Friction welding is a thermal joining process based on friction between two metal parts. Thanks to the heat generated by this movement, the materials reach a plastic state, enabling them to fuse without the addition of filler metal.
Unlike conventional welding methods, it requires neither an electric arc nor a shielding gas. This limits defects caused by impurities and reduces thermal stress on materials. This makes it a popular technique for applications requiring high strength.
Used in the aerospace, automotive and energy industries, this process enables similar or dissimilar metals to be joined. Friction welding also guarantees strong joints with minimal distortion, meeting the requirements of cutting-edge sectors.
But how does this process work in practice? What are the different types of friction welding? How does it differ from traditional methods? Principle, benefits, applications… In this article, TRA-C industrie tells you more about this innovative process!
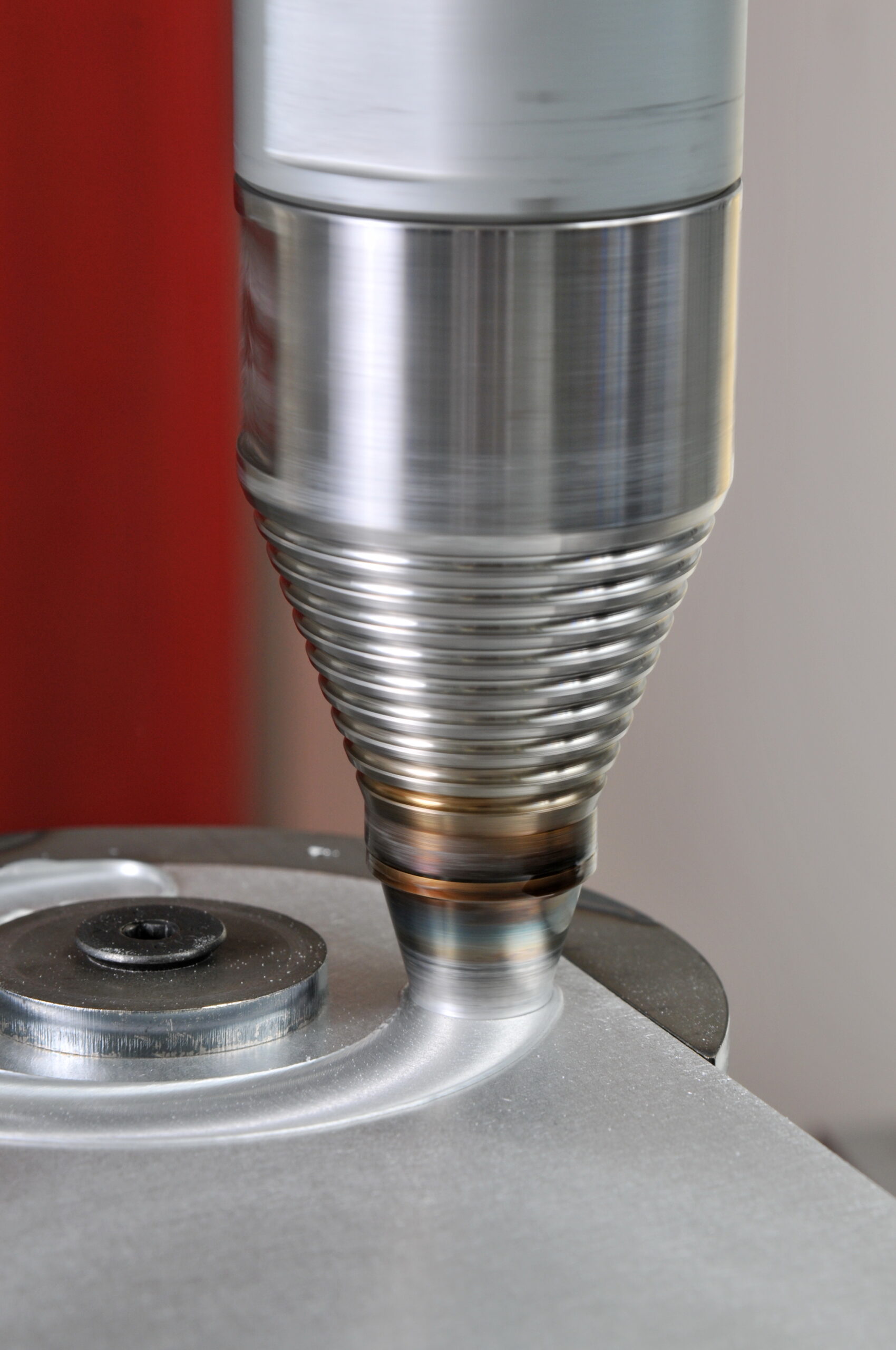
What does this process actually involve?
When two materials rub against each other, they release thermal energy through friction. The higher the speed and pressure of this friction, the greater the amount of energy produced, thus promoting heating of the parts.
Friction welding uses this principle, where it subjects the components to be joined to intense friction. At extremely high speeds and pressures, it creates mechanical friction between the parts, generating the heat needed to fuse them together.
The thermal energy released causes localized softening of the materials at the point of contact. This temperature rise makes the surfaces viscous, allowing the metals to interpenetrate without the need for a filler metal!
Once friction has stopped, pressure is maintained to consolidate the joint. Controlled cooling then creates a solid, homogeneous joint, ensuring optimum mechanical resistance to external stresses.
Friction welding techniques
Friction welding includes a number of techniques that exploit friction to join materials without external input. The purpose of these methods is the same, but the approaches to making welds between metals are slightly different…
Rotary friction welding
Rotary friction welding involves rotating one material against the other, precisely at the joint. Thanks to high speed and strong axial pressure, the heat generated softens the surfaces in contact.
Under this thermal effect, the metals become plastic and interpenetrate at the point of contact. Once rotation has stopped, pressure is maintained to ensure homogeneous, solid assembly of the components.

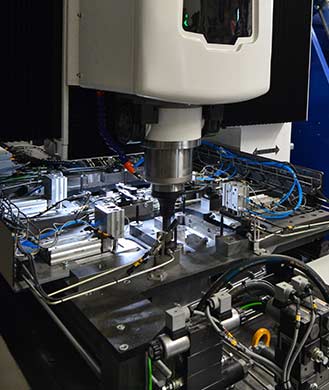
Linear friction welding
Linear friction welding uses rapid back-and-forth movement of one component against the other. This intense friction, combined with high compressive forces, generates sufficient heat to soften the contact surfaces.
Under this thermal effect, the materials plastically deform and mix at the point of contact. This process creates a strong, homogeneous bond between the parts, guaranteeing a resistant, durable weld.
Friction stir welding
Friction stir welding relies on the use of a cylindrical pin to generate frictional heat between the materials to be joined. This process heats the parts at their point of contact, making them plastic and facilitating their fusion.
This rotating tool moves along the weld line, kneading the plasticized materials to mix them homogeneously. This agitation creates a solid bond between the components without the use of filler metal…
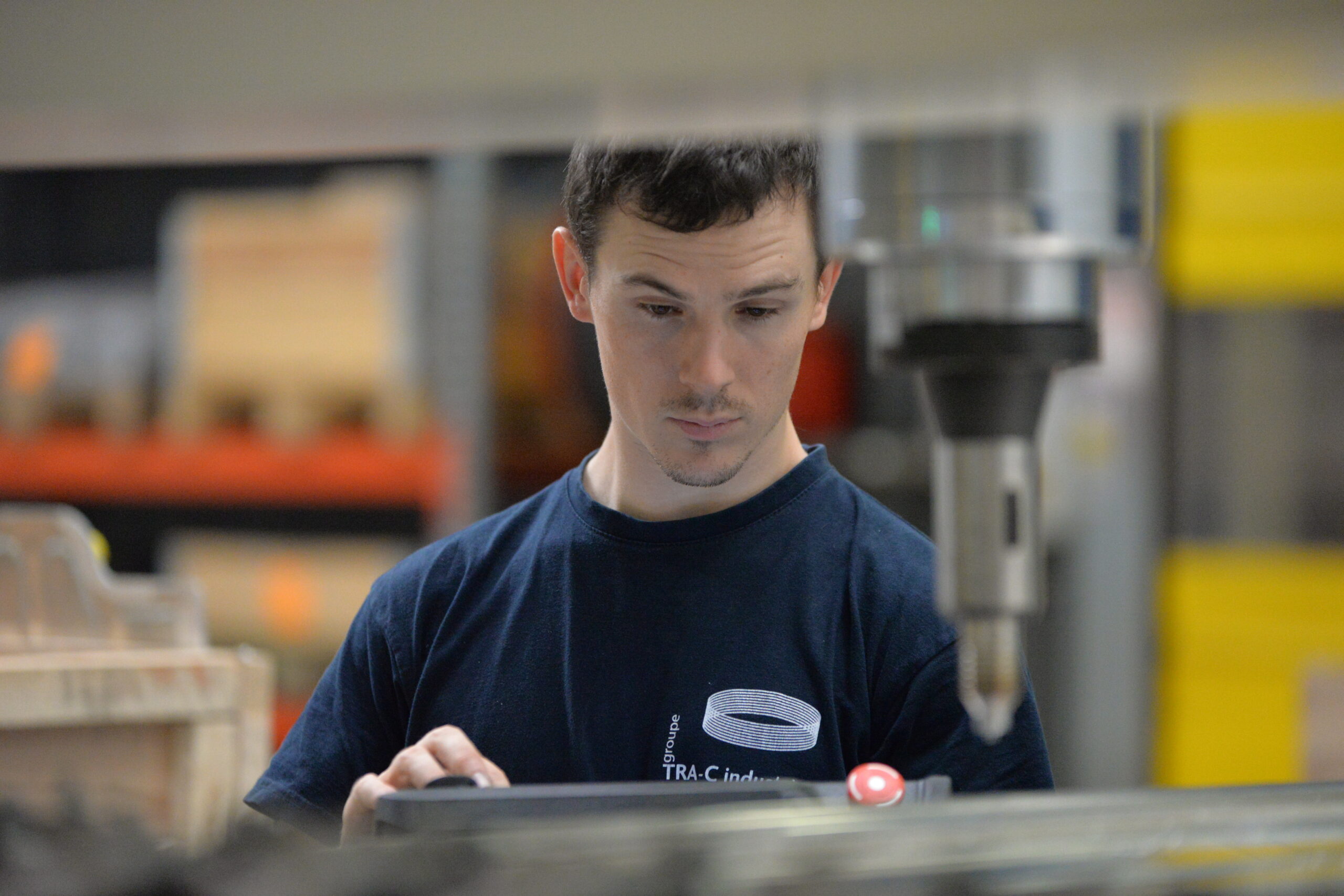

Friction stir spot welding
Friction stir spot welding is a variant of friction stir welding, used in a variety of industries. Unlike linear welding, where the tool moves along the joint, the tool remains in place and rotates on a single point of contact.
This circular movement generates intense heat at the precise point of contact, creating a localized fusion of the materials. After a while, the tool is lifted, leaving behind an excess hole.
The advantages of friction welding
Not all welding techniques are equal, and the choice of the method depends on the materials to be joined. Friction welding does, however, offer a number of advantages that distinguish it from other traditional processes:
- Heterogeneous welding: it can weld more complex configurations than traditional welding (aluminum-copper, aluminum-titanium, etc.), thus broadening assembly possibilities;
- Compatibility with various metals: all forgeable metals can be friction welded. This gives manufacturers great flexibility in the design of strong assemblies;
- More energy-efficient process: no external heat or flux is required. This method is therefore more economical and less restrictive than traditional techniques;
- Increased reliability and speed: with a reduced defect rate and mechanically robust welds, this technique is one of the fastest and most efficient compared to fusion welding;
- Environmentally-friendly process: by reducing energy consumption and the emission of fumes or toxic gases, friction welding also limits its environmental impact and is part of a more sustainable approach;
- Less deformation of materials: as the heat is localized and controlled, parts better retain their mechanical properties. They also undergo less distortion than with fusion welding;
- Excellent repeatability: this automated process finally delivers uniform welds of consistent quality. This makes it ideal for large-scale industrial production.
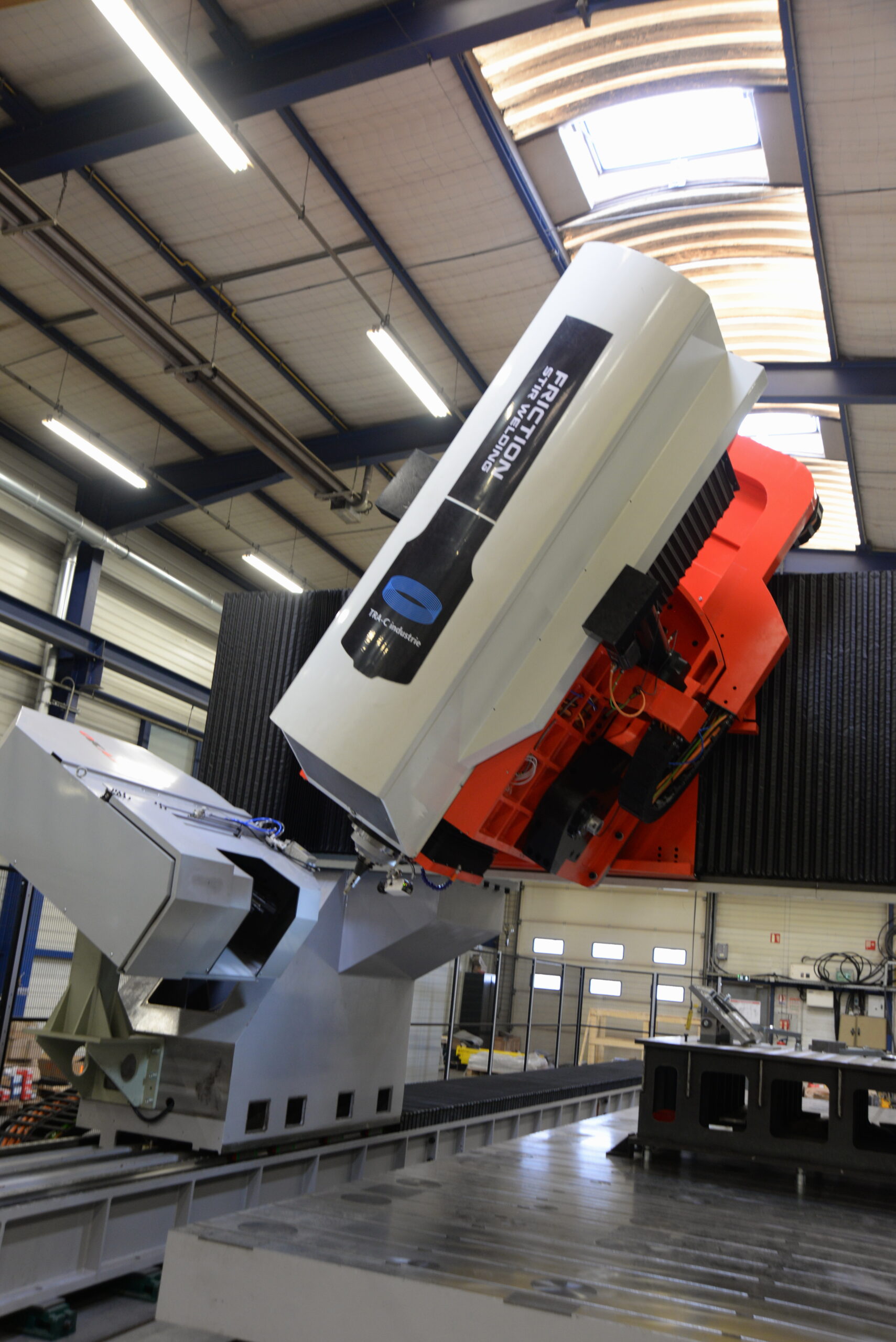
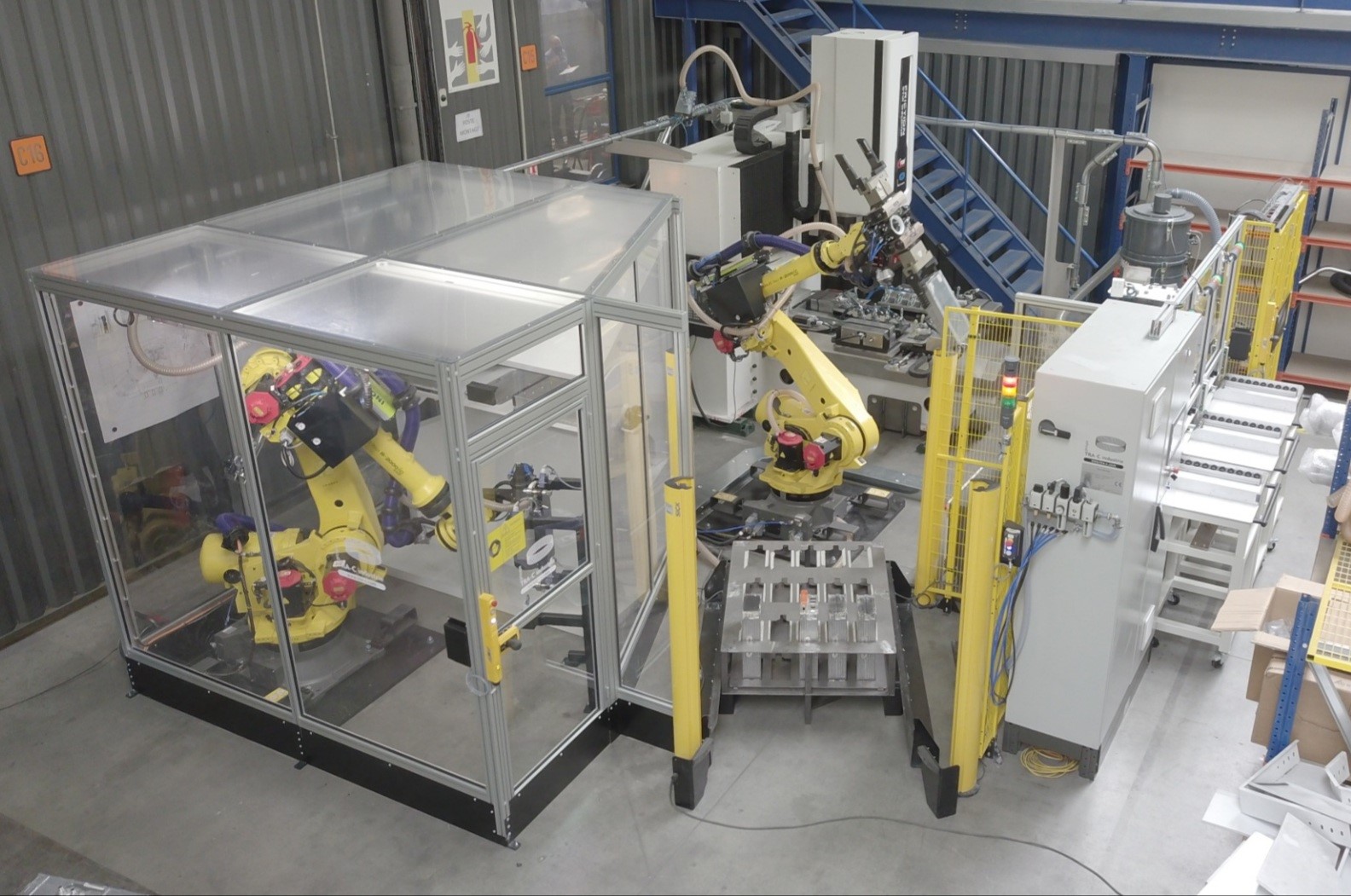
The drawbacks of this welding process
Although friction welding has many advantages, it also has certain limitations. The process requires specialized equipment, which is often costly and bulky. The machines used must apply high forces and speeds, implying a significant initial investment for manufacturers wishing to adopt this technology.
Another drawback is the complexity of the process. Perfect control of parameters such as pressure, speed and duration of friction ensures a quality weld. The wrong configuration can lead to defects or an insufficiently strong bond.
Finally, friction welding is mainly suited to linear or circular assemblies. It is less flexible than other processes for welding complex shapes or structures with irregular geometries, thus limiting its field of application.
What are the different applications for this process?
Friction welding is used in many sectors thanks to its reliability and ability to join various metals. Here are just a few areas where this technique plays a key role:
- Aerospace: it enables the assembly of lightweight, high-strength alloys for aluminum turbine blades and fuel tanks, for example;
- Automotive: thanks to this technique, manufacturers can lighten vehicles and improve the performance of engine and chassis parts;
- Energy: this process is also used to produce high-pressure turbines and equipment requiring flawless welds;
- Railway: it plays a key role in the manufacture of axles and rails, ensuring precise joints and greater safety;
- Medical: used to design implants and surgical tools in biocompatible metals with impeccable finishes;
- Spatial: finally, this technology enables the assembly of lightweight, ultra-resistant structures adapted to extreme conditions.

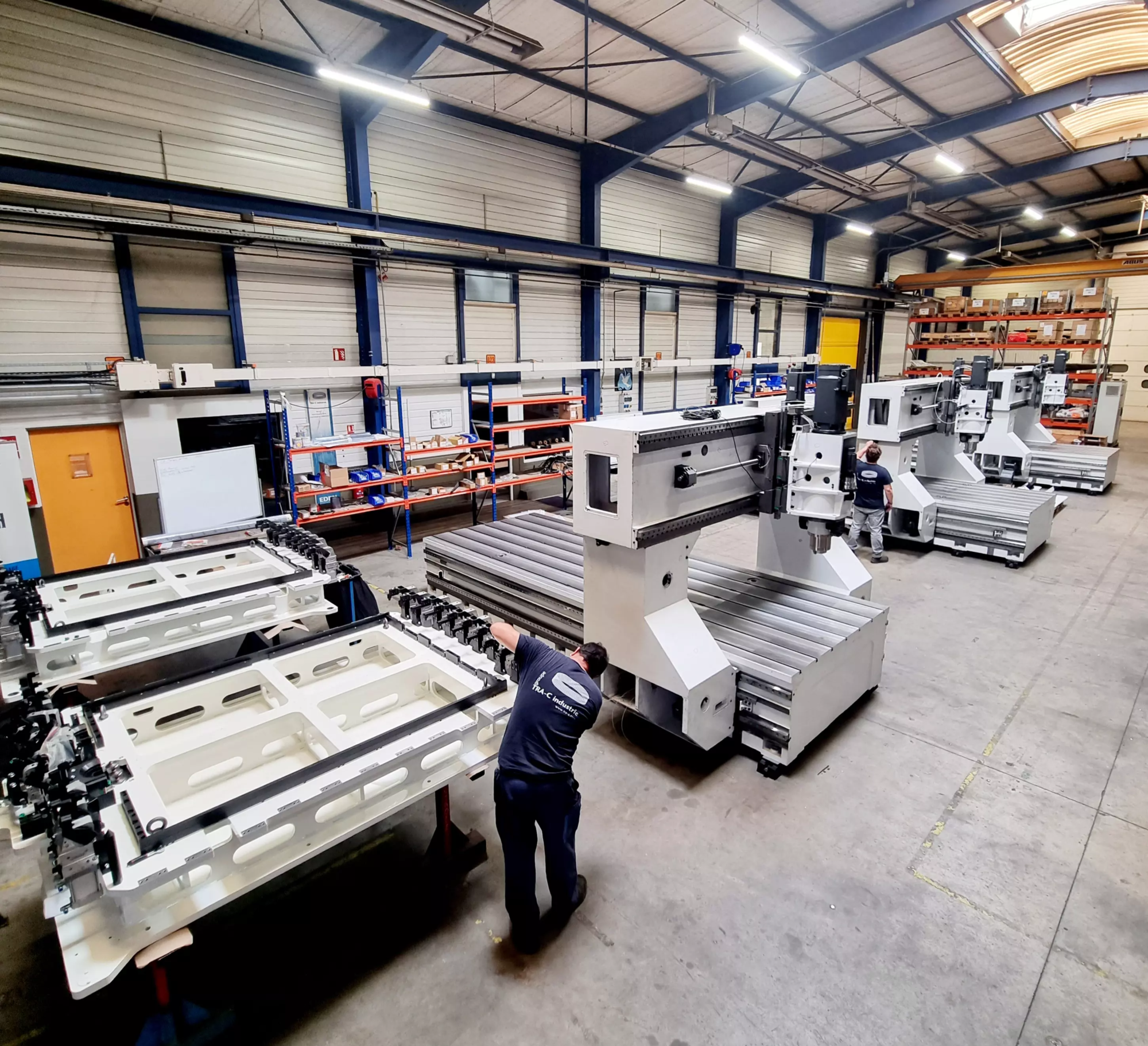
TRA-C industrie, specialist in friction stir welding
A pioneer in friction stir welding (FSW), TRA-C industrie has been involved in this innovative technology since 2009. It contributes to its continuous improvement and integration into the manufacturing industry.
Our commitment to research and development has made us the European leader in FSW welding. By developing new techniques and designing state-of-the-art machines, we push back the limits of industrial assembly and improve the performance of welded materials.
The growing popularity of friction welding for the assembly of complex alloys has strengthened TRA-C‘s expertise. We have developed solutions tailored to the needs of a wide range of sectors, from aerospace and automotive to energy and rail!
TRA-C industrie also works closely with renowned partners, such as UIMM, to advance research and development in this field. As a result, we are constantly innovating, offering our customers ever more effective technologies.