FSW copper welding: challenges and benefits
FSW copper welding is revolutionary. Today, it is essential in many industrial sectors, including electronics, energy and aeronautics. The specific properties of this material make it difficult to assemble using traditional methods!
Friction stir welding (FSW) provides an innovative solution to these challenges. This technique uses friction-generated heat and material stirring to join copper with remarkable quality and precision.
By combining robustness and reliability, FSW reduces common welding-related defects such as cracks and distortion. This makes it the technology of choice to meet the requirements of modern industries looking for high performance…
But what are the challenges of welding copper? What are the advantages of FSW for welding this alloy? And what are the assembly steps? In this article, TRA-C industrie tells you more about the applications, limits and prospects of FSW for copper.
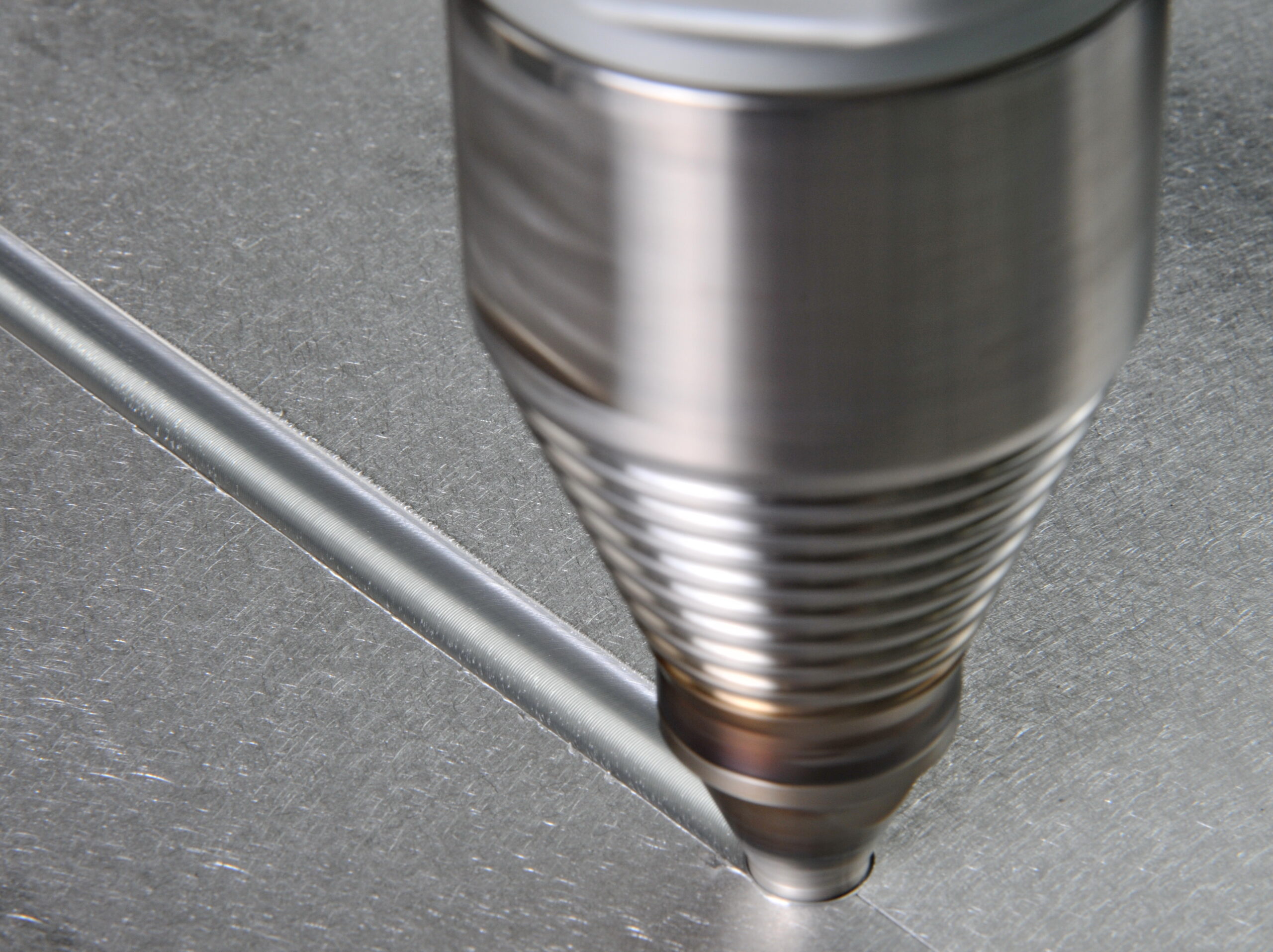
What is friction stir welding (FSW)?
Developed in the 1990s, friction stir welding (FSW) is a solid-state joining process. It uses the heat generated by the friction of a rotating tool to plasticize and mix the materials to be welded.
Unlike conventional welding processes, FSW does not require metals to melt completely. This reduces high-temperature-related defects such as cracks and porosity!
The welding tool presses and kneads the parts, creating a homogeneous weld. This mechanical movement ensures a strong, durable bond between the assembled materials.
Thanks to its precision and ability to join metals such as copper, FSW has become a key technology. It is at the heart of demanding sectors such as aerospace, electronics and energy.
The challenges of copper welding
Copper is known for its exceptionally high thermal and electrical conductivity. In traditional processes, rapid heat dissipation makes it difficult to weld copper and obtain a homogeneous joint.
Furthermore, copper is sensitive to contamination and oxidation at high temperatures, which can compromise the quality of the weld. These problems often lead to defects such as cracks, porosity or insufficient mechanical strength…
Thermal stresses associated with conventional methods also cause significant distortion of copper parts. These distortions are particularly problematic for applications where precision and durability are essential.
In the face of these challenges, friction stir welding (FSW) stands out as an effective alternative. Thanks to solid-state joining, it avoids many of the disadvantages associated with high melting temperatures, while guaranteeing high-quality welds!
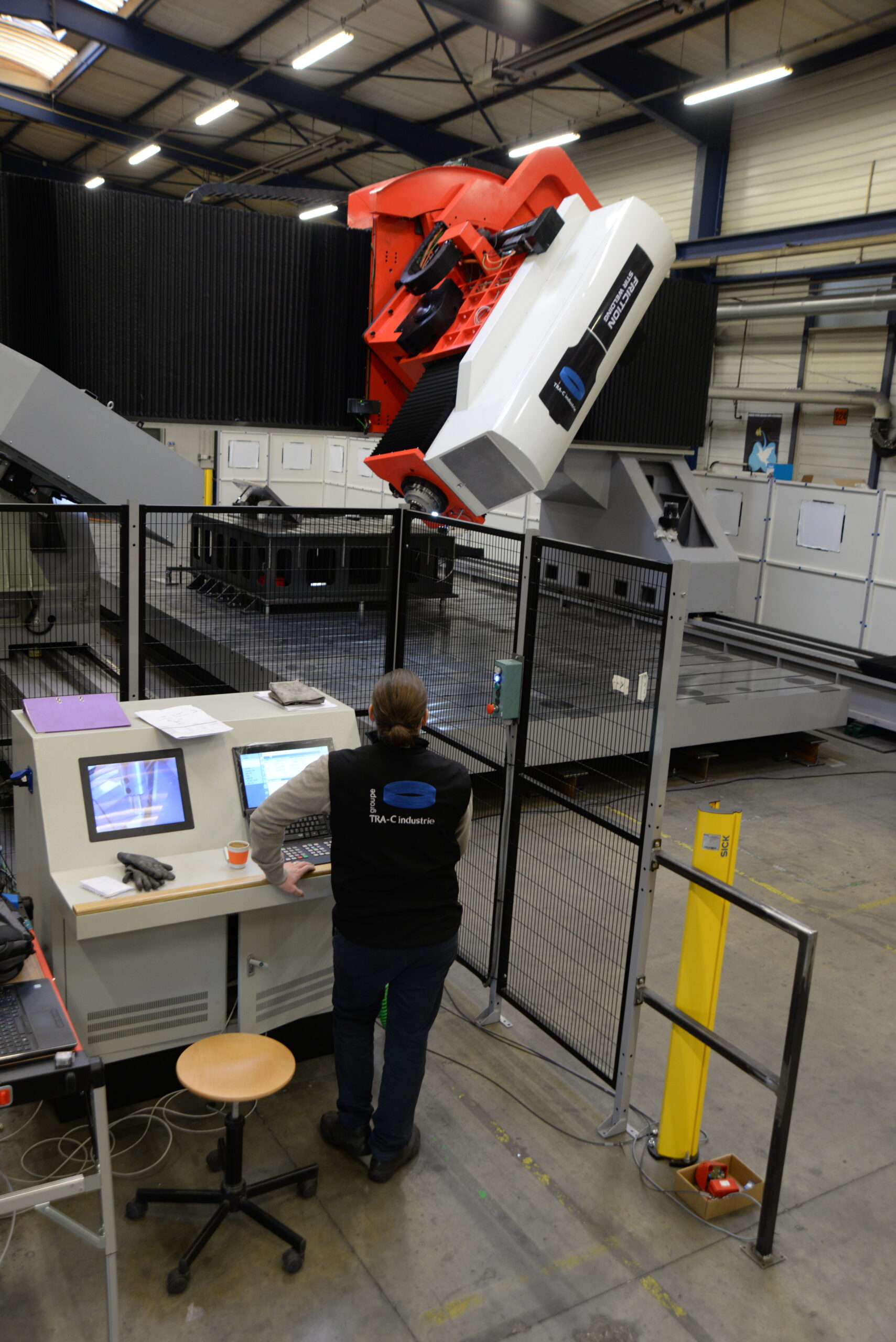
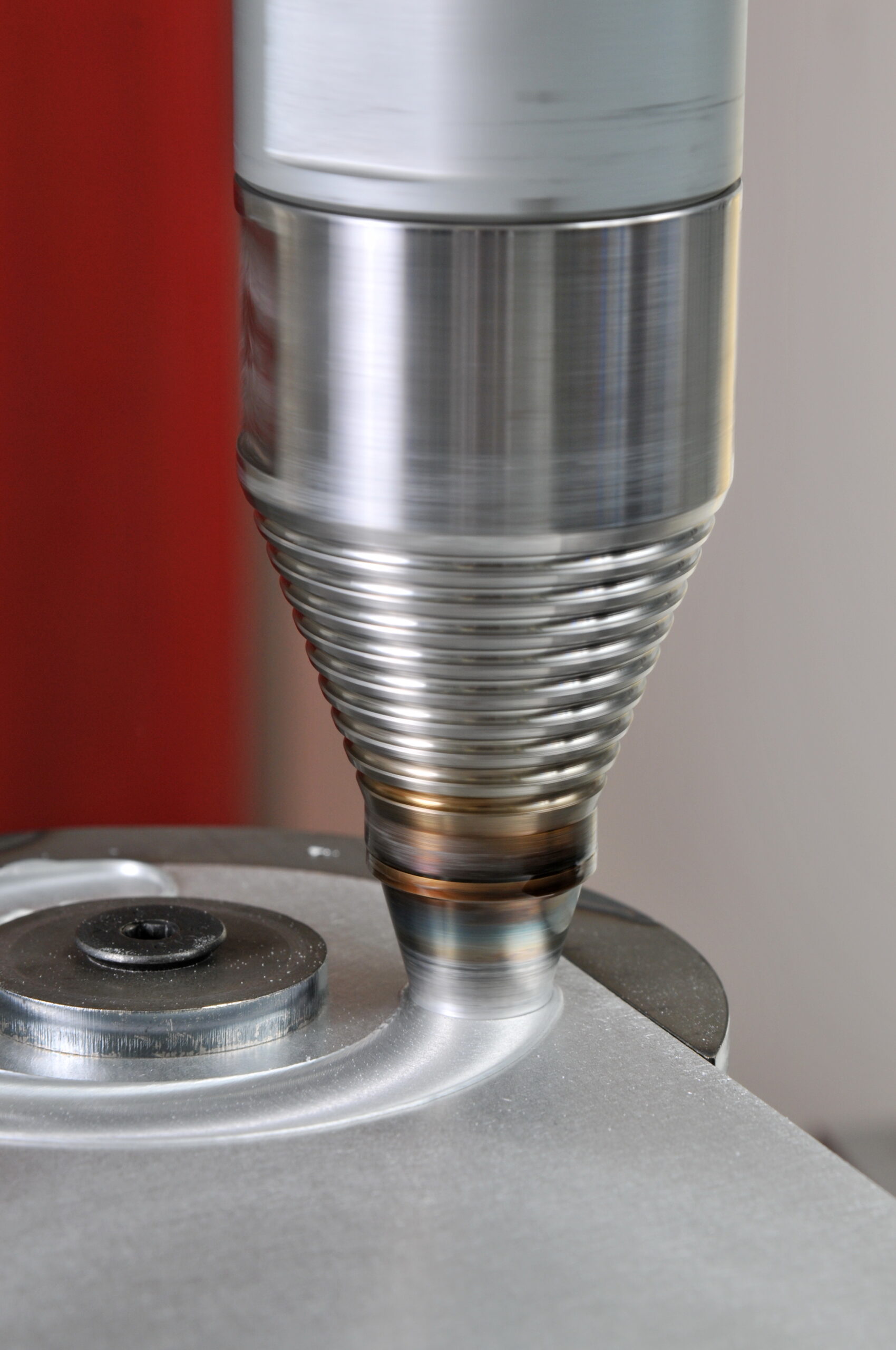
The advantages of FSW copper welding
FSW copper welding offers many advantages, particularly in terms of quality and performance. This welding process overcomes the challenges associated with copper’s thermal conductivity, while producing durable assemblies:
- Reduced soldering defects. First and foremost, FSW minimizes the risk of cracks, porosity and oxidation, which are common when welding copper using conventional techniques. The result is solid, homogeneous welded joints;
- Less thermal distortion. Unlike conventional soldering methods, FSW also limits the effect of thermal stress, preventing deformation of copper parts;
- High mechanical strength of welds. Joints obtained by friction stirring are more resistant to wear and mechanical stress. They therefore make copper welding more durable;
- Improved thermal conductivity of joints. The FSW process also preserves the thermal properties of copper. It ensures optimum thermal conductivity in the soldered areas;
- Adaptability to complex geometries. FSW can also be used to weld complex copper parts without compromising weld quality.
Processes and stages of friction stir welding for copper
The FSW copper welding process begins with the preparation of the parts to be welded. They are carefully aligned and clamped to ensure a stable position during the welding operation.
The rotating tool, designed to resist wear, then comes into contact with the soldering area. It exerts pressure and friction on the parts, generating the heat needed to plasticize the copper without melting it…
During operation, the pin performs a rotary movement combined with linear translation of the tool shoulder. The partial melting of the material thus enables the material to be kneaded. This dual action creates a homogeneous, flawless and solid weld.
Once welding is complete, the parts are cooled slowly. This allows the joints to solidify and regain their mechanical properties. Finally, quality control ensures the strength and durability of the weld!
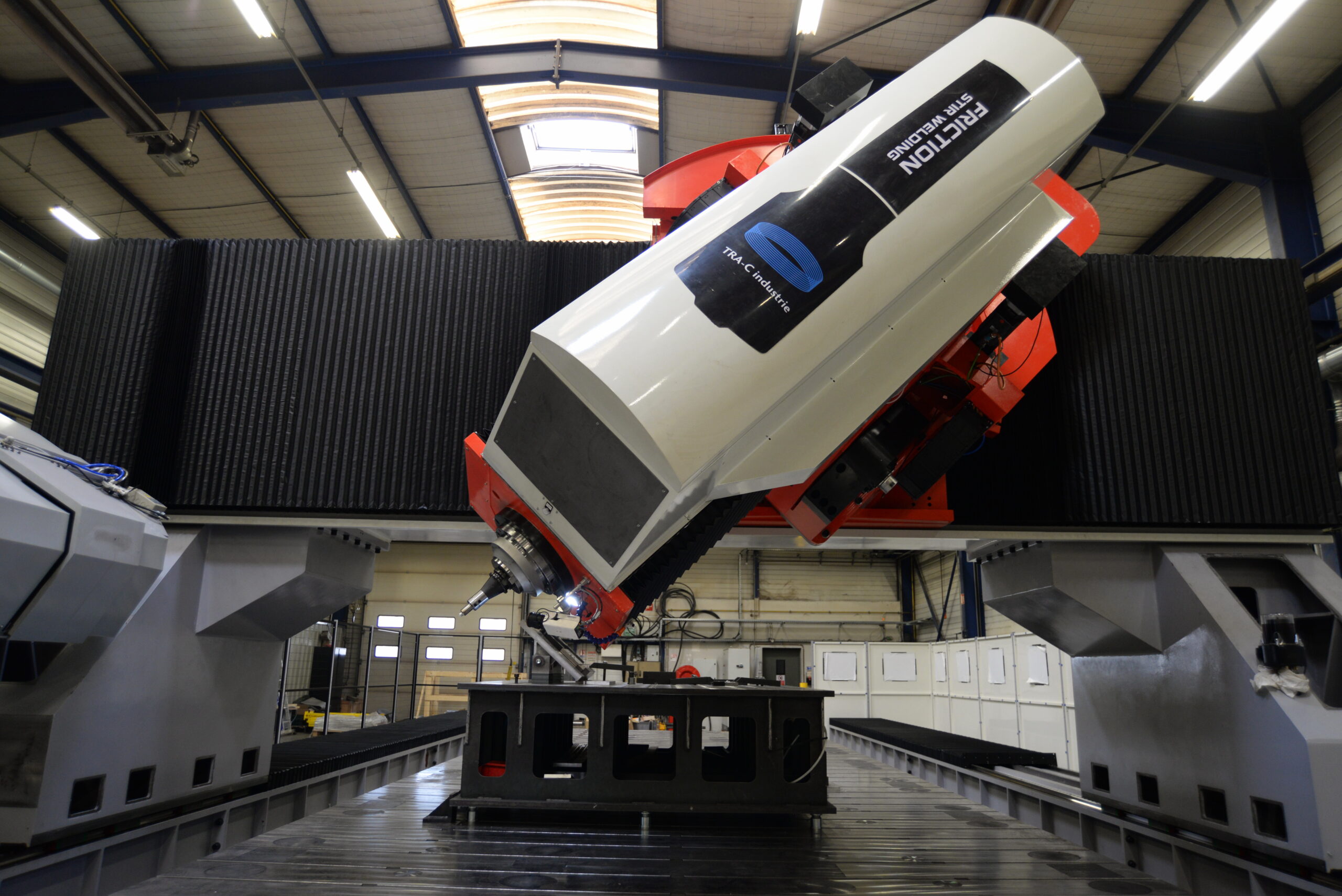

Concrete FSW applications for copper
Friction stir welding is used in a variety of sectors to fully exploit the properties of copper. Its performance makes it an ideal solution for applications requiring durable assemblies:
- Electronics sector: FSW is used to solder electrical connectors and copper busbars, guaranteeing excellent conductivity and durability;
- Energy sector: this process is also ideal for assembling components for electrical and thermal systems, such as heat exchangers or solar collectors;
- Aerospace industry: FSW copper welding is popular for cooling systems and high-performance electrical components used in aircraft and satellites;
- Automotive industry: in electric vehicles, FSW is used to join batteries and copper components, ensuring optimal conductivity and increased reliability;
- Railway industry: this welding process is also used to solder copper electrical components in high-speed trains and signalling systems;
- Shipbuilding: friction stir welding is finally being used to assemble copper components for on-board electrical systems and heat exchangers in modern ships.
Limits and prospects of friction stir welding for copper
Despite its many advantages, friction stir welding has certain technical limitations. For example, rapid tool wear due to FSW copper welding, due to its high thermal conductivity and hardness, remains a challenge to overcome.
This process also requires specific and costly equipment, such as FSW machines adapted to the alloys and dimensions of copper parts. This may limit its adoption by small companies or for low-volume production…
However, the prospects for innovation are promising. Current research is aimed at developing stronger tools and optimizing the process to improve durability and reduce costs. These advances will broaden the range of applications for FSW.
With the growing demand for sustainable and efficient solutions, FSW copper welding will play a key role in the industry. Its potential in emerging technologies such as renewable energies and electric vehicles suggests a promising future!
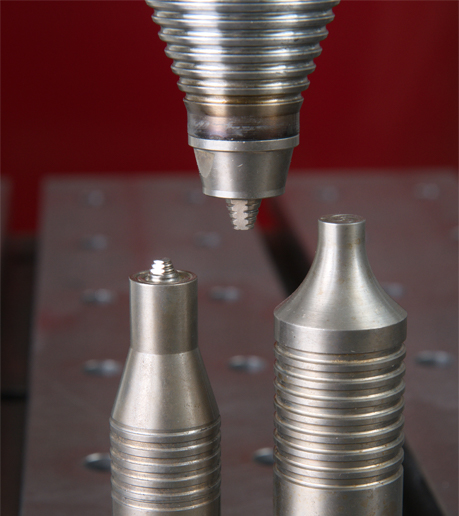
Entrust your industrial projects to an expert in FSW copper welding
For industrial projects requiring reliable, high-performance solutions, it’s essential to rely on qualified experts. Their experience ensures assemblies tailored to the requirements of each sector, particularly for FSW copper welding.
TRA-C industrie is the partner of choice for your industrial projects. Leader in friction stir welding in Europe, the company offers innovative welding solutions, particularly for complex materials such as copper.
Thanks to our state-of-the-art equipment and mastery of the FSW process, we can offer tailor-made services: needs analysis, engineering design, production of welded parts, process automation, operator training…
Finally, we rely on reputable suppliers to meet the most complex technical challenges and the growing expectations of modern industries. TRA-C industrie works with trusted partners such as Fronius, Roboprod and UIMM.