FSW in the rail industry: challenges and benefits
FSW in the rail industry is an innovative technology that is attracting growing interest. Used to join lightweight materials such as aluminum, it meets the performance and safety requirements of modern rail transport…
Friction stir welding (FSW) is a solid-state welding process. The heat generated by the friction of the tool on the parts to be welded is used to soften the material and thus, to join the materials.
This process stands out for its ability to reduce production costs and offer greater durability for welded components. It improves the competitiveness of rail companies by reducing the need for vehicle maintenance!
But what are the challenges facing the rail industry? What are the benefits of FSW for this sector? And what are the process’s current applications? TRA-C industrie, experts in FSW welding, tell you more about friction stir welding and its advantages.
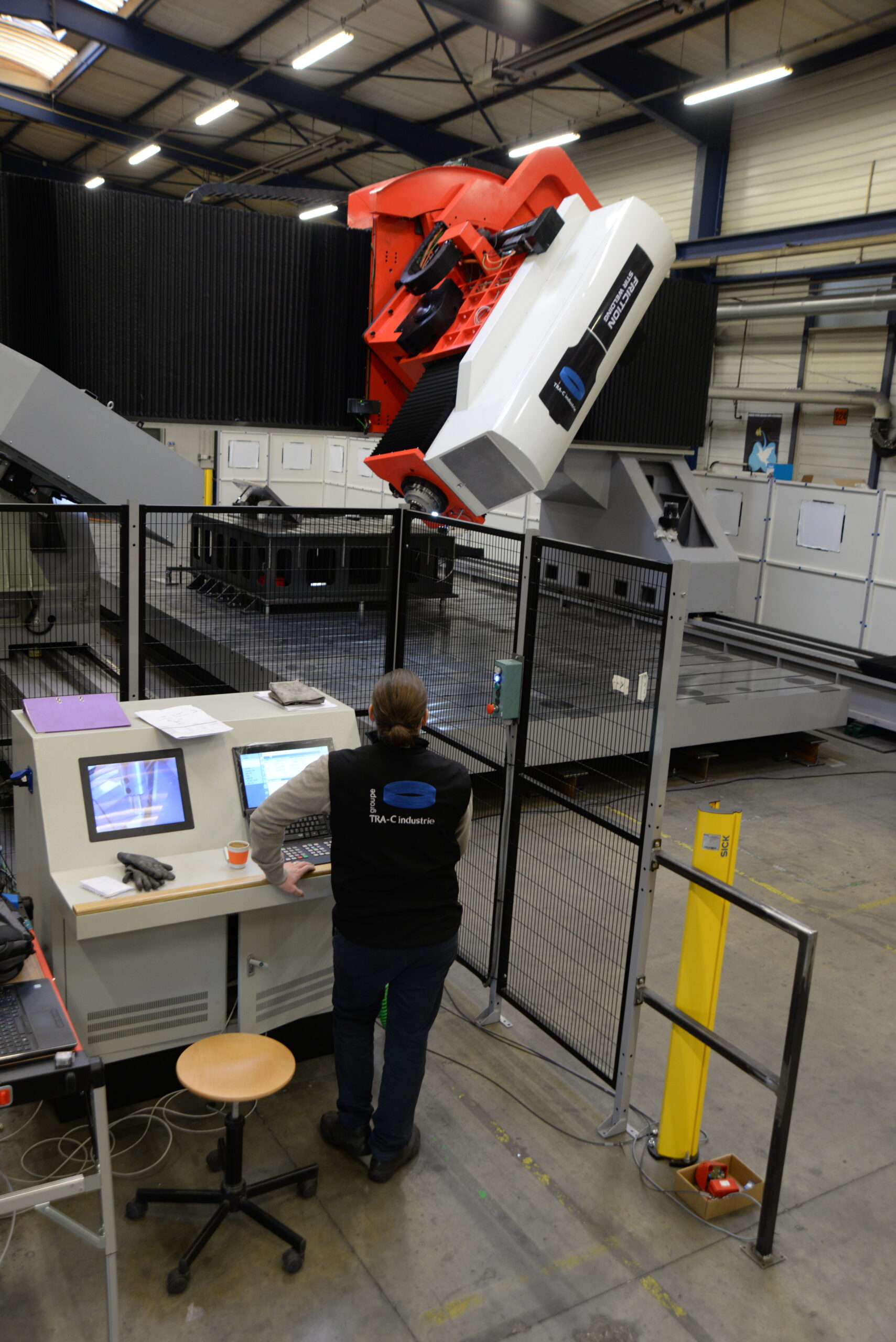
Welding challenges facing the rail industry
The rail industry is particularly demanding when it comes to component safety and durability. The challenges facing this sector in terms of welding are therefore numerous. These include :
- Safety: in the railway sector, the reliability of welds is essential to guarantee the solidity of structures. Processes must meet strict safety standards to prevent failures during operation;
- Durability: welds must also withstand environmental conditions, vibrations and intense mechanical forces. Increased durability extends train service life and reduces maintenance downtime;
- Energy efficiency: lighter welds make it possible to design trains that consume less energy, improving their performance. They thus help to reduce the rail industry’s carbon footprint;
- Cost reduction: by optimizing welding techniques, material and labor requirements can be reduced. The use of more efficient processes also reduces rework and defects, thereby cutting production costs;
- Innovation: the adoption of new welding technologies offers better assembly quality with fewer metallurgical defects. This enables to meet ever-increasing performance requirements.
Interests of FSW in the rail industry
FSW in the rail industry offers many advantages, particularly in terms of performance, efficiency and durability. This innovative process is increasingly being adopted to meet technical and environmental challenges:
- Weld quality: first and foremost, FSW produces welds free of porosities and cracks. This improves the strength and reliability of assemblies, and reduces the risk of long-term failure;
- Cost reduction: FSW requires neither filler materials nor shielding gas, which reduces production costs. In addition, the reduction in weld defects means fewer rework operations and less quality control;
- Faster production: friction stir welding also increases productivity. The welding speed is in fact 3 m/min, which means significant time savings for manufacturers;
- Energy efficiency: thanks to lighter assemblies, FSW contributes to the design of more energy-efficient trains. The result is lower CO2 emissions, making the rail sector more environmentally friendly;
- Increased durability: FSW welds also offer excellent resistance to mechanical and thermal stress. They extend component life, reducing maintenance requirements.
- Process automation: FSW can be easily integrated into automated production processes. This reduces human error and increases weld repeatability and efficiency;
- Reduction on noise and vibration: FSW welds are also known for their improved acoustic properties. They help reduce noise and vibration in trains, thus improving passenger comfort;
- Adaptation to complex welds: FSW is particularly effective for complex geometries. They are ideal for hard-to-reach areas or long assemblies, such as train bodies and structures.

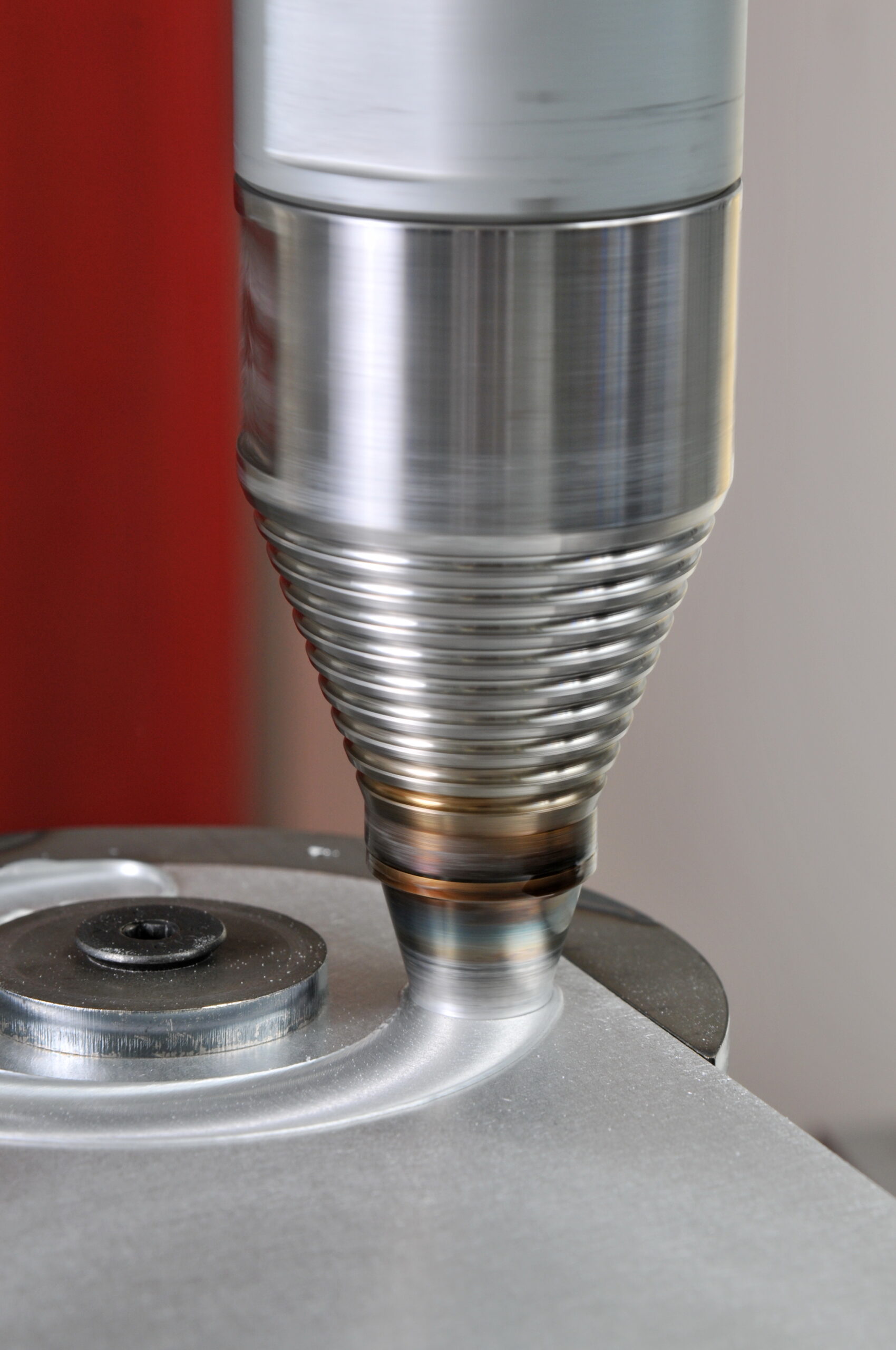
Friction stir welding challenges for rail industry players
FSW in the rail industry, while promising, presents a number of challenges for industry players. The initial investment in specialized equipment is high, which may slow down its adoption in some companies…
Secondly, although this welding process is effective for materials such as aluminum, it remains more complex to apply to harder steels or alloys. This further limits its use for certain parts of trains.
What’s more, implementing friction stir welding requires specific expertise and operator training. The skills required to optimize this process may represent an obstacle for some traditional industries.
Finally, although FSW can be automated, integration into existing production lines can be costly and time-consuming. The adjustments required to guarantee weld quality in a variety of environments therefore remain a major challenge.
Concrete applications of FSW in the rail industry
FSW in the rail industry has many concrete applications, offering solutions tailored to the need for lightness, durability and performance. The process is used in various components to optimize the manufacture of modern trains:
- Assembly of aluminum bodies: FSW was first widely used to assemble aluminum body panels. It reduces the overall weight of trains while guaranteeing strong welds;
- Wagon floor manufacture: FSW welds are also used to join aluminum or light-alloy floor sections. They ensure strength and resistance to vibration during operation;
- Tank and container production: FSW is also ideal for welding large tanks and containers. The tightness and strength of joints are essential to avoid leaks;
- Cabin wall assembly: thanks to FSW, driver’s cabs benefit from strong, aesthetic welds. This welding process enhances safety while maintaining a neat appearance;
- Design of bogie structures: FSW is finally used in the manufacture of bogie components. The mechanical strength of these components is essential to support loads and ensure train stability.

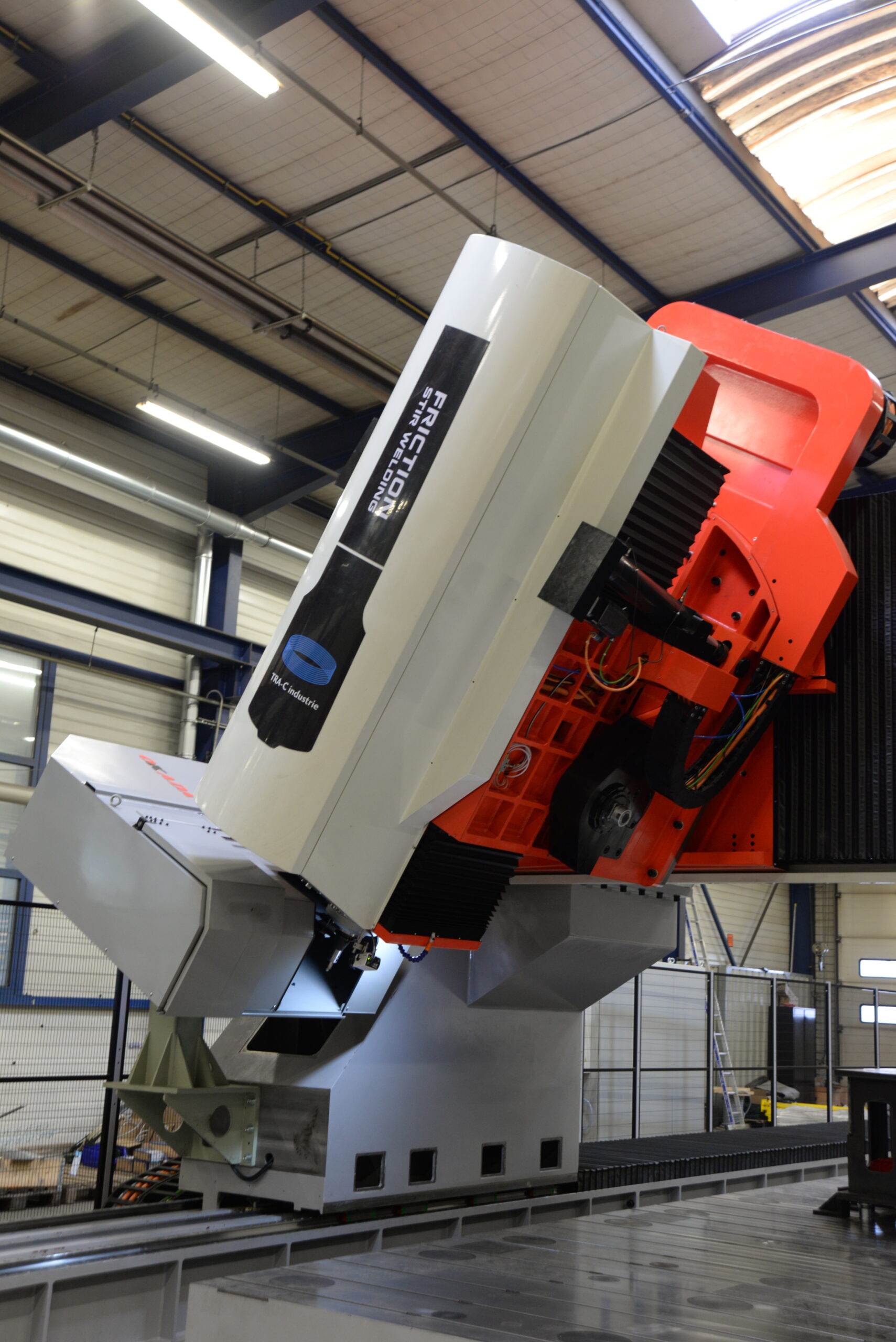
FSW innovations and developments in the rail sector
Innovations around FSW in the rail industry focus on improving the weldability of complex materials. Research is underway to extend friction stir welding to steel alloys and other more resistant materials…
What’s more, the development of automated and robotized systems for FSW speeds up production, while guaranteeing consistent weld quality. These advances facilitate the integration of FSW into modern production lines.
Innovations also focus on reducing the energy footprint of the process. By optimizing FSW parameters, it is possible to reduce energy consumption while improving the mechanical performance of welds!
Finally, intelligent sensors and real-time control systems are being developed to monitor and adjust welding conditions. They ensure more precise quality monitoring and optimize production in a demanding rail environment.
TRA-C industrie, specialist in FSW in the rail industry
Recognized player in the field of friction stir welding, TRA-C industrie has particular expertise in FSW for the rail industry. The company stands out for its innovative solutions, adapted to the quality and durability requirements of railway components.
Specialized in aluminum assembly, we contribute to the manufacture of lighter, more efficient and environmentally friendly trains. Our FSW technologies improve energy efficiency and strength of welded structures!
TRA-C industrie also offers customized services for the integration of FSW into railway production lines. Thanks to our equipment and know-how, we can help companies modernize their welding processes.
We also hold certifications such as ISO 9001 and ISO 25239, attesting to the quality of our assemblies. The EN 15085 standard allows us to subcontract according to the rules of the trade. Finally, we work with reputable partners such as Constellium and Alstom…
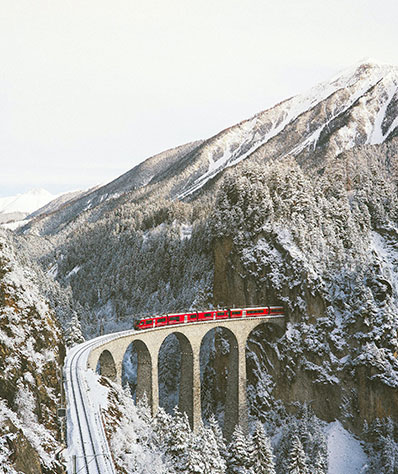