What is friction stir welding (FSW)?
Friction stir welding (FSW) is a solid-state welding process that uses the heat generated by friction between a rotating tool and the materials to be joined. This process creates solid joints without melting the materials, offering an effective alternative to traditional methods.
One of the main advantages of FSW is its ability to weld materials that are difficult to join using other techniques, such as aluminum or copper alloys. It also generates less distortion and stress, guaranteeing high-quality welds.
Nowadays, this process is widely used in various industrial sectors, such as aeronautics, automotive, shipbuilding and even renewable energies. FSW meets the technical requirements of modern applications, while reducing costs and environmental impact.
But how does FSW welding work in practice? What are its advantages and drawbacks? What are its practical applications? And what are the advances in this technology? In this article, TRA-C industrie tells you more about this revolutionary process…
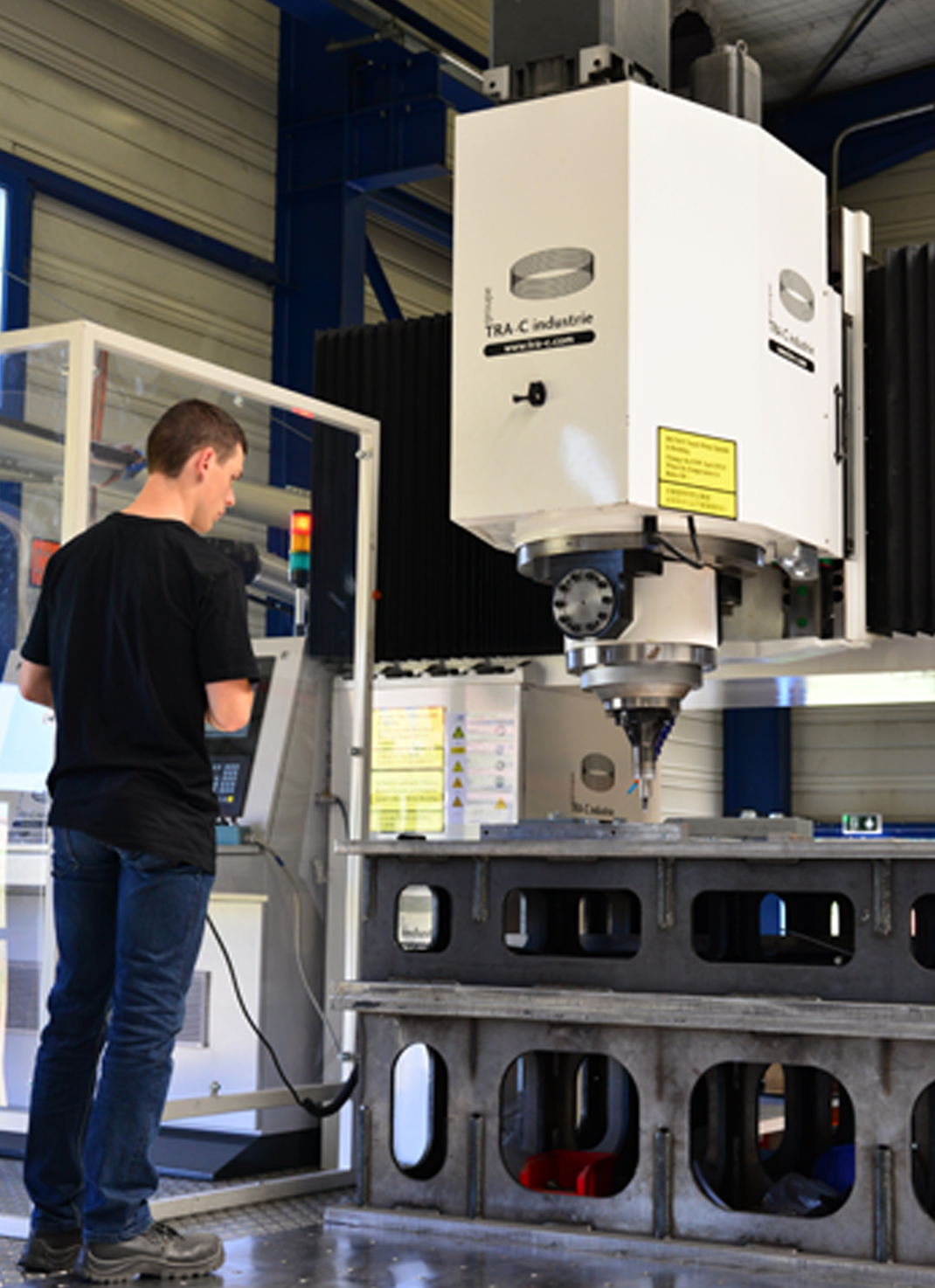

Friction stir welding operating principle
Friction stir welding is based on the use of a rotating cylindrical tool fitted with a tip that penetrates the parts to be joined. As the tool rotates at high speed, it generates frictional heat, locally softening the material without melting it.
Once the material has softened, the tool moves along the joint to be welded, resulting in plastic mixing of the materials of the two metal parts. This mechanical mixing creates a solid, homogeneous bond between the surfaces in contact.
During the operation, a driving force is exerted on the tool to maintain sufficient pressure and ensure a continuous weld. This precise control of the process prevents the formation of cracks or porosities in the assembly.
Finally, the tool retracts after traversing the entire lineweld, leaving behind a compact, resistant weld bead. Once cooled, the assembly keep high mechanical properties, close to those of the original material.
What are the main components of an FSW tool?
The friction stir welding tool plays a key role in the success of the assembly. Its various components have a direct influence on the quality of the welded joint, and require the use of materials capable of withstanding high temperatures and mechanical stress:
- The shoulder: this is the wide part of the tool in contact with the surface of the workpieces, generating heat by friction. It also contains the softened material;
- The tip (or pin): this element penetrates the material, allowing the surfaces to be welded to be mixed. Its geometry influences the quality of assembly and stirring;
- The tool body: this connects the tool to the machine and transmits the forces exerted. It must withstand the high mechanical stresses encountered during operation.
FSW tools are manufactured using ultra-high-strength materials such as hardened steel or tungsten carbide. These materials withstand high temperatures and wear caused by friction with the parts to be welded.

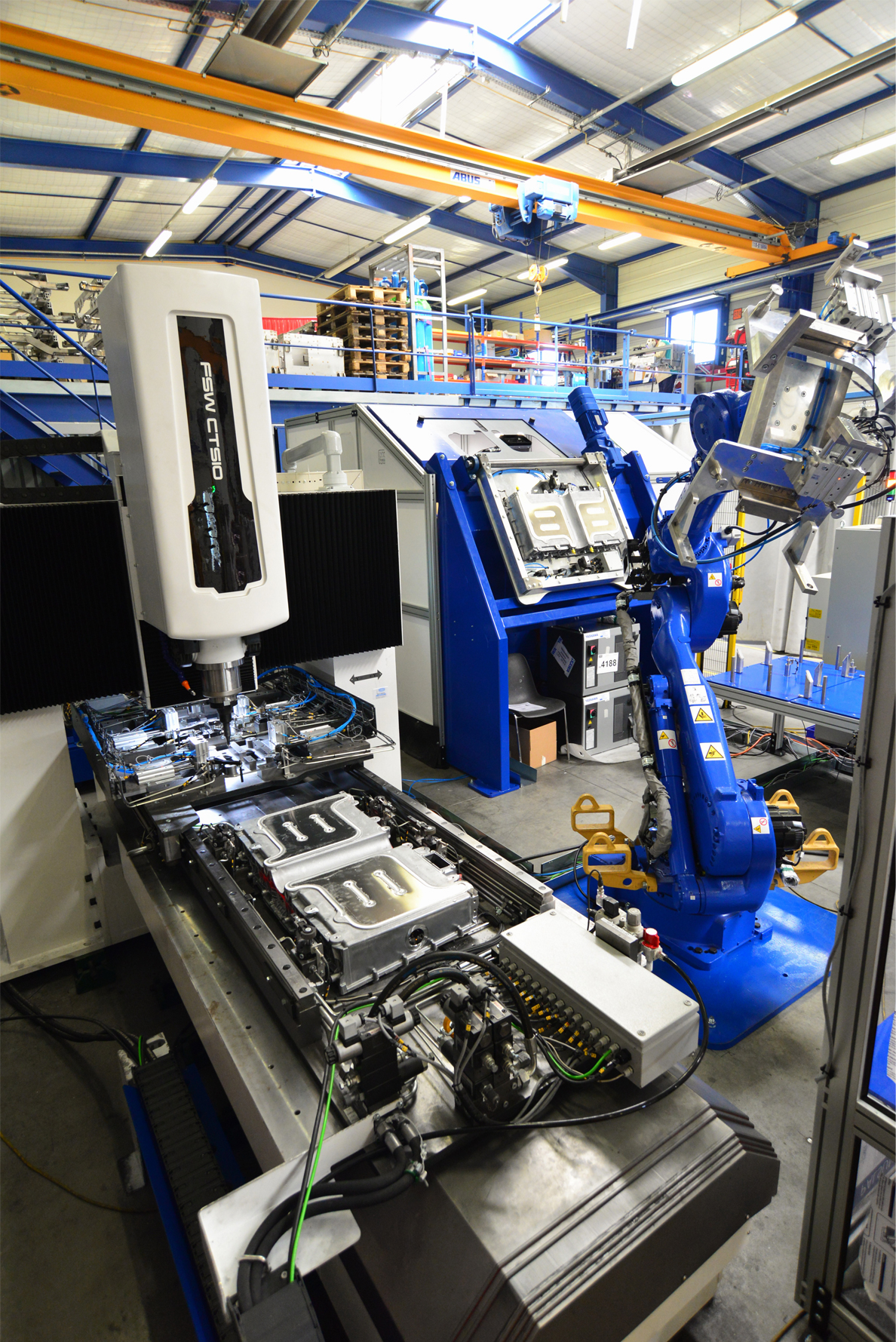
Advantages of friction stir welding
Friction stir welding offers many advantages over traditional fusion welding methods. The main benefits of this process include :
- High welding quality: the resulting joint is homogeneous, limiting cracks and porosities. Mechanical strength is therefore improved compared with conventional welding processes;
- No melting: the material remains in a solid state, reducing the risk of deformation. The initial structure of the material is thus better preserved;
- Reduced energy consumption: less heat is required compared to melting techniques. FSW thus optimizes the energy efficiency of the process;
- Limited environmental impact: FSW generates no filler metal, protective gas or toxic fumes. The process is therefore cleaner and safer for operators;
- Compatibility with complex materials: light metals that are difficult to weld, such as aluminum, are joined with reliability. Weld quality remains consistent, even on sensitive materials;
- Optimized operating costs: Finally, reduced wear on the tools extends their service life. The absence of metal or other consumables also reduces overall production costs.
Drawbacks of the FSW welding process
Although friction stir welding offers many advantages, this technology also has certain limitations. These mainly concern technical constraints, materials and equipment costs:
- Application limited to ductile materials: materials that are too hard or brittle, such as certain steels, are difficult to weld. Their behavior under friction can lead to defects or fractures;
- Use of specific equipment: adapted machines, more robust than conventional welders, are also required for FSW. This implies a high initial investment for manufacturers;
- Exit hole: finally, at the end of the welding process, a small hole may appear where the tool withdraws. However, specialists such as TRA-C industrie design the part in order to place this hole in a stress-free area, thus ensuring a watertight seal.

Which industries can benefit from welding friction stir ?
Shipbuilding and offshore
Friction stir welding is widely used in shipbuilding and offshore. This process is used to manufacture a wide range of components, such as deck panels and helicopter landing platforms…
The construction of entire ships, from stern to bow, also incorporates FSW. In particular, this process lightens the armor of amphibious assault ships by eliminating the need for rivets, nuts or traditional welds.
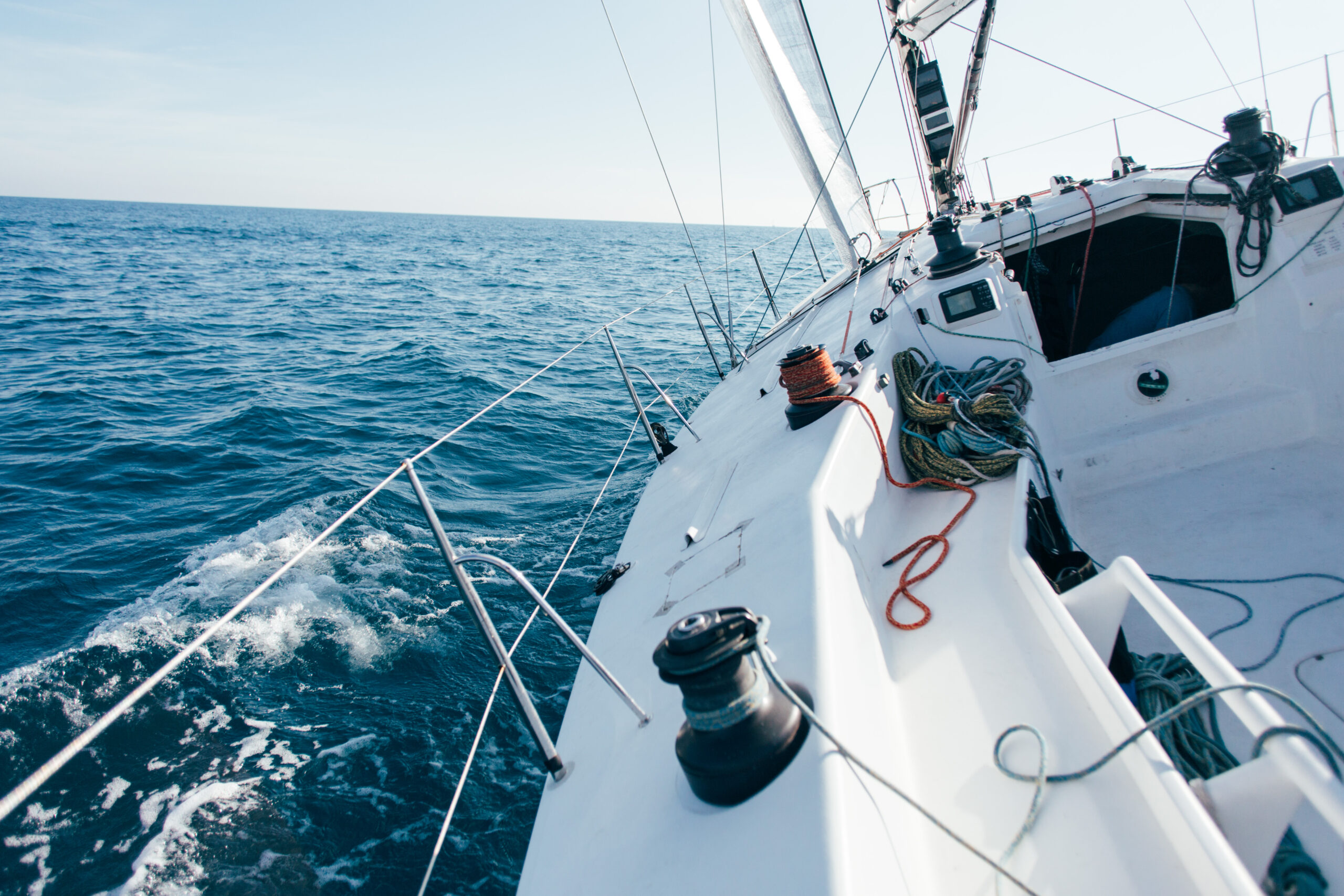
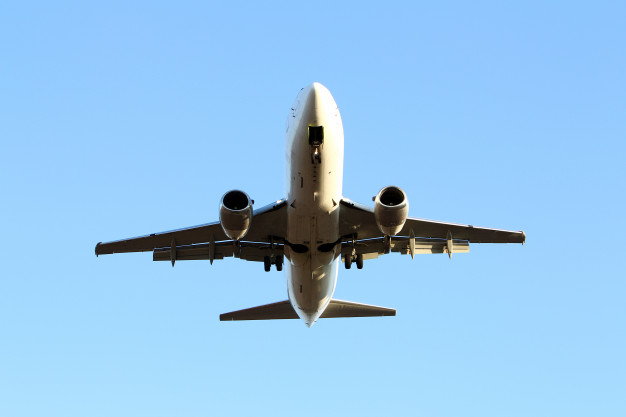
Aerospace industry
The aerospace industry also uses FSW to assemble various critical components. Numerous expendable launch vehicles, including rockets and booms, incorporate this process, notably in NASA tests.
The aerospace industry favors FSW to simplify the welding of aluminum alloys, which are often complex to assemble using traditional methods. It also facilitates the joining of alloys with different properties, providing a solution to a major challenge!
The automotive industry
FSW can also be used to design automotive parts such as battery, traysheat exchangers, cold plates and so on. Many companies use it successfully to manufacture a wide range of components
This method also facilitates the assembly of aluminum sheets to supports for components such as doors, trunks or hoods. Carmakers prefer FSW for its stability, reduced wear and improved fuel efficiency.
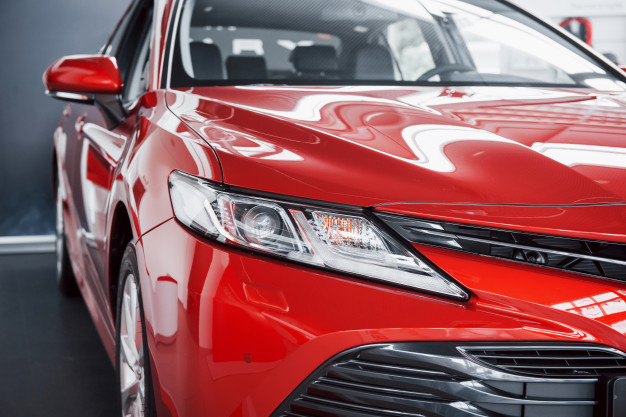

Railway sector
Friction stir welding is also used in the rail industry, notably to manufacture roof and side panels for trains. Friction stir welding is also used to fasten floor panels in double-decker wagons, ensuring high strength.
This process is an excellent choice for cooling high-power electronic locomotives, thanks to its heat transfer efficiency. The rail industry also favors FSW for its safety benefits!
Manufacturing industry
The FSW process is commonly used in this industry to manufacture components such as faceplate panels and cathode ray tubes.
The process can also be applied in specialized fields, such as confining nuclear waste in thick copper drums.
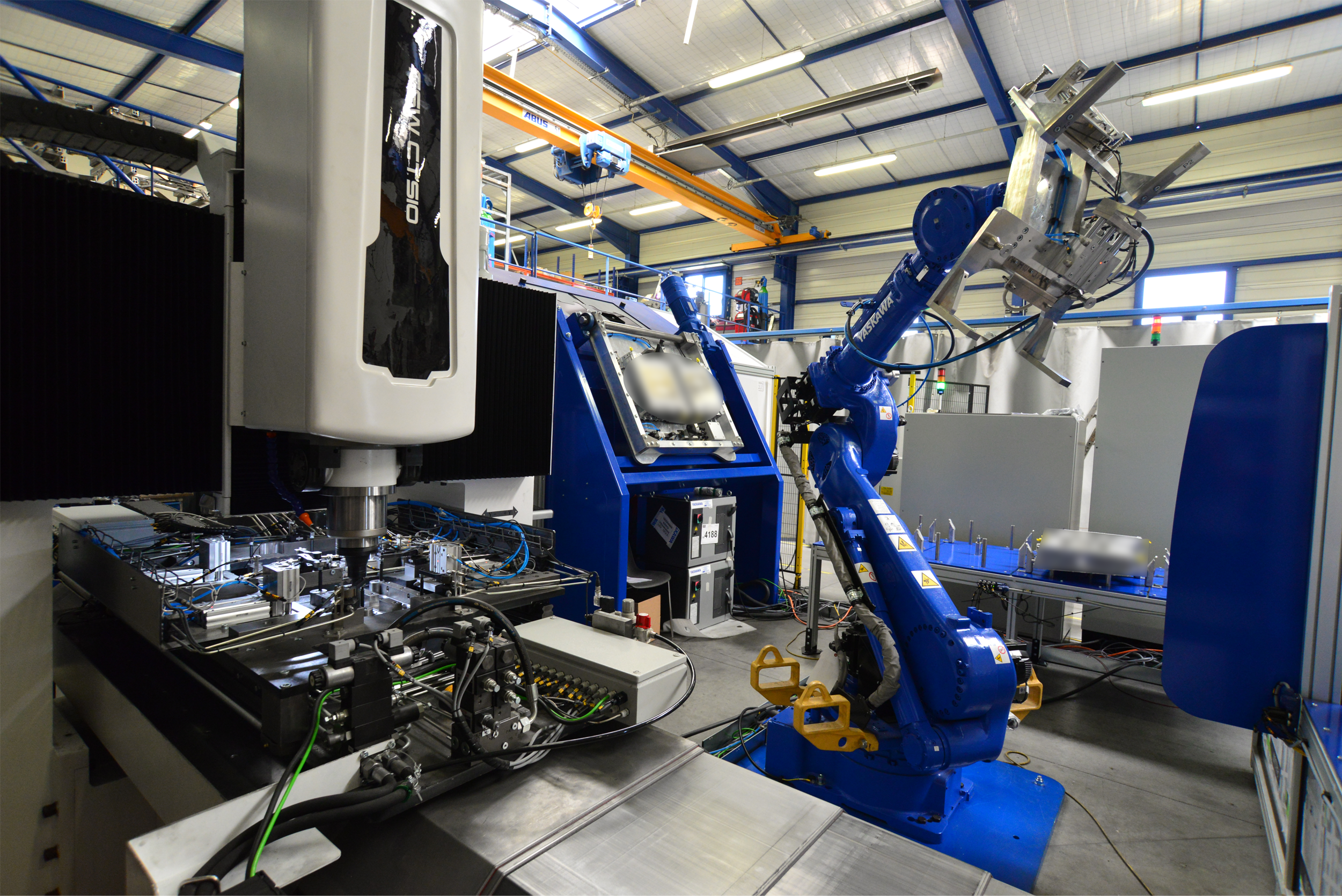

Robotics
Finally, friction stir welding is use for emerging applications in robotics, although its use still depends on advances in other technologies. For the time being, its adoption remains limited, but its potential is considerable.
In particular, it is used to manufacture complex, lightweight parts. Although largely untapped at present, this process could transform the robotics industry as it continues to develop and diversify…
TRA-C industrie, European leader in friction stir welding
As a major player in the field of friction stir welding in Europe, TRA-C industrie is recognized for its expertise and cutting-edge technologies. We offer innovative solutions for a wide range of industrial applications!
Thanks to close collaboration with renowned partners such as UIMM, we continue to strengthen our leading position in the FSW sector. This strategic alliance enables us to pool our know-how and drive innovation in this field.
Through our design office, we constantly invest in research and development to stay at the cutting edge of technology. Our aim is to offer solutions adapted to the specific needs of each customer.
With solid expertise and a network of reliable partners, TRA-C industrie continues its expansion and commitment to providing excellent friction stir welding solutions to tomorrow’s industries.
