Automated welding for more efficient production
The automation of production processes allows repetitive tasks to be performed as many times as necessary with consistent quality in the same amount of time. This allows quality to be maintained at a high level while reducing unit costs. The purchase of an automated welding system therefore pays for itself in a very short time, which makes automated welding attractive for large and medium-sized companies, as it increases the efficiency of the entire welding process.
What is automated welding?
An automated welding process allows the welding process to be repeated in a production site as often and continuously as necessary. Automatic welding machines or welding robots can be used for this purpose. Types of automated welding include automatic fusion welding, automatic pressure welding, and automatic brazing/soldering.
Automatic fusion welding is particularly used in the automotive industry. Possible welding processes are arc welding (MAG, TIG, MIG, plasma) and laser welding. Automatic pressure welding is also used in the automotive industry. In addition, it is also used for tanks or pipes that require high tightness. This process is also used in the construction of trains or in aeronautics. The welding processes used here are resistance spot welding, continuous welding and friction stir welding (FSW).
Automatic soldering/brazing is used for electronic boards or electrical components. It is also used for the manufacture of small parts for motorcycles and cars, valves or cooling pipes. The most common processes are electron beam brazing and furnace brazing.
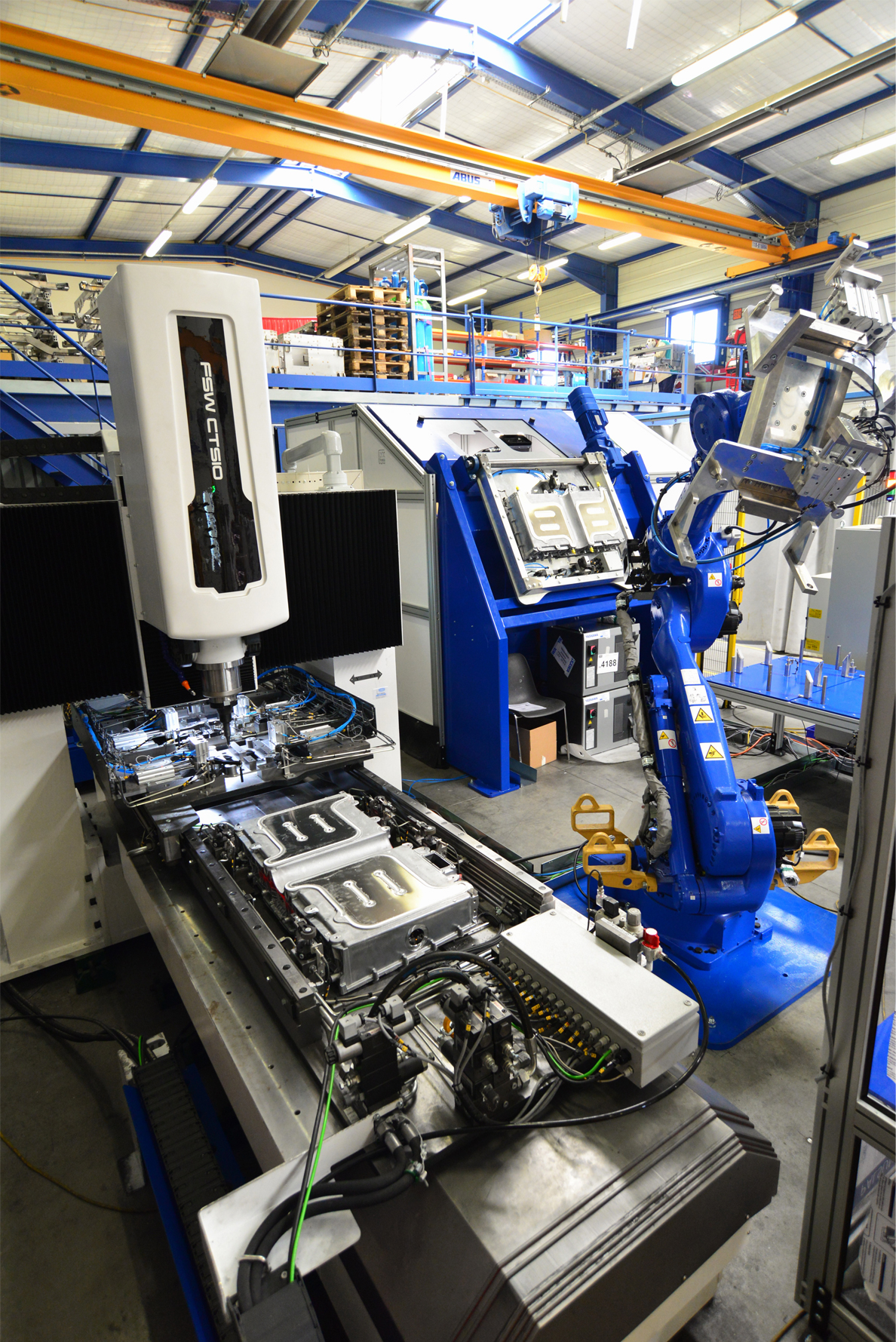
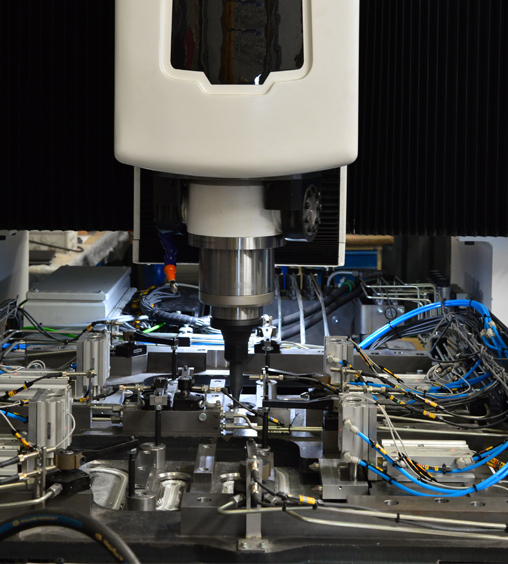
What are the advantages of automated welding?
Automated welding allows us to produce as many parts as we want while maintaining a constant quality. The unit costs are thus reduced, which means that the purchase of an automated welding system can be quickly amortized. The high quality guaranteed by the automation reduces the number of necessary reworkings. While production costs decrease, production times are shorter.
Once set up, the processes can be repeated as many times as necessary with consistent quality. The greater the production, the greater the time savings. When calculating time savings, the entire process, from receipt of the order to delivery of the parts to the customer, must be taken into account. Once an order is received, the production systems are integrated into the process chain. The downtime of a machine can thus be reduced. Automated welding is profitable from a series of ten parts. The more complex and time-consuming the welding job, the lower the number of parts at which the automated process is profitable.
What are the welding techniques and machines used by TRA-C Industrie?
TRA-C Industrie is specialized in automated welding and robotized welding. The company has all the human and material resources to design, manufacture and install on site industrial robots according to customers’ requirements. Our mobile teams take care of the installation and deployment of the solution on the customers’ production sites. We provide training for your employees as well as maintenance of the equipment.
An industrial robot can automate entire processes while eliminating repetitive and dangerous tasks for workers. It thus contributes to improving safety and working conditions in a company. In addition, it makes tedious tasks easier for employees.
TRA-C Industrie develops tailor-made machines according to the customers’ requirements. Our engineers develop, design and program each machine on our premises. As an internationally recognized manufacturer of special machines, we take care of the installation of our solutions on site. We offer our customers a complete training on the use of their new machine. They learn to use it and we accompany them in the first phase, when a new production is launched.
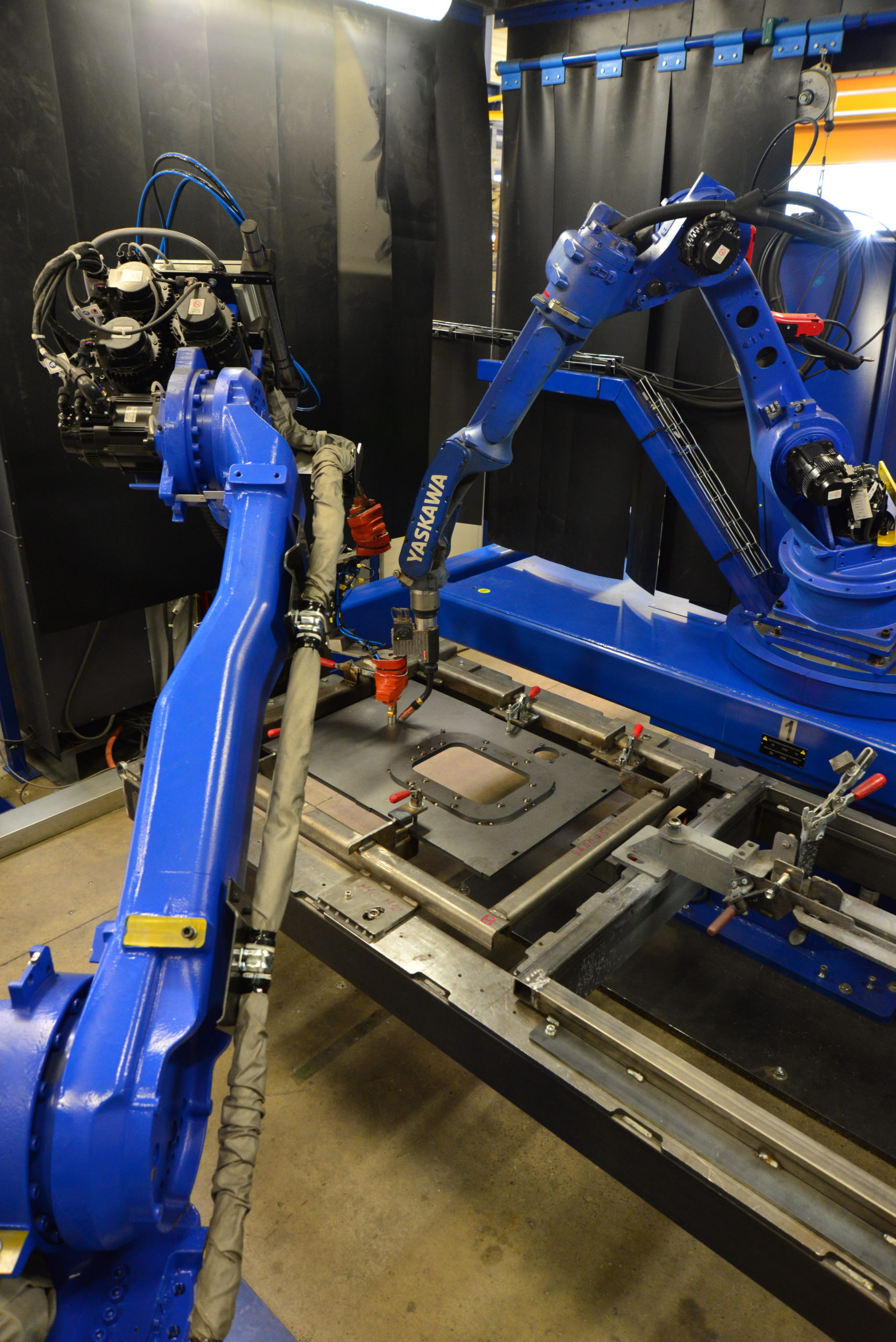
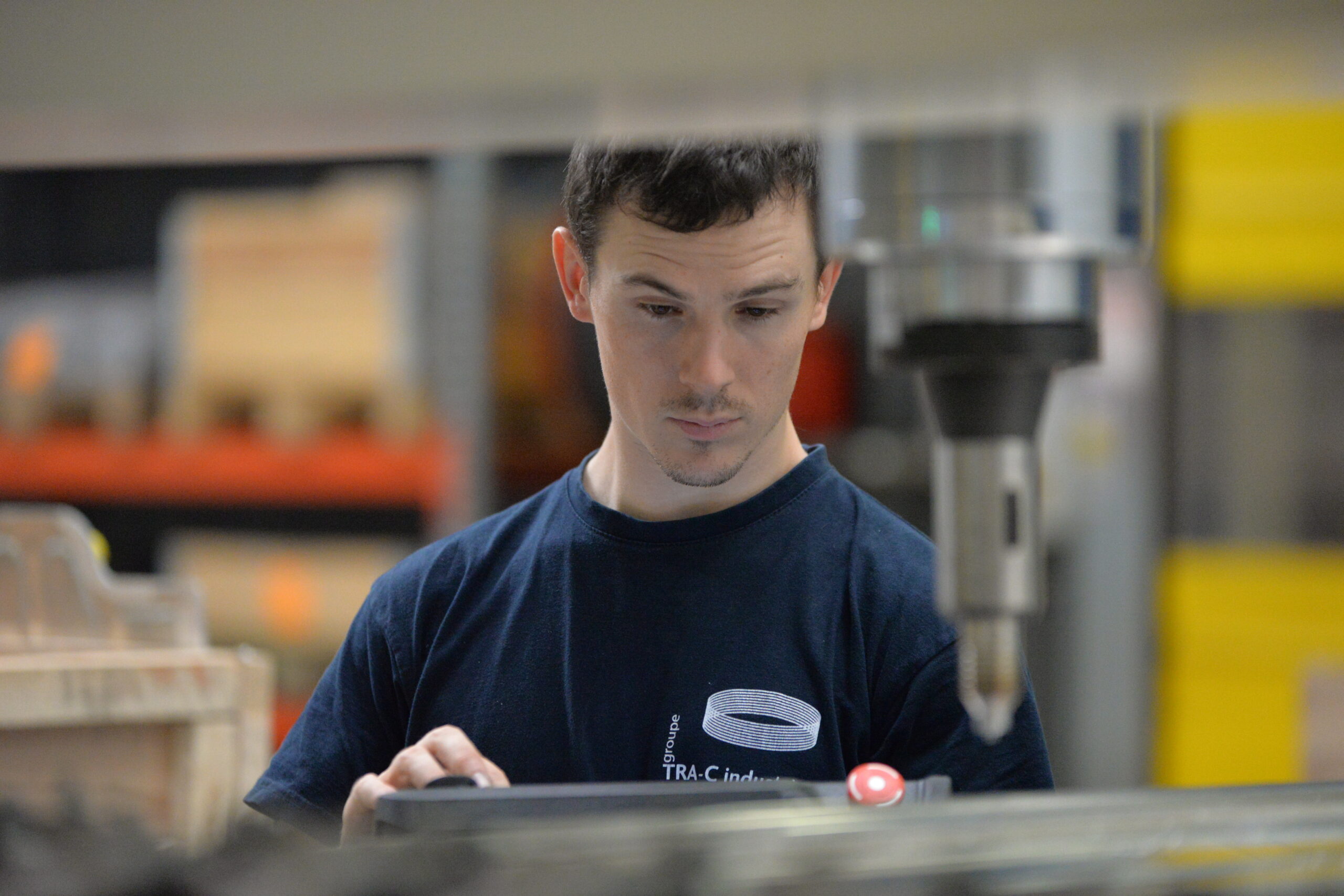
Welding specialist for FSW
The Lyon-based industrial robotics company TRA-C Industrie collaborates with partners from different sectors. Our teams design and develop industrial robot systems as well as complete welding systems for FSW. In the field of FSW, we are the European market leader.
We work with the latest technologies to realize your large projects. If you wish to develop and install robotized equipment to improve and optimize your manufacturing process and your competitiveness, TRA-C Industrie puts its experience and skills at your service.
Design and manufacture of welding equipment
Each welding procedure is unique. Therefore, there can be no standard solution for automated welding equipment. On the contrary, it must be tailored to the customer’s requirements. TRA-C Industrie has all the necessary skills to design and manufacture welding equipment according to customers’ requirements. Our teams of engineers and technicians study and design customized solutions for our partners in various sectors.
Our design office studies your request and verifies its feasibility. We then define the machine, its functions and tools, so that it is perfectly adapted to your needs and production conditions. Our offer of specific automated welding systems can be supplemented by other elements, for example in the areas of control or handling.
Once an automated welding system has been designed according to your requirements, our teams of mobile technicians take care of the installation and configuration of the system on your premises. We take care of the implementation, commissioning, and training of your employees in the use and maintenance of the system.
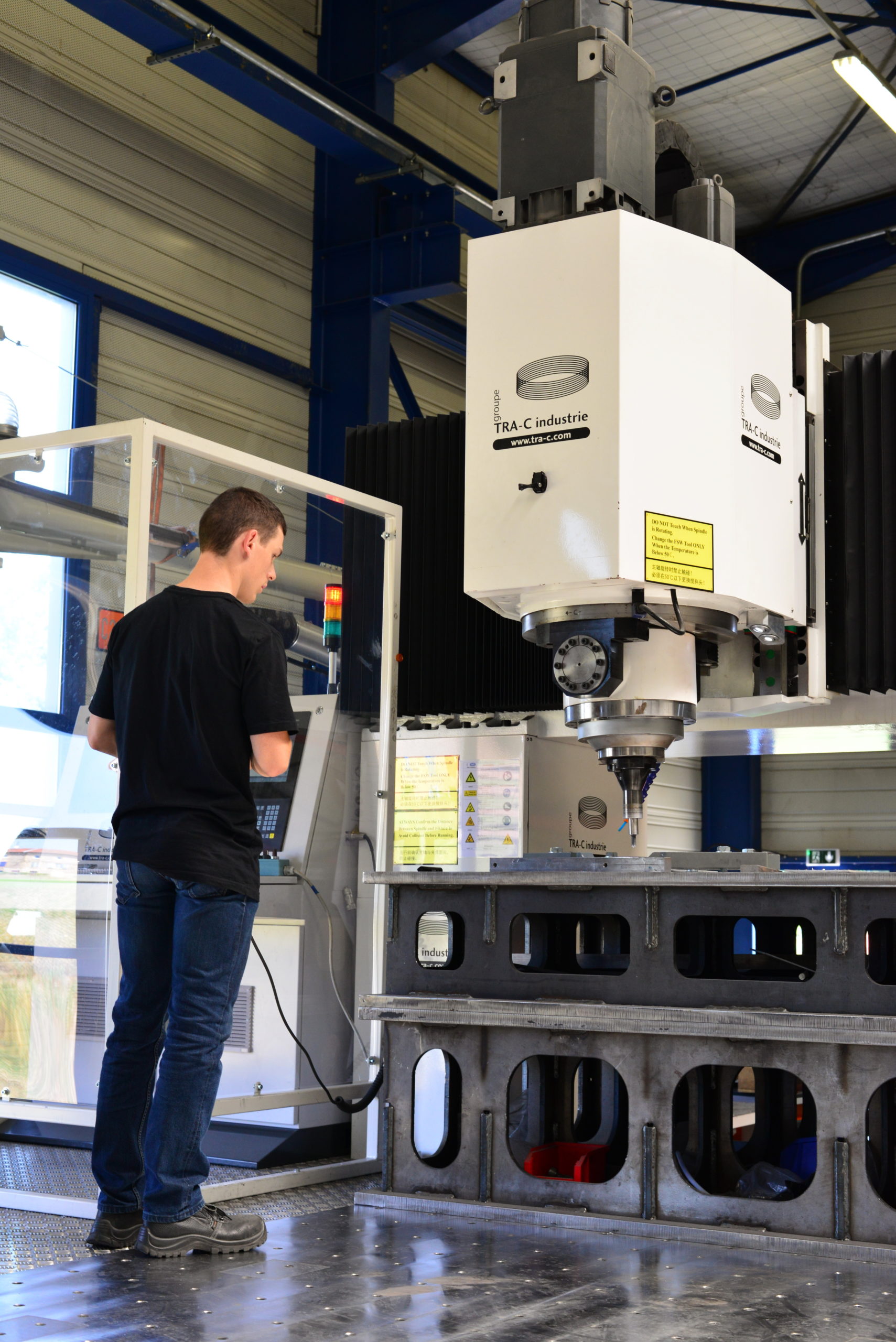