FSW in the automotive industry: challenges and benefits
Friction stir welding, or FSW in the automotive industry, represents a major step forward due to its many advantages. Today, it is indispensable in a sector that is constantly seeking to improve vehicle performance, safety and durability.
Friction stir welding is a unique process that enables parts to be welded together in a solid state, without the need to melt material or to add filler metal. It is the combination of friction and heat generated by a rotating tool that creates the welded joint.
This method produces solid, homogeneous assemblies, free from common defects associated with fusion welding techniques. FSW is therefore particularly well suited to the automotive industry, where weld quality is essential.
But what are the welding requirements in the automotive sector? What are the applications of FSW in this field? TRA-C industrie tells you more about the uses and benefits of friction stir welding in the automotive industry…
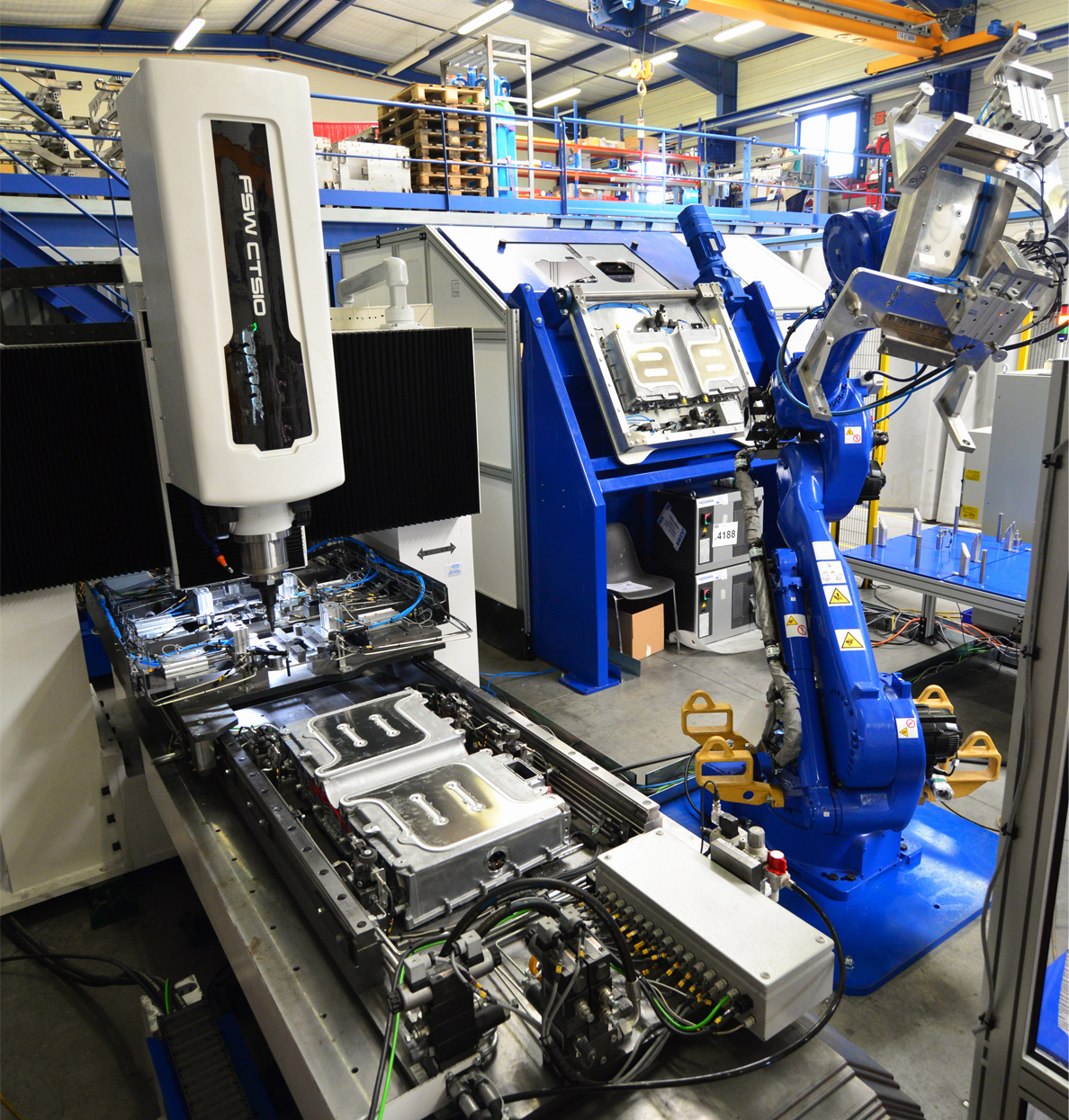
Welding needs and challenges in the automotive sector
The automotive industry is a dynamic sector. To remain competitive, car manufacturers must meet increasingly demanding requirements in terms of performance, safety, energy efficiency and sustainability:
- Vehicle weight reduction: the use of lightweight materials such as aluminum and composites reduces vehicle weight. This improves their energy efficiency ;
- Improved weld quality: vehicles also have to withstand considerable mechanical stress and a wide range of operating conditions. Durable welds guarantee the reliability and longevity of components;
- Energy efficiency in production: reducing energy consumption during manufacturing is a priority for minimizing our environmental footprint. Welding methods that consume less energy are particularly sought-after;
- Design flexibility: with the rise of electric and hybrid vehicles in the e-mobility sector, design is becoming increasingly complex. Welding techniques have to adapt to complex material configurations;
- Reducing production costs: finally, car manufacturers are constantly looking for ways to optimize their processes and cut costs. Welding automation is a key element of this optimization.
What are the advantages of FSW for the automotive sector?
FSW in the automotive industry offers significant advantages over traditional welding methods. It therefore meets the growing demands of this sector:
- Improved weld durability: first and foremost, FSW produces very high-quality welds, characterized by excellent mechanical strength. The absence of material fusion minimizes defects and creates more homogeneous welds;
- Vehicle weight reduction: FSW can also be used to weld lightweight aluminum and aluminum alloys. This assembly process thus contributes to the design of lighter, more fuel-efficient vehicles;
- Energy savings: compared with fusion welding technologies, FSW generates less heat to create welds. The result is substantial energy savings;
- Production efficiency: FSW is automated. It enables mass production with consistent quality and reduced labor costs. As a result, car makers can optimize their manufacturing processes;
- Improved vehicle safety: FSW welded joints offer improved fatigue resistance and impact tolerance. This improves overall vehicle safety, a major priority in this sector;
- Adaptability to modern designs: this technology is ideal for welding battery components, aluminum structures and composites. It facilitates the integration of innovative architectures and designs;
- Reduced environmental impact: unlike conventional methods, FSW requires no flux, protective gas or filler metal. This reduces CO2 emissions by 50%. It also uses less energy and produces less waste. It is therefore an environmentally-friendly welding process.
- Sealing of weld joints: FSW finally produces homogeneous joints, without fusion, solidification or filler metal. This eliminates porosity, cracks and common defects found in conventional welds.

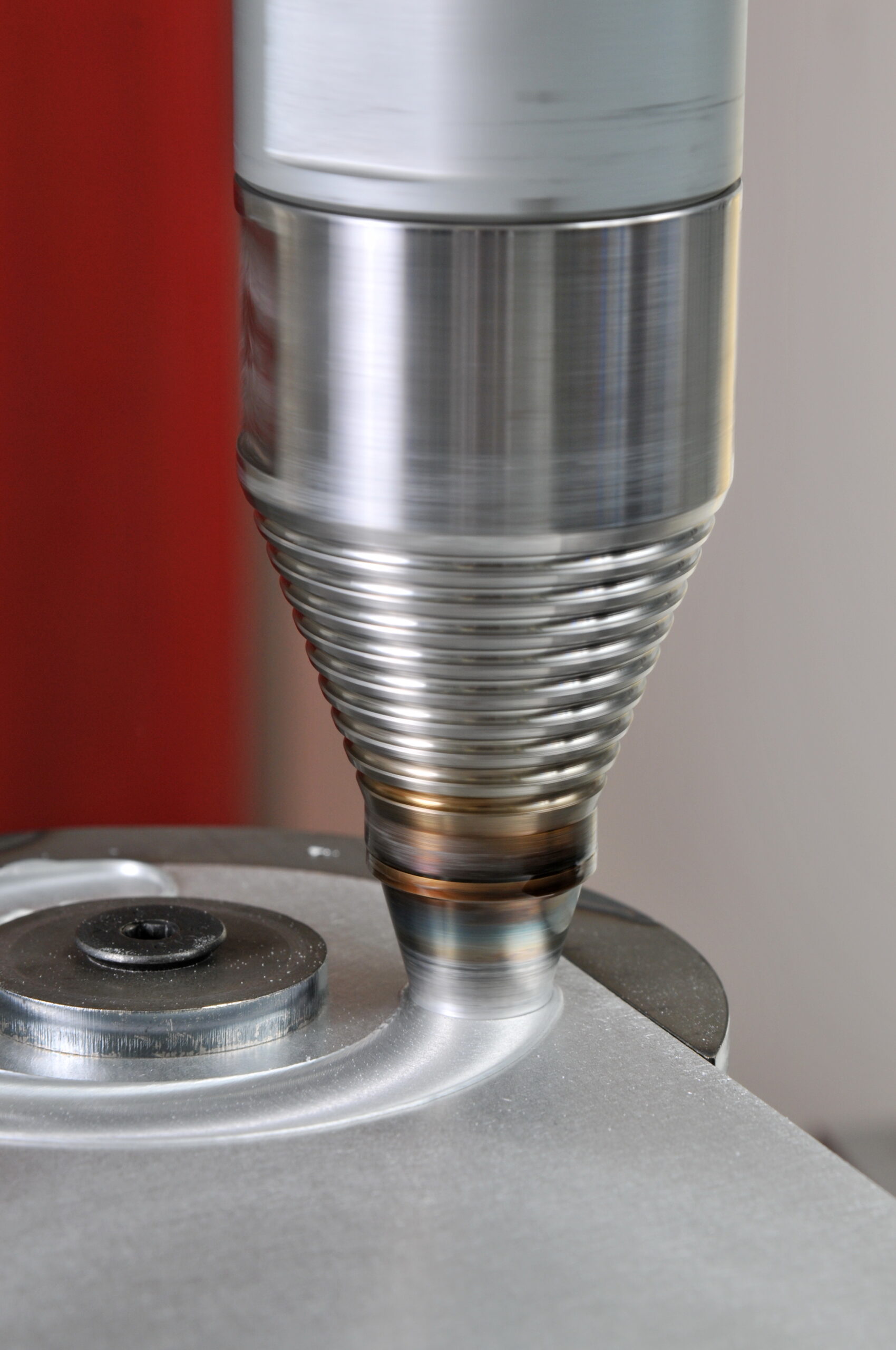
Current applications of FSW in the automotive industry
One of the most common applications for FSW in the automotive industry is chassis assembly. The process is particularly well-suited to weld chassis components made of aluminum, a material used for its lightness and strength.
Body panels also benefit from FSW technology. This method produces discrete, solid welds, essential for maintaining the structural integrity of roofs, hoods and doors, while offering a high-quality finish.
Fuel tanks and safety structures must meet strict standards. FSW enables the creation of corrosion-resistant, robust welds, essential for fuel tanks, door reinforcements and protective bars.
Electric vehicle batteries contain electrical components that require so-called “cold” welding to prevent damage. FSW makes it possible to weld these components without causing thermal damage.
Last but not least, this technology enables durable assembly of various structural components, such as side members, crossmembers and suspension brackets. These parts have to withstand high dynamic loads and varied driving conditions.
Challenges of integrating friction stir welding in the automotive industry
Integrating FSW in the automotive industry first requires the development of specific tools for different materials and thicknesses. Their design is complex and costly, requiring extensive research and development.
Another challenge is to automate the FSW process. It requires in-situ control systems to guarantee a constant level of quality. The use of real-time monitoring technologies enables anomalies to be detected and corrected instantly.
Differences in the thermal and mechanical properties of material combinations, such as aluminum and steel, also make it difficult to create joins. Welding parameters must therefore be optimized for each combination.
Finally, developing the skills of operators and engineers is essential for optimum integration of friction stir welding. Specialized training programs help maximize the benefits of this technology.

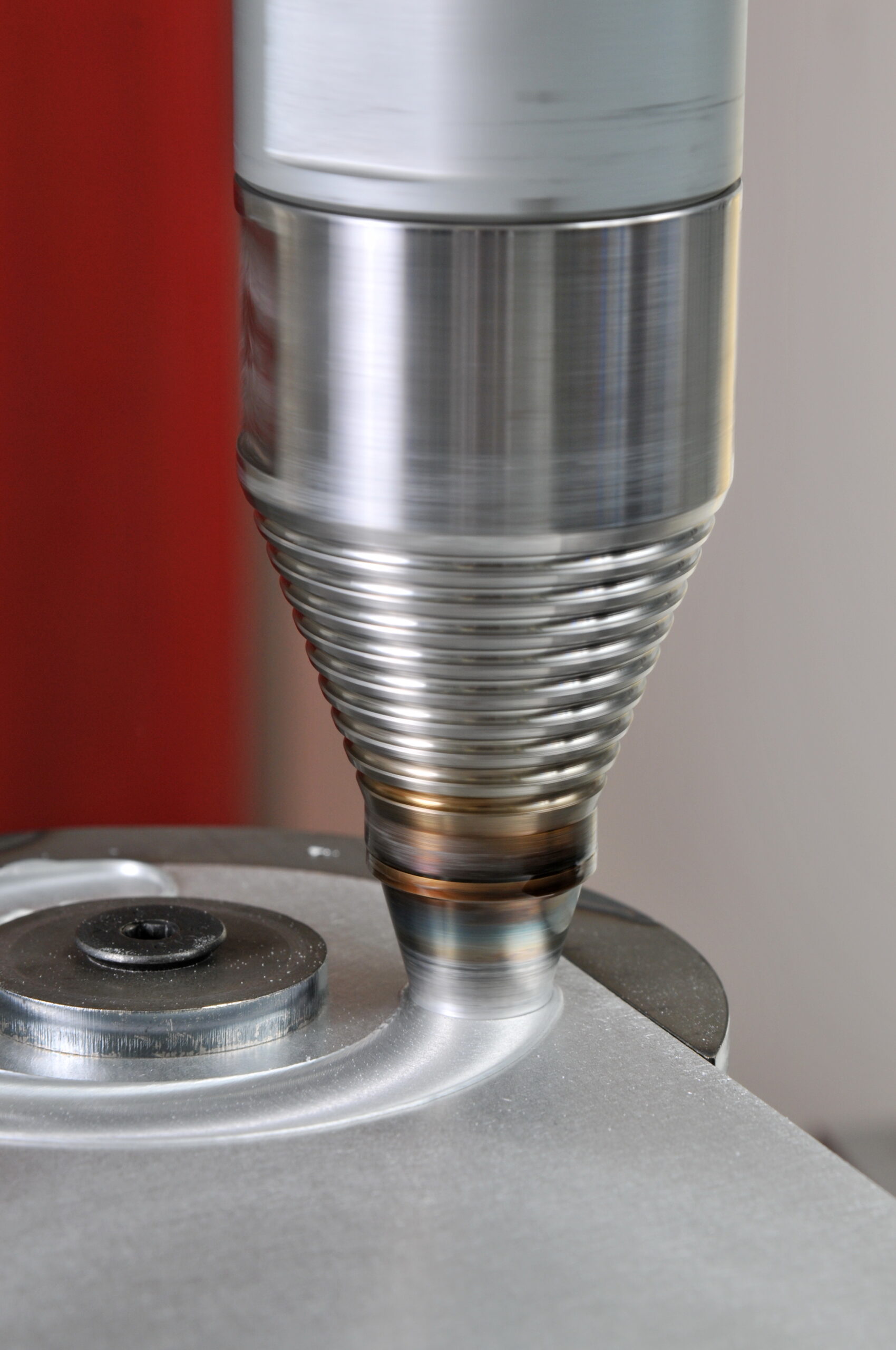
FSW innovations and developments in the automotive sector
FSW in the automotive industry continues to evolve at a steady pace, offering promising perspectives for the future of the sector. Current developments and trends suggest several avenues of evolution that could push back the current limits of this welding technique.
First and foremost, increasing welding speed is a major objective in terms of productivity gains. The development of new machines, combined with appropriate control techniques and tooling, aims to achieve such a goal.
Improved in-situ control using machine data also offers prospects for guaranteeing continuous weld quality. By integrating advanced sensors and monitoring systems, machines will be able to adjust welding parameters in real time to optimize results.
Last but not least, the development of related techniques such as RFSSW (Refill Friction Stir Spot Welding), SSFSW (Stationary Houlder Friction Stir Welding) and FSD (Friction Stir Deposition) opens up new application possibilities and broadens the fields of use.
These technological advances promise to position FSW as an essential welding method. It offers innovative solutions to the various challenges facing the industry…
TRA-C industrie, expert in FSW in the automotive industry
Nowadays, FSW in the automotive industry is a leading technology for building safer, lighter and cheaper vehicles. This process enables car makers to meet today’s challenges in terms of performance, safety and durability.
To help you integrate this technology into your manufacturing processes, TRA-C industrie, leader in friction stir welding, supports you at every stage of your automotive welding project: design in the engineering design office, assembly in the workshop, consulting…
We are also experts in robotized cells and welding automation systems. Our team can analyze your specifications, integrate your machines, install, maintain and train your operators.
We also rely on trusted partners and suppliers who are specialists in the field of industrial robotics. We draw on the experience of Fronius and Hurco, to name but a few, to help you achieve your production goals.
Finally, TRA-C industrie took part in the drafting of the ISO 25239 standard. These regulations attest to our expertise in friction stir welding of aluminum alloys. We can therefore guide you in the production of your pieces in small, medium and large production runs.