Automated Welding in the Automotive Industry
Automated welding using robotics is a cornerstone of modern industrial manufacturing processes. Welding robots tackle to welding process in many industries, not least in vehicle production. Advanced robotics allow manufacturers to automate the welding process, which eliminates the need for human labour when producing cars in nearly all plants globally.
Kinds of Robotic Welding
Various automated welding techniques are used for robotic welding in automotive manufacturing. Six main processes require a specialised robot and provide unique functionality in vehicle production.
Firstly, resistance spot welding is a commonly automated process in the automotive industry. This relies on heat generation from electrical resistance and pressure. Heat and pressure are applied to the metal components that are to be joined. This concentrated pressure and electric resistance cause the metals to melt and mix at the point of contact. Once cooled, the point where the metals coalesce develops into a permanent bond.
This seamless process doesn’t leave any marks that the welding took place and is very strong relative to other welding techniques. Therefore, the automotive industry relies heavily on spot welding, which has become more efficient and cost-effective using welding robots.
Laser welding is another process that is commonly automated in car manufacturing. As the name suggests, this technique involves focusing high-powered laser beams at the desired joining point. The intense heat produced from the laser will melt the materials, promoting mixing and a robust weld once it has cooled. This precise technique is consistent and rapid, making it invaluable in the mass-manufacture of automotives.


Arc welding is also widely used in this industry. This process uses the heat generated from an electrical arc between an electrode and the material to be welded. This process requires shielding gas that is typically inert to facilitate the travel of the arc. The material at the join is melted and will then permanently join after cooling down. Metal inert gas welding (MIG) robots and metal active gas welding (MAG) robots are staples of the automotive industry.
The next automated welding technique in the industry is gas tungsten arc welding. This is another form of arc welding, so it also relies on electricity passing between an electrode and the components. Much like the previous technique, a shielding gas is also used to protect the weld area. The main difference here is that the electrode is made out of tungsten, which has the highest melting temperature of any metal.
Thin gauge arc welding is another type of arc welding. This technique is predominantly used with thinner components that need a more delicate approach. Welding thin metal sheets is challenging, as arc welding can cause deformation and property changes that are more apparent in thinner materials. This approach is a more refined technique that prevents the weld from collapsing or distorting the constituent metals.
Finally, plasma welding is another arc welding technique similar to thin gauge arc welding in many ways. The primary difference between the two is that the plasma arc can be separated from the gas shield. The plasma can be pushed through a nozzle, creating a more focused arc, allowing manufacturers to weld metals as thin as 0.1mm.

Advantages of Robotic Welding
Using robots to automate the welding process in automotive manufacturing can significantly boost the efficiency and productivity in plants. These robots are highly specialised and precise, resulting in fewer errors and higher consistency when performing repetitive tasks.
Additionally, using such robots allows car manufacturers to utilise their floor space more effectively. These machines create more floor space in factories as fewer humans are required in the facility. More space means more room for movement and more space for equipment, which can boost overall productivity.
On top of this, robotic welding machines tend to increase safety in the manufacturing process. This is because, unlike humans, they do not lose focus when performing repetitive tasks. Accidents are predominantly caused by lapses in concentration so automated factories tend to be safer.
Finally, using robotics in the automotive manufacturing process helps to cut down on the waste produced in the industry. The higher level of accuracy that robots provide and their efficiency means that little debris is discarded in the process. Human error is one of the leading contributors to waste from factories, so using robots helps to reduce this significantly.
Disadvantages of Robotic Welding
Despite the many advantages of these automated systems, there are drawbacks nonetheless. For example, integrating robotic welding solutions into the manufacturing process is an expensive endeavour. These are intricate and technologically advanced tools, so they tend to cost a lot to produce in the first place.
Additionally, these robots will need to be supervised by human workers. This means that human employees will require specialised training before integrating robotic welding into the manufacturing process. This can be expensive and time-consuming.
Additionally, robots have a substantially limited scope for flexibility compared to their human counterparts. A human employee can easily be trained to undertake multiple roles in the manufacturing process. On the other hand, robots are highly specialised for a certain task, so a robot can’t switch roles unless programmed to do so.
This highlights another downside of automated labour: these machines cannot make decisions. Despite their sophisticated programming, robots rely on a set of instructions to perform their roles in the manufacturing process. This means they cannot make decisions on the fly or react to abnormal circumstances in the way humans can.

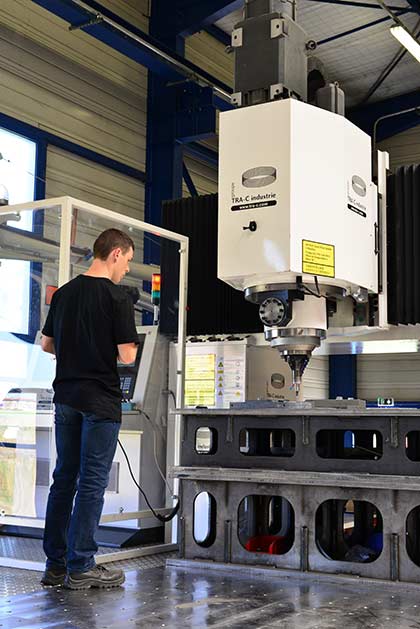
TRA-C and Automated Welding
TRA-C is one of the leading manufacturers of user-friendly robotic welding machines in Europe. The company manufactures such automated welding machines to enhance efficiency and return on investment for many companies across various industries.
These machines are widely deployed in automotive manufacturing. One of the primary approaches taken by TRA-C is to place training and integration at the centre of their rollout process. This negates some of the more significant downsides of automated manufacturing, as employees can be trained in-house to supervise and maintain the robotic welding machines used in factories.
On the whole, robotic welding has become standard practice in the automotive industry over the past decades. This is even more apparent today, with many companies opting for fully automated production lines in their factories.