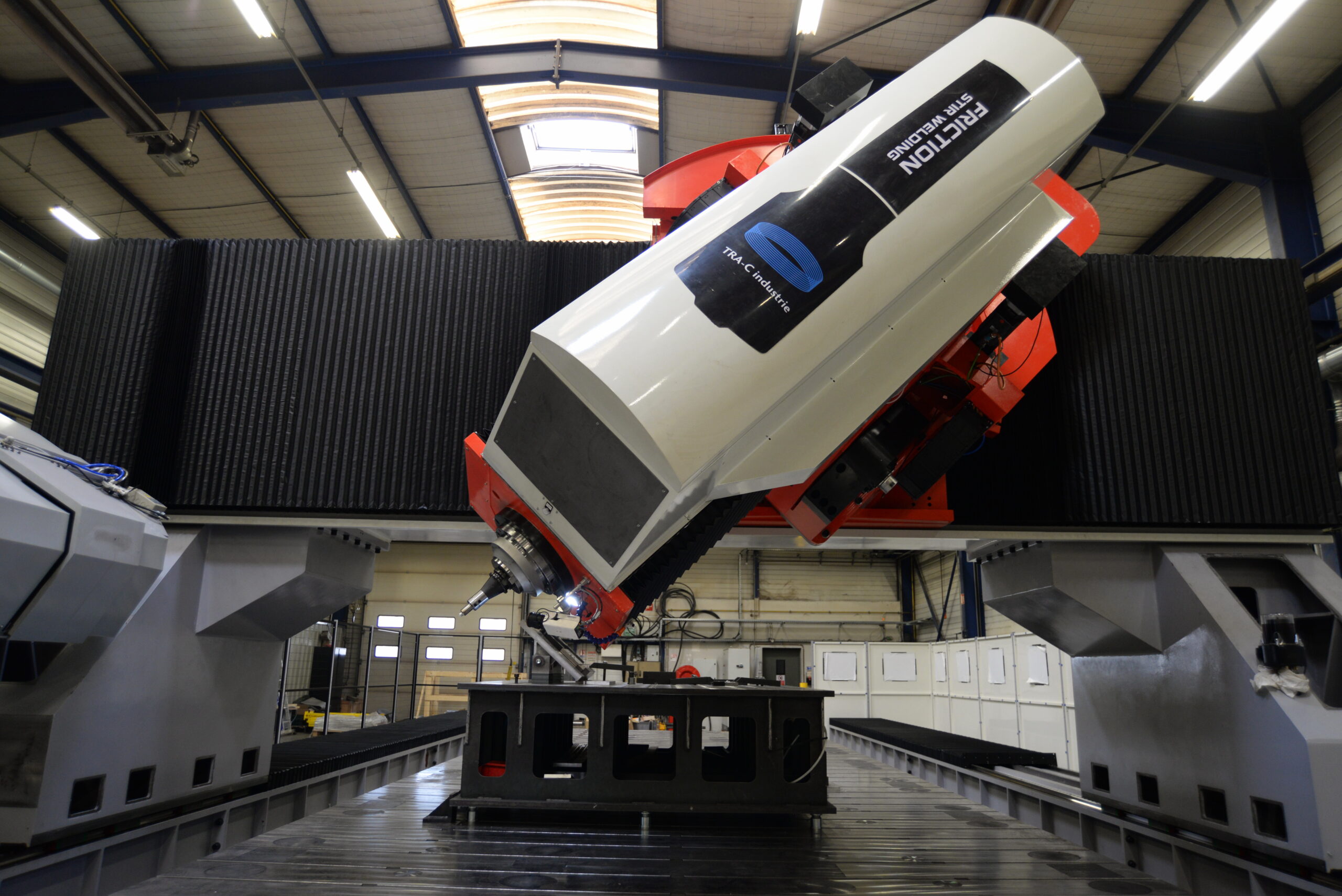
Some FSW applications in the aerospace industry
In the aeronautics industry, FSW is used to assemble aircraft fuselage panels and fuel tanks. Thanks to the strength and homogeneity of the welds obtained, it guarantees greater resistance to mechanical stress and pressure variations in flight.
This technique is also used for the manufacture of primary structures, such as stringers and reinforcement frames. By eliminating the need for rivets, FSW makes it possible to lighten components while maintaining their strength.
This technology is also used in the manufacture of heat exchangers and aircraft engine components. Thanks to its ability to produce strong, watertight joints, FSW contributes to optimizing performance and reducing maintenance costs for aeronautical structures.
Finally, in the space sector, FSW is used to weld cryogenic tanks for launchers and satellites. These assemblies have to withstand extreme temperatures and high stresses, which FSW enables them to achieve with precision and reliability.
Challenges and prospects for FSW in the aerospace industry
Despite its many advantages, FSW presents certain technical challenges, notably the need for high clamping force and tool wear. Optimizing tool materials and improving welding parameters are therefore essential to increase efficiency and durability.
The adoption of FSW in the aerospace industry is also hampered by the complexity of its automation for certain complex geometries. Advances in robotics and artificial intelligence will enable this technology to be better adapted to more varied structures and mass production.
Regarding the materials, research is focusing on extending FSW applications to denser alloys and hybrid materials. The development of new versions of the process, such as double-tool or high-speed FSW, could further enhance its performance.
In the future, FSW will play a key role in the manufacture of next-generation aircraft and space structures. Its growing integration into metal 3D printing and automated assembly will open up new prospects for the production of lighter, stronger and more environmentally-friendly aircraft!
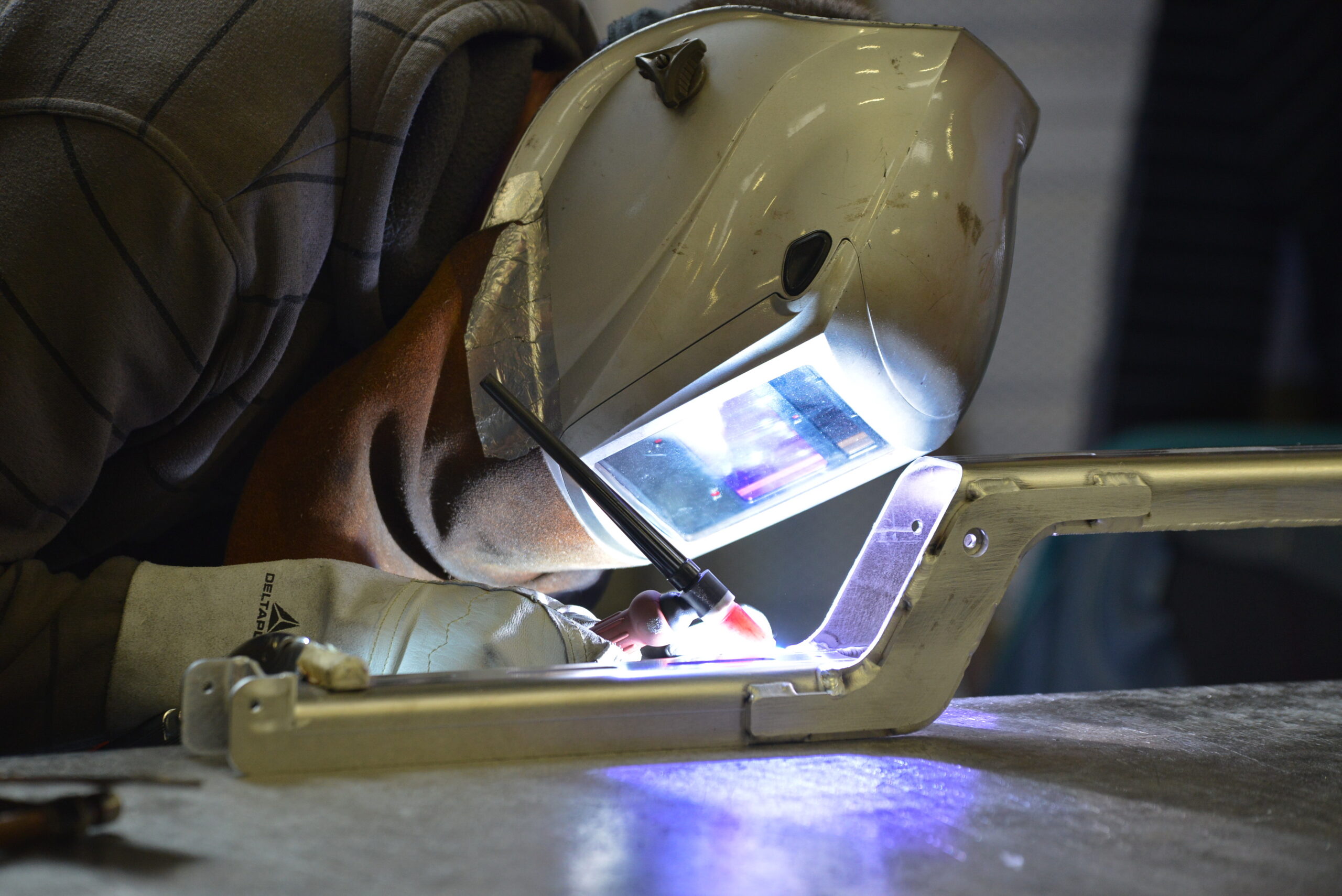
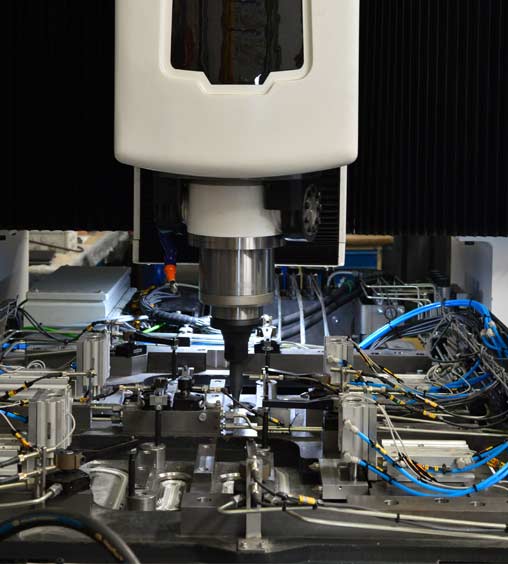
Calling on an FSW expert in the aerospace industry
TRA-C industrie is one of Europe’s leading companies in the field of friction stir welding (FSW). We offer tailor-made solutions for aerospace engineering, guaranteeing high-quality assemblies adapted to the sector’s requirements.
Since 2009, we have been perfecting our FSW process to optimize weld robustness and precision. Thanks to continuous improvements, our approach enables us to efficiently join key materials such as aluminum and its alloys.
Innovation is also at the heart of our methods, particularly when it comes to welding heterogeneous metals. The integration of robotics and automation in our processes ensures highly reliable welds, essential for the manufacture of aeronautical structures.
Our know-how in FSW in the aerospace industry enables us to improve the durability, reproducibility and efficiency of assemblies. We also collaborate with renowned suppliers such as Constellium and Hurco, enabling us to meet the growing needs of the sector.